Richard Hipkiss, development director for the Modular & Portable Building Association (MPBA), considers the role digital construction technology has to play as offsite rapidly becomes the preferred delivery model
The government and the wider public sector play a pivotal role in encouraging and facilitating the uptake of Modern Methods of Construction. Progressive building systems that deliver at scale and increase productivity are now in great demand.
Historically, manufacturing operations have been considered extensions to construction processes instead of an integral and important part. This perception is changing. As offsite becomes an increasingly dominant force that utilises high levels of digital construction technology, the lines between manufacturing, engineering and construction have become blurred – creating a need for new skills and redefining existing ones.
Benefits of volumetric modular technology
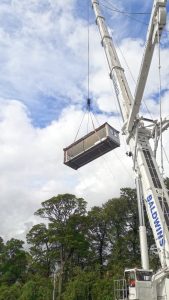
Volumetric modular technology offers benefits that have a huge positive impact on the construction industry, bringing longstanding traditional practices up to date. The first key shift away from traditional methods is that build processes take place in controlled factory conditions. The far-reaching implications of this require a change of mindset and approach.
At the core of volumetric modular production, Design for Manufacture and Assembly (DfMA) protocols and Building Information Modelling (BIM) enable optimal configuration of offsite solutions by connecting multidiscipline and multi-tier teams right from the beginning of the design development process.
DfMA facilitates early design detail and three-dimensional design information, while BIM minimises the risk of errors by eliminating the time-consuming process of translating engineers’ information into cutting lists and assembly drawings. BIM also enables the optimising and testing of designs in virtual and pre-production environments.
Technology is ever evolving, and the volumetric industry is now integrating BIM and digital design specifications with Enterprise Resource Planning (ERP) and Material Requirement Planning (MRP). This technology permits manufacturing simulation and visualisation, clash detection and virtual onsite assembly modelling, which can be enhanced using augmented and virtual reality. Digital construction technology is as relevant to the offsite manufacturing process as it is to design and architecture.
Modular construction makes up 60-70% of offsite
Offsite technology encompasses a variety of panelised and volumetric methods of construction. At the forefront of offsite techniques, volumetric manufactured buildings have a remarkable impact on reducing costs while increasing quality and safety measures. Having gained considerable momentum over the past few years, modular construction makes up 60-70% of offsite techniques and reduces build times by an impressive 50-60%.
Module selection is influenced by transportation dimensions and shipping distances. A number of other factors are also holistically considered to achieve optimal design efficiency. Connection details for example together with specific site logistics, such as foundation/transfer deck requirements, installation and crane costs.
The demand for customisation has led the manufacturing industry to develop methods for adaptation during mass production while meeting specific customer needs. Each individual material can be selected specifically for its performance characteristics, tailoring every inch of a modular build. Eco-friendly materials are often specified, and waste is recycled or reused.
As units are factory manufactured, stringent quality control processes can be undertaken within these well-managed environments. These in-house conditions also prevent weather from inhibiting the manufacturing process, guaranteeing efficiency. On top of this, modular construction enables site work and building processes to be completed simultaneously, reducing labour costs and build times.
Quality and safety with modular
Volumetric modular practices augment the construction industry with a multitude of benefits that span from greener, healthier environments to maximised sustainability, heavily reduced costs and quick build times.
With modular construction, all data can be validated and coordinated as part of a structured process, which helps provide accurate and reliable information for clients at the point of handover. It also means it is easier to identify what products and material specifications were used on previous projects should any legislation changes occur.
By verifying the materials and products to be used on a construction scheme and by simplifying the onsite assembly process, volumetric modular construction offers developers an opportunity to avoid many traceability issues. Modular construction helps ensure client satisfaction and product assurances through the certainty and quality embedded into the build process.
With its powerful combination of controlled deliverables and customisable outputs, modular construction provides the repeatable quality and safety needed to meet client demands.
Richard Hipkiss
Development Director
Modular and Portable Building Association (MPBA)
Tel: 02475 90 1938
*Please note: This is a commercial profile