Nick Atkinson, Company Director at Ambar Kelly explores the need for fire protection in risers during construction
Despite their global use, riser shafts are consistently designed in a piecemeal manner rather than as part of a holistic approach.
With the attention being on the working at height and the risk of falling through riser openings (holes), one’s focus naturally becomes managing risk, as opposed to designing out the risk in the first place.
The riser is the only area of a multi-storey building’s floor plate where there is no designed floor. Add to this the silo mentality in construction, focusing on the visible risk and not the invisible risk of fire becomes even greater.
Coupled with the ever-present focus on the bottom line, the main objective becomes acquiring a product with the lowest cost and managing the obvious safety risk of working at height. As a result, the less obvious but fatal risk of fire in risers during construction is masked and neglected.
Ambar Kelly is a manufacturer of a permanent modular riser flooring solution
Our focus is on the flooring required in riser shafts and the area within the riser where the trades interconnect. Riser shafts are used to vertically route mechanical, electrical and plumbing (MEP) services to every level of a building.
The riser shaft starts its life as a series of holes in structural floors, one above the other. Walls and temporary fire doors are installed around the holes and filled with the necessary MEP services required for the building user’s needs.
Once the services are installed, they are closed off with permanent fire doors. As a riser shaft flooring specialist, we have several concerns about the current riser shaft design and construction practices during the building phase.
Before completion of the riser, it harbours significant destructive potential in the event of a fire. Several problematic, established practises must be addressed to prevent the risk of fires.
The uncertainty of design responsibility
Firstly, the current design of riser shaft flooring is a cause for concern. Principal designers (architects, structural engineers and MEP consultants) are not designing permanent riser flooring as they do not see it as their responsibility.
Rather, they see the risk of falling when working at height around these open holes as the main risk to be managed by the principal contractor.
The open shaft risk being delegated to the principal contractor during construction has unfortunately become the industry norm, despite being an inherently flawed approach as the design is not within the remit of principal contractors.
Principal contractors then pass the responsibility for working at height to the frame contractor because they are forming the riser openings in the floor structure as they build.
The established practise of combustible fall protection products
Subcontractors look for the cheapest fall protection product they can buy to remain comparative with their competition, which is typically a glass reinforced plastic (GRP) grating. GRP is flexible, cheap to buy, easy to install and allows for late changes in vertical MEP service coordination.
Throughout the construction industry it is widely believed that GRP is non-combustible due to it being labelled as fire resistant.
GRP was implemented as a temporary solution – but it became permanent
The established use of GRP demonstrates that there is no attention paid to the combustible properties of a product used in fall protection and a lack of understanding that product that is labelled fire resistant may be highly combustible in the wrong situation.
As mentioned previously, GRP was only originally implemented as a temporary solution. Unfortunately, the industry considers cost and safety in the same sentence and over time, the expedient measure has become permanent due to the low cost.
This hazardous practice has become so well established that many don’t even pay attention to the type of resin the GRP is made from, posing a significant threat to on-site health and safety as the most popular GRP resins (orthophthalic and isophthalic) are combustible.
A recent scaled fire test on various types of GRP in mock-up riser shafts, show GRP grating fuelling a fire to over 670 degrees in seven minutes. The GRP supplier test results indicate a pass for the surface spread of flame (BS: 476 part 7, now superseded by BS 13,501-1 in part).

Therefore, this should not be taken to demonstrate that these products are safe in a shaft fire situation. They are combustible ranging from Euroclass B to D.
The riser shaft during construction takes the form of an incomplete chimney or passage linked to every floor level of a high-rise building.
The hazardous state of a riser shaft fitted with combustible materials for fall protection (and then never removed) is an accident waiting to happen.
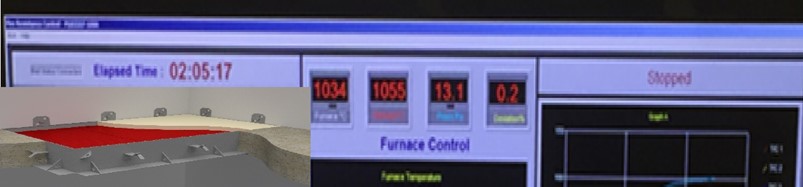
The ambiguity of regulations
Given the lethal risk of fire in the riser shafts, there are codes of practice, regulations and legislation in place to stop the spread of smoke and flame during construction of incomplete riser shafts.
However, these are often misunderstood or ignored by designers and site teams as they differ from the fundamental requirements for the building in use under Approved Document B.
The Joint Codes of Practice (JCoP) published by the fire protection association titled Fire protection on Construction Sites and buildings undergoing renovation has been issued as a 10th edition, Amendment 1, which bears a significant difference in messaging from the former 9th addition.
JCoP states the following: ‘consideration should be given to all potential fire hazards which may be identifiable at the design stage. These may be managed by considering: [A] the use of non-combustible and non-flammable materials to reduce the fire load.
Particular consideration should be given to reducing the risks presented by all combustible insulating materials, in particular those in cladding systems, green roofing/ walling (or similar alternative features) and structural insulated panels.
This should also include consideration of temporary materials brought onto site to facilitate work such as full protection products (non-combustible scaffold boards in place of timber boards in high fire risk areas).’
Therefore, the new messaging includes useful guidance on scaffold boards which should be non-combustible, given the risk of fire when working in the riser shaft.
However, reading this we are presented with the irony that workers will be using non-combustible scaffold boards to access work at height to fix combustible materials (GRP) in place within the riser shaft.
Rather than focusing on scaffold boards specifically, if the text instead referred to all non-combustible materials the ambiguity associated with the employment of combustible materials would be eradicated and buildings during construction will be safer as a result.
Gain better fire protection with the right riser flooring
Despite established practices, the fire safety guidance during construction is increasingly optimistic. JCoP 10th edition (amendment 1) now considers the impact of fire loading of temporary materials during the design phase, which is excellent progress. Furthermore, it now also stipulates the need for temporary horizontal (compartmentation) every fifth floor for 60 minutes without loss of integrity or insulation, which is reduced from every 10th floor.
There has also been a change of when this code comes into play where the original focus was on buildings over 30 metres; this has now been reduced to 18 metres above a fire appliance. This highlights the importance of managing the fire risk in a shaft to prevent the fire spread. Therefore, the industry is moving in a more positive direction with regards to fire safety. Greater industry education and contractors becoming more familiar with all aspects of regulation will greatly improve health and safety practises.
The lack of a ban on combustible materials within the riser shafts still remains, ensuring that the widespread use of GRP still poses a significant threat. In order to make positive changes to the industry must also shift from its current discipline centric mentality; the reason for the lack of design which gets passed down the supply chain.
We propose that principal designers should instead be designing a permanent rise of flooring, meeting their obligations under CDM 2015, page 8 section 5a avoid risk in design, stated under the general principles of prevention during the initial design phase and specifying riser flooring to Euroclass A1 non-combustible standard so that every precaution possible is been taken to ensure fire safety as well as fall protection.
For more information on RiserSafe® and to arrange a meeting with our industry experts, call 01707-324523 .