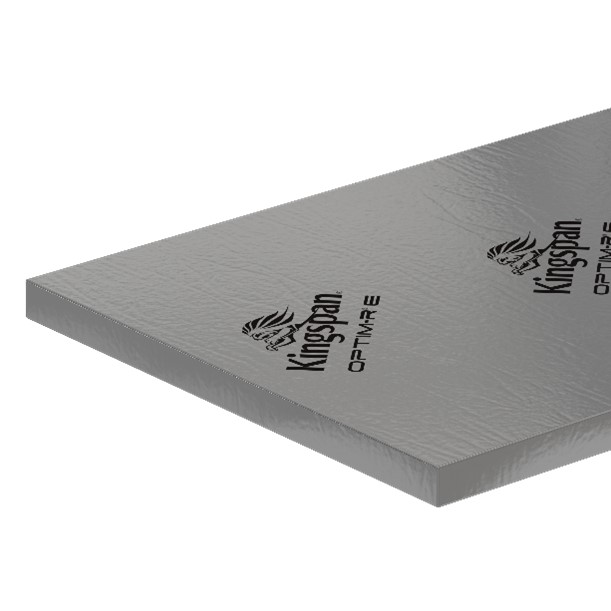
Kingspan explores how encapsulated vacuum insulation panels (VIPs) could be the answer to improving your inverted roof’s performance
Over the past year, the English, Scottish and Welsh Governments have all been introducing updates to the energy performance targets in their respective Building Regulations and Standards, leading to more developers and homeowners considering encapsulated vacuum insulation panels than ever before.
These can have a significant impact on insulation specification – particularly when it comes to roofing projects. In Scotland, for example, a target U-value of 0.09 W/m2K has been set within the Notional Building Specification for roofs on new domestic properties, as well as an area-weighted, worst-case value of 0.12 W/m²K for new build, extensions and refurbishments.
Achieving these ambitious levels of fabric performance can be challenging with traditional insulation materials, requiring increased thicknesses to be used and resulting in much thicker and heavier overall roof constructions. This issue is especially significant for inverted roofing applications, where the insulation layer sits above the waterproofing layer.
Historically, extruded polystyrene (XPS) insulation has been used for this application due to its excellent moisture resistance properties. However, these boards offer relatively low levels of thermal performance, meaning a significant thickness is needed to achieve a low U-value.
Encapsulated vacuum insulation panels (VIPs) offer a new solution that can significantly reduce the thickness of insulation required to achieve these values.
Retrofit potential and high thermal performance
Inverted roofs are expected to do a lot during their lifetime. They must be properly drained, fully waterproofed, and, increasingly, capable of supporting functional upper surfaces such as green roofs or roof terraces.
Fitting a significant thickness of insulation in these constructions can present additional challenges, particularly where the upstand height is already set, or where a smooth transition is needed between internal and external spaces. This is where VIPs can help.
VIPs are generally seen as a problem-solving solution, particularly for retrofits. In their basic form, they are made by evacuating the air out of a microporous core and sealing it in a thin, gas-tight membrane to ensure the vacuum is maintained over time.
These VIPs can achieve excellent thermal performance, making them well suited to retrofit applications above solid floors or flat roofs where you need to hit the desired U-value with a minimum thickness of insulation.
Encapsulated VIP systems are now available for inverted roof applications
These panels are covered in a protective spray coating to provide a more robust finish which is easy to handle and makes them suitable for inverted roof applications. Some encapsulated VIPs can achieve a declared thermal conductivity (lambda value) of 0.008 W/mK, and a design thermal conductivity of 0.009 W/mK.
The encapsulated VIPs are usually supplied with extruded polystyrene (XPS) insulation boards of the same thickness. These boards can be cut as infill strips to fit around the perimeter of the roof, fill awkward spaces between the VIPs and to enable penetrations through the insulation layer, allowing for elements such as rooflights or ventilator kerbs. Suppliers can provide a clear, project-specific layout for these systems, ensuring the best possible ratio of encapsulated VIPs to infill panels.
In practice
To illustrate how VIPs can be used to create a reduced construction depth over traditional insulation approaches, without compromising on thermal performance, we compared two build-ups above a typical concrete decked roof configuration on a property located in Glasgow.
The constructions differed only in insulation specification. One features XPS boards with a declared lambda value of 0.034 W/mK and a design value of 0.036 W/mK. The other features encapsulated VIPs, combined with a 120 mm layer of the same XPS insulation for additional protection. They have been calculated to achieve a U-value of 0.09 W/m2K as required by Section 6 of the Building Standards.
Construction | 150 mm concrete deck, liquid applied waterproofing, geotextile membrane, XPS, water flow reduction layer, paving slabs on support | 150 mm concrete deck, liquid applied waterproofing, geotextile membrane, encapsulated VIP system*, XPS, water flow reduction layer, paving slabs on support |
Insulation thickness required to meet the 0.09 W/m2K requirement | 420 mm (made up of two 150 mm layers and one 120 mm layer below) | 220 mm (made up of two 50 mm encapsulated VIP system layers with a 120 mm XPS overlay). |
Table 1: Inverted roof constructions and insulation thicknesses designed to achieve U-value of 0.09 W/m2K for a typical concrete roof in G1 postcode area, Glasgow.
*A thermal bridging factor of 15% has been applied where XPS infill insulation panels are used within the design. A full design will include a specific bridging factor based on the proportion of infill panels to encapsulated VIPs.
As the table clearly shows, installing encapsulated VIPs can help to significantly reduce the thickness of the insulation layer in an inverted roof application, and therefore provide the ideal solution where space is a key consideration.
It is important to note that the U-value of all inverted roofing systems is influenced by local rainfall. In addition, the layout of your roof and configuration of the encapsulated VIPs may affect the required thickness. For this reason, the encapsulated VIPs system should be designed specifically for your project.
Tailored solutions
Designing both new and existing buildings to achieve a good level of fabric performance will not only be key for compliance, but also for ensuring we remain on the path to creating a net zero carbon built environment.
Solutions such as encapsulated VIPs can help to address challenging applications without having to compromise on the thermal performance of the construction.
For further information and technical support, please contact:
Or call +44 (0) 1544 388 601