Denmark’s tallest tower, the Lighthouse Tower in Aarhus, used Imerso’s digital construction tools to reduce costs and project delays substantially
Denmark’s tallest tower stands at 142 metres, spearing into the skyline of Aarhus.
Construction of The Lighthouse Tower was anything but straightforward.
Having already completed the first phase of the project in 2012, the second phase was paused due to feasibility concerns regarding challenging ground conditions for such a heavy structure, alongside the looming menace of a financial downturn.
Eventully Danish construction company Per Aarsleff were awarded the contract to build the second phase, which included the main tower and two 10-storey buildings “Promenadehuset” and “Kanalhuset”.
Construction quality control was a key concern
Imerso combines innovative methods like laser scanning and BIM into a real-time digital twin for highly efficient construction site management.
Routine As Built surveys and proactive site monitoring helped ensure construction quality control throughout the project and ultimately avoid work errors and delay costs.
Prefabricated construction ensured swift project delivery
Spanning 22 x 22 meters, the “Crown” of Denmark’s tallest tower, consists of a heavy steel structure of over 70 tons, with a complex geometry resembling a seashell. The public can access a viewing platform and bar to see across Aarhus’ harbour and the city.
The steel elements of the structure were prefabricated and assembled on-site, then lifted up the tower in four parts once the top floors were completed.
Once on the roof, they were placed on two different floors and bolted onto approximately 250 rods.
The curved design of the roof, with bends featuring eleven different slopes, meant teams had to be especially precise in placing correctly within the tight tolerances. Even more so when you consider the restricted working space and unusual heights.
A lean construction process ensure that the team were adhering to project requirements every step of the way.
Automation of As Built inspections revealed critical deviations in Denmark’s tallest tower
VDC coordinator Christian Øster and his team were looking for the right construction software tool to closely monitor the As Built status.
The main focus was to implement an innovative workflow that emphasises quality control, so any deviations can be detected early and resolved proactively.
From other projects, The VDC team at Aarsleff had great results using Imerso for capturing the As Built conditions with Laser Scanning — enabling all As Built data to be automatically verified against the BIM specifications on a routine basis.
Using a Leica RTC 360 laser scanner, the team made an As Built survey to capture the roof area where the tower “Crown” would be installed.
Uploading the resulting As Built data to Imerso, Christian and his team ran the automatic inspection against the BIM models in minutes and found 14 deviations that had remained overlooked in that critical area alone.
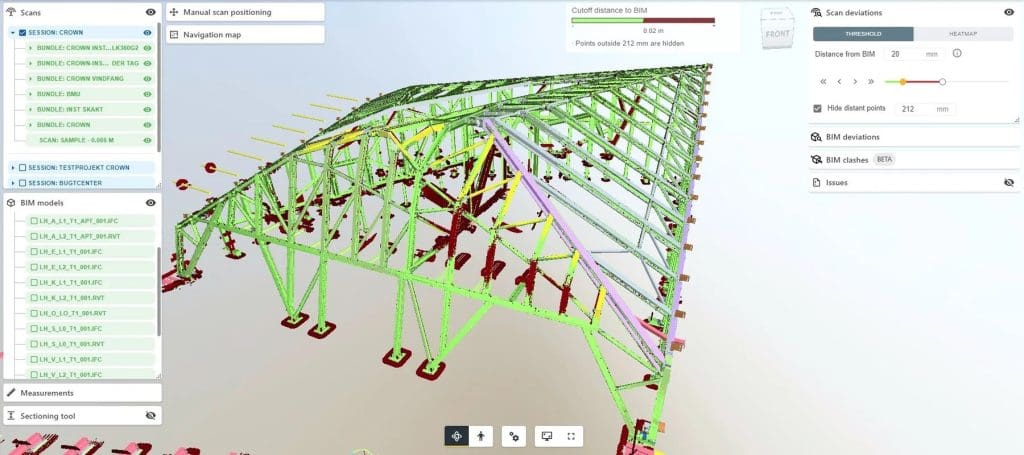
Aarsleff is utilising Imerso across a further eleven projects
Within eighteen months, Per Aarsleff has scaled up Imerso deployments across eleven projects with another two scheduled to start in 2023, aiming to streamline best practices of Lean Construction and emphasise work quality through automatic BIM workflows.
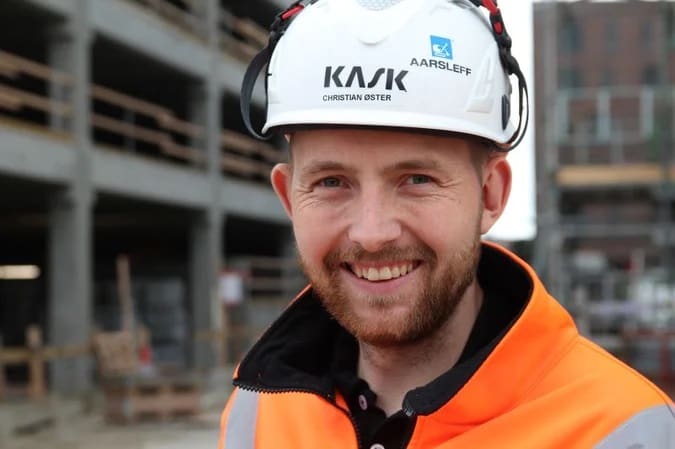
“While advanced, the construction world in Denmark is still pretty conservative. We only want things that have been tried and tested.
As a VDC professional, I know that the greatest praise one can get is when you see the most conservative people ask for more of it — This is what happened with Imerso.”