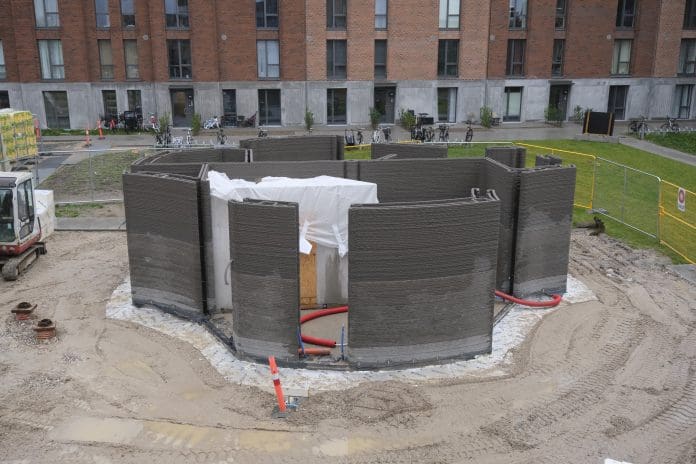
The debut of a 3D-printed, low CO2 concrete building in Copenhagen marks a transformative leap in construction methods
Partnering with 3DCP Group, AKF introduces a pioneering structure featuring environmentally friendly materials and an adaptive construction process.
Once complete, the low CO2 concrete building will house a gym, a guest room and a common laundry facility for residents.
Special low CO2 cement with 30% lower CO2 footprint was used in the concrete
To further reduce the CO2 footprint, the entire AKF project was printed using low CO2 cement, which has a carbon footprint of 30% lower than normal cement.
The low CO2 cement was mixed with local sand and gravel and turned into 3D printable concrete using the D.fab admixtures method developed by Cemex and COBOD.
Compared to 3D printing of mortars, the low CO2 cement 3D printable concrete reduces the CO2 footprint by 50%.
The low CO2 concrete building was printed using five printing days
AKF sees significant potential in 3D printing technology that goes beyond concrete and envisions a future where natural resources like clay-rich soil can be used for 3D-printed construction.
Vibeke Lorenzen, the technical director at AKF, said: “3D printing opens the door to a world of possibilities, and hopefully, we can contribute to pushing the industry’s traditional construction methods”.
Saga Architects, who also designed the first building 3DCP Group made in Denmark, strived to make the community building appear forthcoming and friendly by using a lot of wood for the decorative parts and organic shapes for the walls, a detail virtually impossible to make with conventional methods.