PBC Today was recently invited to the opening of the new regional headquarters for Bentley Systems at 8 Bishopsgate in London, where we caught up with construction manager LendLease and Bentley System’s Greg Demchak to discuss building design challenges and the use of Bentley’s infrastructure construction management software SYNCHRO
Situated at 8 Bishopsgate, the new 50-storey tower stands as a testament to innovation, offering an interactive collaborative space that fosters networking and stimulates discussions on the future of infrastructure delivery.
Bentley’s structural engineering software and SYNCHRO, their flagship 4D infrastructure construction management software and an integral part of Bentley Infrastructure Cloud, played a pivotal role in overcoming the challenges faced during the construction of 8 Bishopsgate.
Logistical and structural complexity at 8 Bishopsgate
Can you elaborate on the engineering challenges faced during the construction of 8 Bishopsgate, particularly those related to its design and location in the heart of London’s skyline?
LendLease: “8 Bishopsgate presented a number of challenges during its construction, including logistical constraints and structural complexity. The building design required the construction method to facilitate the safe construction of three overhangs spanning up to 6 meters over the public walkway.
“The superstructure was formed through an innovative steel-braced box that tied the two cores together, introducing constraints on their progression during the structure’s temporary state.
“The site’s constrained nature, coupled with the building’s unique geometry, posed significant logistical challenges. All materials had to be delivered via a pit lane on Bishopsgate and safely offloaded above the live footpath, adding to the project’s complexity.
“These complexities were incorporated into the construction approach with the use of SYNCHRO, enabling the pre-planning of the construction activities to ensure the successful delivery of the project.”
Bentley: “The use of SYNCHRO was a way to schedule, plan, organise, and figure out how all the deliveries were going to come. It also helped the team determine how they were going to get all the components up and erect the building in such a very tight job site.”
A continuous legacy of innovation: Solutions for logistical and structural challenges
What innovative approaches were implemented to ensure successful completion within the specified timeframe?
A range of innovations were developed to suit the project requirements, including:
- Prefabrication items that reduced installation periods and on-site labour requirements, such as:
– Multi-level mechanical risers.
– Electrical risers.
– WC pods. - Concrete core rigs with integrated lifting equipment for stair construction that reduced cranage requirements.
- Bespoke prefabricated reinforcement lifting stillages that reduced risk and increased productivity.
- A mammoth hoist to allow facade panels to be loaded out without cranage.
- Gantry cranes that enabled material offloading via a logistics gantry to reduce vehicle and pedestrian interfaces.
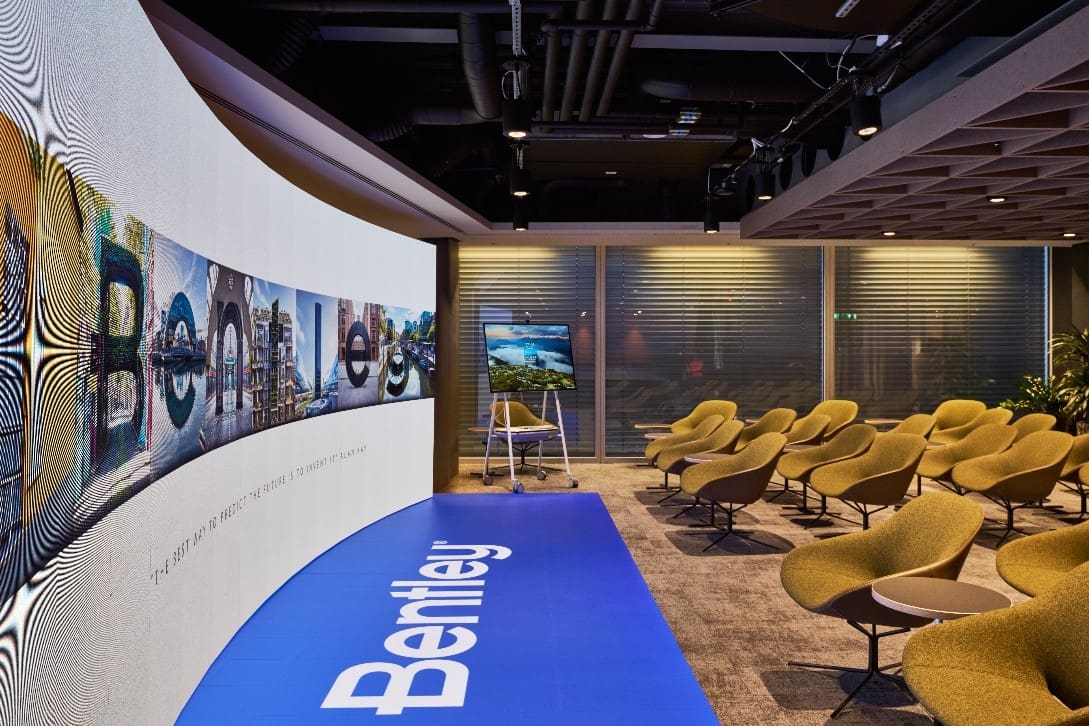
Bentley: “SYNCHRO was used for detailed planning, from the early high-level concept to the animation planning of equipment being dropped off, delivered, lifted, and installed in the building.
“By doing this digital rehearsal ahead of time, Leandlease planned the construction of the building beforehand.”
Infrastructure construction management software solution
How did the integration of infrastructure technology contribute to overcoming the challenges encountered during the construction process, including those exacerbated by unforeseen events such as the COVID-19 pandemic?
LendLease: “The use of SYNCHRO enabled the project team to build the project virtually before undertaking on-site works.
“The application enabled the refinement of construction methods that increased productivity and reduced safety risks by allowing detailed and thorough assessments of the installation sequences to be developed and considered by the team.
“The early development of the 4D construction sequence enabled detailed discussions to continue to be undertaken virtually during COVID, when project team members were working remotely, enabling continued engagement from all project stakeholders during this challenging period.”
Bentley: “During the pandemic, there were construction pauses, and if teams were working remotely, they could still understand and share information visually using SYNCHRO.
“Even if you were in very different locations, you could be doing 4D planning and modelling and basically building the tower virtually, even though you couldn’t physically build the tower.”
Environmental consciousness in project delivery
How does the architectural design of the building align with corporate sustainability targets?
LendLease: “The design for 8 Bishopsgate incorporates a range of sustainable initiatives developed by the design team in collaboration with the construction team.
“The optimisation of the steel structure reduced the embodied carbon on the project by 5,000 tonnes, and the innovative piled foundation solution delivered a further 500 tonnes of embodied carbon savings.
“The intelligent Combined Cavity Facade system has enabled the cooling load for the building to be reduced by 1.2 megawatts.
“Furthermore, in delivery, the project took an approach that sought to reduce unnecessary packaging and avoid single-use plastics where possible to minimise its impact on the environment.”
Bentley: “We’re committed to sustainability as a company and broadly support these measures in the industry. At the government level, we participated in COP28 and COP29.
“It’s important for us to move our office from an old building to a new one that has been listed as the most sustainable new speculative building in the city. I think this project speaks to our commitment to reducing environmental impact. We looked at a lot of different projects in the city, and we thought this one aligned well with our own vision.”