Marmox Thermoblocks is an affordable solution for preventing heat loss and addressing thermal bridging in various building projects
Anyone with a passing interest in celebrity lifestyles will know that buying an island in the Maldives is a popular way to secure privacy.
However, even in the humbler world of construction, the cost of achieving isolation can be eye-wateringly expensive.
The best solutions require very special materials and the use of technically challenging engineering practices.
These materials often have to be combined to cope with the multiple demands placed on building structures.
For instance, the aerospace industry and even top car manufacturers use gold as an insulant because its excellent reflectance repels radiant heat.
By contrast, building contractors’ budgets will always require them to settle for multifoil insulation or some other affordable alternative.
Even though we have managed to replicate the emptiness of space to keep coffee hot in a flask, ‘vacuum’ sealed glazing units – despite their undoubted performance premium compared to argon-filled cavities – feature in only the most expensive fenestration systems.
Affordable building products to achieve isolation
Thankfully, there are some tried and trusted building products that are affordable and practical and are answering the need to prevent heat from escaping from our properties.
For example, Marmox Thermoblocks are finding applications on an increasing number of projects, from social housing schemes to PassivHaus-standard schools and even swimming pool complexes.
Thermoblocks are the answer to tackling linear heat loss
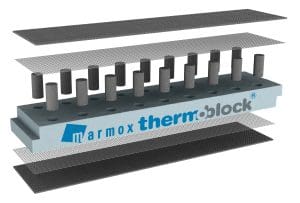
Unique to the industry in terms of their insulation performance, coupled with high load-carrying capacity and practicality in use, Thermoblocks are viewed by many specifiers as offering the ideal answer to tackling linear heat loss at places such as the ground floor perimeter, parapet walls, and even within basement construction.
BBA-approved Thermoblocks are available in widths of 100, 140, or 215mm and are formed from sections of XPS encapsulating two rows of high-strength, epoxy concrete mini-columns.
These are attached at either end to the top and bottom layers of glass-fibre reinforced polymer concrete, to ensure a good bond with the rest of the structure.
The 600mm long units – the same depth as a course of bricks – feature an overlapping, stepped joint that is normally secured using Marmox’s own 360 adhesive. They can also be cut to length to suit individual plot dimensions.
The installation task is normally assigned to the groundworker or bricklaying subcontractor.
With the XPS also being fully waterproof, Thermoblocks can further be seen as representing a modern advancement on the traditional practice of laying engineering bricks to form a damp-proof course.
Most wall constructions will incorporate a conventional DPC interconnecting with cavity trays and damp-proof membranes protecting the main floor area.
Increasing use in modern build solutions
Significantly, however, as well as for masonry wall designs, Thermoblocks are increasingly being utilised beneath timber frames, SIPs, and other modern offsite or system-build solutions.
This has included one of the UK’s largest developers of affordable housing incorporating them into the extensive oversites used as the base for their low- and medium-rise apartment buildings, where modules weighing several tonnes are craned into position directly on top of the courses of Thermoblocks without disturbing them.
Grant Terry, the Marketing Manager for Marmox, commented: “The increasing focus on energy performance, from fuel prices and legislation like the Future Homes standard, have forced specifiers to pay particular attention to thermal bridging, and Thermoblock really offers a unique solution.
“The product has proved itself in a range of applications and is now widely used in commercial contracts as well as by housebuilders.
“15% of a building’s heat gets lost through the wall-floor junction, and by simply replacing one layer of blocks with Marmox Thermoblocks, that heat loss can be cut to just 1%, and crucially, it avoids having to use punishing default values under SAP, and it is also now being used beneath modular multi-story buildings.”
Marmox offers comprehensive technical advice on project-specific matters
Marmox, based in Chatham, Kent, is able to offer developers comprehensive technical advice on project-specific and other matters, as well as provide on-site training for contractors employing the product for the first time.
The team also regularly assists architects and structural engineers seeking guidance or the provision of detailed drawings so that Thermoblocks can be incorporated into non-conventional wall types and still fully contribute to meeting SAP or even Passivhaus requirements.
Thermoblocks are an effective solution to thermal bridging
In fact, on recent projects across the UK, Thermoblocks have been used within wall constructions where the outer leaf is raised in natural coursed stone, as well as beneath internal walls where thermal bridging is identified as an issue.
On one Passivhaus standard build in Wigan, 140mm wide Thermoblocks were laid along the base of the external walls, and the 100mm option was switched to for the party walls and all the internal ones.
So, with the Marmox products featured in the best-performing affordable housing projects across the country, we can confirm that the solution to thermal bridging isn’t rocket science.