Traditional building methods will not deliver the homes needed to tackle the housing crisis. It’s time to embrace the age of modular construction, says Kieran White, director of Vision Modular Systems
Modular construction is one of those things, like the personal computer or the mobile phone before it, that was lauded long before it came of age. We hear about their benefits, the disruptive forces that they will unleash upon our world and marvel while carrying on as if nothing has changed. And then, as if overnight, the technology arrives.
Indeed, much has been made of modular construction over the last few years, culminating in a commitment in the Housing White Paper to “promote more modular and factory-built homes”. Communities secretary Sajid Javid, who visited our factory last September, is clearly a supporter of the technology, arguing that modular provides modern, stylish homes that are “made to measure and ready to go”. He is wholly correct in this assertion: modular homes are high spec, built to last and capable of creating homes for the 21st century.
The modular home has a critical role to play in solving our chronic lack of housing. The existing construction sector, as currently formulated, simply cannot build the numbers of houses needed to get a proper roof over Britons’ heads.
Our work on Apex House, a 679-module student accommodation scheme in Wembley, is testimony to both the strength and potential of modular construction in the UK. Towering up at 28 storeys, and built in just 12 months, it stands as an excellent example of how manufacturing disciplines can be successfully applied to the housing market – a market besieged by chronic undersupply and ever-tightening margins for construction companies.
I use that word ‘manufacture’ when talking about our system for good reason. The way these homes are built is fundamentally different to the traditional brick-and-mortar approach that is usually taken. We can precision build these modules using assembly line techniques in a controlled factory environment.
This allows us to cut down on waste, both in our Bedford factory and onsite, as well as ensuring a consistent rate of quality for the modules. A modular construction approach to housing delivery creates homes that will stand the test of time, are better performing (as built performance meets design performance) and, I believe, provides homes superior to what we might be able to achieve by building onsite.
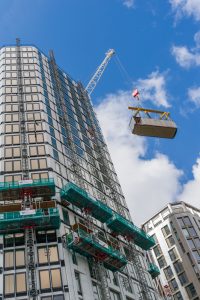
The assembly process itself also has several significant advantages over the traditional site-based approaches that have been employed for years.
Modular construction saves time – a crucial commodity amid a housing crisis. While traditional builders must prepare the site, install foundations and then construct the building, we can do both at the same time. While site-based work such as piling and pouring of foundations is underway, we have specialist manufacturer operations putting together the rest of the building at the same time. When the site is ready, we then transport the units from our factory to the site and slot the constituent parts together. A well-managed modular project can reduce overall build time by half, but equally provides for greater programme certainty, allowing developers to better plan for scarce resources.
Offsite construction offers two more substantial benefits: reduced environment disruption and greater certainty around financial planning. Both effects make the process of developing a site not only faster, but easier.
One of the many issues with getting planning permission involves the disruption that neighbours and local communities suffer. Beyond the obvious impact of the noise of construction and increased air pollution, an influx of heavy vehicles can clog up vital road access and slow down traffic. With modular, the number of transport movements is greatly reduced and the period over which they occur is also reduced. Most of the work can be done with a simple HGV to deliver the units and a crane to drop them into place.
In addition to the increased programme certainty offered by modular, a related benefit is cost certainty, which derives from the fact that up to 50% of the project cost is delivered through modular. Modular is predicated on manufacturing disciplines to ensure efficient operation of production lines, in a controlled factory environment. Going over budget is a common problem for traditional builds, whether due to delays in the design, sourcing of materials or subcontractor difficulties – all of which feeds into the uncertainty of bricks and mortar construction. In adopting modular, design and detailing is driven much earlier in the project lifecycle to allow for the procurement of materials required to feed the production lines – much like any other form of manufacturing.
The materials are ordered and the delivery scheduled in detail – providing consistent demand for many SME suppliers – and, given the precision-built approach, there is very little wastage of materials, which helps to contain costs and make the whole development more environmentally friendly, while ensuring high-quality build performance.
All of this demonstrates that modular construction is now a competitive alternative to traditional build methods. Factory-built homes offer distinct advantages over traditional construction, as Apex House proves. The government has woken up to this fact, and the market is starting to, as we now enter the modular age.
Kieran White
Director
Vision Modular Systems
Tel: +44 (0)1234 845 640
info@visionmodularsystems.com
www.visionmodular.com
www.twitter.com/visionmodular