In the third of a series of articles, Mike Shilton and Carl Collins address collaboration at the construction and operations stages of a BIM project
This is the third in a series of articles (Concept design to construction: why collaboration is key and How BIM collaboration in the early design stages should be addressed) that considers how BIM Level 2 and digital processes can support project work stages. In this final article, we will review how BIM can help with the construction of the project and on-going operations and maintenance of a project following handover.
After the client has awarded the contract and before the contractor begins work, there is a process referred to as “mobilisation”, where there are a wide number of activities to prepare for Stage 5 – Construction. This is often contractor led and can include preparation of a master programme, method statements, site layout plans and principles for construction, preparing statutory authorities and utilities and notifying the HSE. During this time, the client may need to prepare for occupation and the BIM model will continue to inform the construction process and phasing.
The contractor should use the information shared by the design teams as the basis for the models, plans, documents and schedules, as this refinement process will usually be quicker and more efficient than redrafting from scratch. The processes that we discussed in the previous articles are now bearing fruit, this standardisation of approach allows contractors, sub-contractors and suppliers to work seamlessly with the models supplied.
Construction phase
During the Construction phase, the BIM model can be used as a coordination tool and in an increasing number of cases automate the construction process, such as where earth moving vehicles are autonomously “driven” from the software to achieve the required levels. The model can also be used to deliver updates from the project team to the contractor, such as refinements to the site levels for site drainage and plant species substitutions. The model will be updated to include these changes. Working with the facilities managers, the handover strategy will be developed to ensure the seamless transition from construction to the operations phase, as set out in the soft landings strategy. See the Government Soft Landings document for more information. As with previous stages, the BIM Execution plan will be updated to consider specialist contractors or suppliers engaged during installation.
We can also start to think about what other uses we can put the models to. BIM Level 2 is not an end in itself; it is there to facilitate now and leverage exciting and innovative ways of working in the future. For example, can we use our 3D model to automate the setting out of complex, hard landscaping? Can we use augmented reality to show our client what the site will look like when we have completed the works or show the proposed below ground services on a site before we start excavating? We can quickly swap out plants to not only show what effect this will have on the overall look and feel of the design but to compare the maintenance and cost implications over its lifetime. For example, do we go for a fast growing tree for quicker impact but with greater maintenance implications and a shorter lifespan or a tree that takes longer to establish but will have fewer maintenance costs and live for several hundred years? Substitution of plants that is reflected with specifications and schedules is already available within current software but growth and lifetime costs are still in its infancy. Critical to this is ensuring good data is being supplied throughout the design, construction and operations of the facility. The use and adoption of the Flora Product Data Template (PDT) developed by the Landscape Institute will assist with this, allowing us to understand far more what it will look like.
By the end of this Construction stage, the “as constructed” BIM model will be prepared to incorporate project changes and, where appropriate, warranty information will be compiled. This will be refined during the handover and close out stages (Stage 6) of the project, and the BIM model will be developed to reflect these changes and is now referred to as the Asset Information Model (AIM).
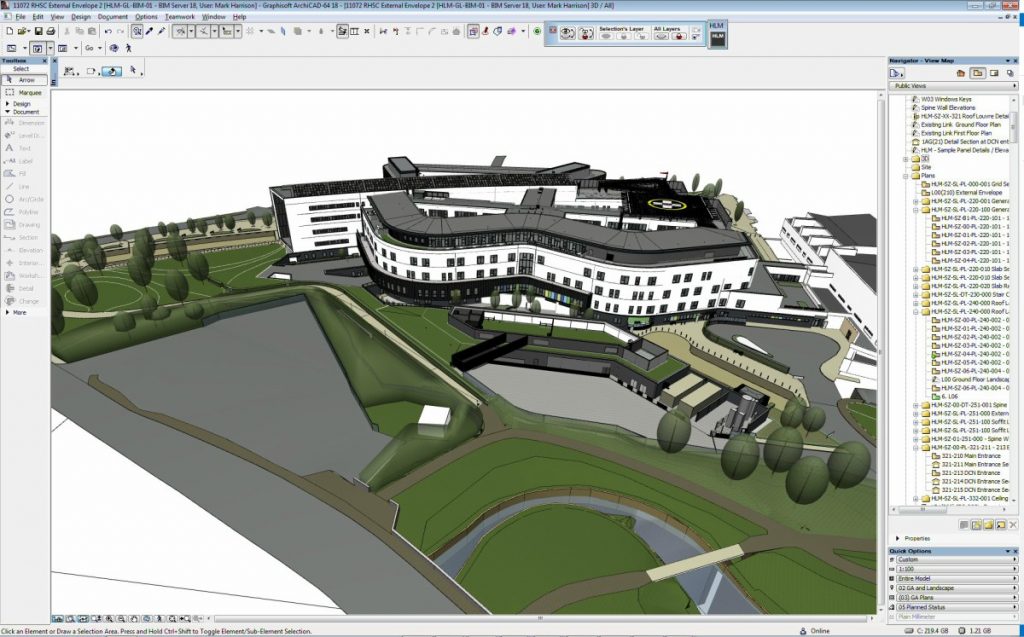
Royal Hospital for Sick Children and Department of Clinical Neurosciences, Edinburgh (UK). Courtesy of: HLM
In the handover between construction and operations, it is important to incorporate the information gathered by commissioning the installed equipment. For example, what water flows are required for a water feature and what treatment and cleaning are required to ensure its successful use? All this information will be vital for facility managers to keep the asset running at its very best and as intended.
Following client approval, the project moves into the final Operations phase, Stage 7. From this point, the AIM and supporting information will help the client and facilities managers manage their asset. This will provide the ability to identify and schedule maintenance, consider modifications to the model, such as minor works, and assess “what if” scenarios, such as the implications of changes to the maintenance of landscape areas, replacement of pumps and filters for water features and replacement of street furniture.
Operations phase
During the Operations phase of a project, the drivers for action change from the linear, sequential flow of the Design and Construction stages into an event driven state. For example, maintenance tasks can be scheduled, but they may also be reactive, driven by an event or failure within the constructed asset. To understand this change of process and to formalise it, we now move from the PAS 1192-2 process to PAS 1192-3, which covers how these reactive processes should be handled.
PAS 1192-3 takes on the concepts of ISO 55000, which is an international standard dealing with asset management. We now take the concepts of good asset management and apply a digital process, taking on the data generated during the Design and Construction phases in an ordered and structured way, into our facility management arena. This may be a Computer Aided Facility Management (CAFM) platform, but for smaller assets, which are common in landscape architecture, this may be too elaborate, and the information may reside in a facilities management database, or be moved into a GIS-based system.
Many landscape projects have yet to see the full benefits of BIM, particularly in the Operations stage, as too few BIM projects have reached this level of completion. However, we see the Operations stage as the major benefit of BIM, especially for landscape, because this is when good decisions made during the design and construction stage will have the greatest impact. Indeed, if you consider any landscape, the cost of maintaining the facility over its lifetime will far outweigh the cost of implementation. And it has been suggested by a BRE survey that more time spent during the design phase can save costs by twenty times during construction and up to sixty times in the operations phase of a project. This is because we can predict and iron out problems in the virtual world before we build them in the real world.
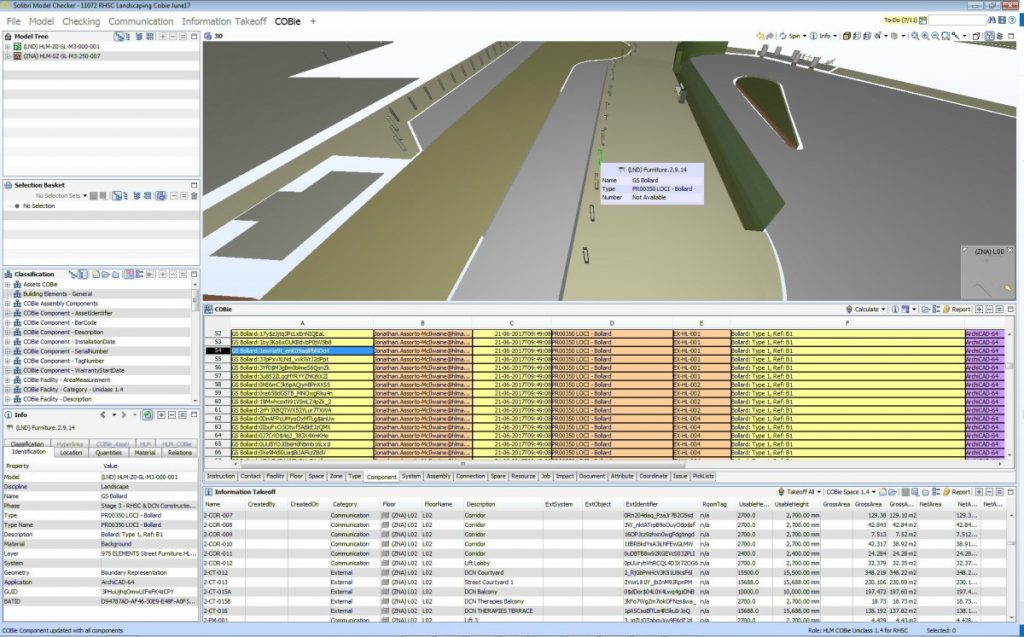
Royal Hospital for Sick Children and Department of Clinical Neurosciences, Edinburgh (UK). Courtesy of: HLM
Over the three articles, we have considered how BIM can help in collaboration and delivery of the project work stages. In essence, BIM is forcing the construction industry to introduce best practices through standards and improved workflows but, importantly, to follow other industries, such as manufacturing, aerospace, product design, where virtually modelling, testing and prototyping are standard practice.
BIM allows us to use virtual models to test our facility is fit for purpose before we start the construction or alteration because once we have started the works, design changes add to costs and lead to project delays. These are the key drivers for the government mandating BIM and why it is becoming ubiquitous within the construction industry. ■
. . . . . . . . . . . . . . . . . . . . . . . . . . . . . . . . . . . . . . . . . . . . . . .
Mike Shilton, CMLI
Product Director Keysoft Solutions
Chair – Landscape Institute Digital Practice Group
Carl Collins
Digital Engineering Consultant and Affiliate member
Landscape Institute
Tel: 0207 685 2640
Twitter @talklandscape