Matthew Durdin, director at Johnson Controls UK&I explores applications for digital twins in the built environment, how they can be implemented, and how building systems can be dramatically improved with a digital twin
A digital twin is a connected, virtual replica of something physical – be it an asset, product, or system. The technology helps create an interface that bridges the digital and physical worlds, for example in construction and building management. Digital twins enable architects, constructors and building managers to “predict the future” of their building – and to answer difficult questions that might otherwise hinder construction projects or reduce the lifetime of a building.
Where building information modelling (BIM) generates and manages digital reproductions, twins hold BIM data alongside building automation systems and sensor networks to bring a whole building together in one place. This creates a constantly evolving, collaborative version of the physical twin.
In modelling building systems, the twin uses myriad data points to bring all its knowledge together under one digital roof: from construction data and floor plans, to data from real-time sensors in a building management system (BMS), to all the data coming out of lighting, HVAC, fire, and security systems. Brought together, a digital twin can know everything about the assets of a building and its occupants – and can predict its every move.
Building a twin
In an ideal world, the digital twin is “born” before its physical counterpart, long before construction begins. Throughout the planning stages, an architect can remodel and update the building plans, and the twin can update and recompute itself. In this process, it can evaluate the building’s physical characteristics – such as modelling airflow or energy use – as well as its role in the wider environment, such as the building’s impact on traffic in the local area. A digital twin can go through thousands of changes before it is finalised and used to construct its physical twin.
If a digital twin is created for an existing building, it can only represent an approximation of the physical twin. However, the two become more alike every day as it collects more data from the building and its real-time sensors. Either way, having a digital twin ensures better decision-making and enables real-time visibility of a building and all its moving parts.
The impact of digital twins
So what exactly can a twin do that a well-planned construction project couldn’t? Before and during construction, a digital twin can improve system interactions and integrations, help select the right providers for the job, make data-driven cost and maintenance predictions, and even spot and assess installation obstacles and major construction risks. While construction professionals have long made these assessments themselves, the ability to do so while working full-time on the construction itself leads to a more cost- and time-efficient project.
Once built, a digital twin can make predictions that help to extend the lifetime of the building. This can include predicting security risks, parts replacement schedules, inefficiencies across all the different inter-operating systems, and even the impact of process integration as a building matures. This helps building owners and managers to know when action needs to be taken on their building, again streamlining costs and creating the best possible environment for its occupants.
Moreover, a twin brings together all the data necessary for predictive algorithms and artificial intelligence (AI) systems, from equipment fault predictions to building optimisation. Running simulations on a twin also reduces risk, helping system engineers make better business cases for system changes. By experimenting on a digital twin, equipment downtime can be reduced, just one way in which digital twins drive cost-efficiency. Cost reduction is a major application of twins: by helping predict and avoid unexpected costs, they help buildings operate more efficiently and avoid unexpected costs, by identifying system inefficiencies, and better estimating when new parts and upgrades are needed.
Alongside these applications, twins also streamline and improve the day to day operations of a building. A digital twin gives building managers a real-time view of a building’s integrated systems: from top-line dashboards for building health to specific applications like asset and people tracking, hot desking, parking, and condition-based building operations. There is also an impact on security: the real-time view offered by a digital twin takes historic trend data into account, which is then able to highlight unusual or abnormal actions that might predict security issues and help managers take action more quickly and accurately.
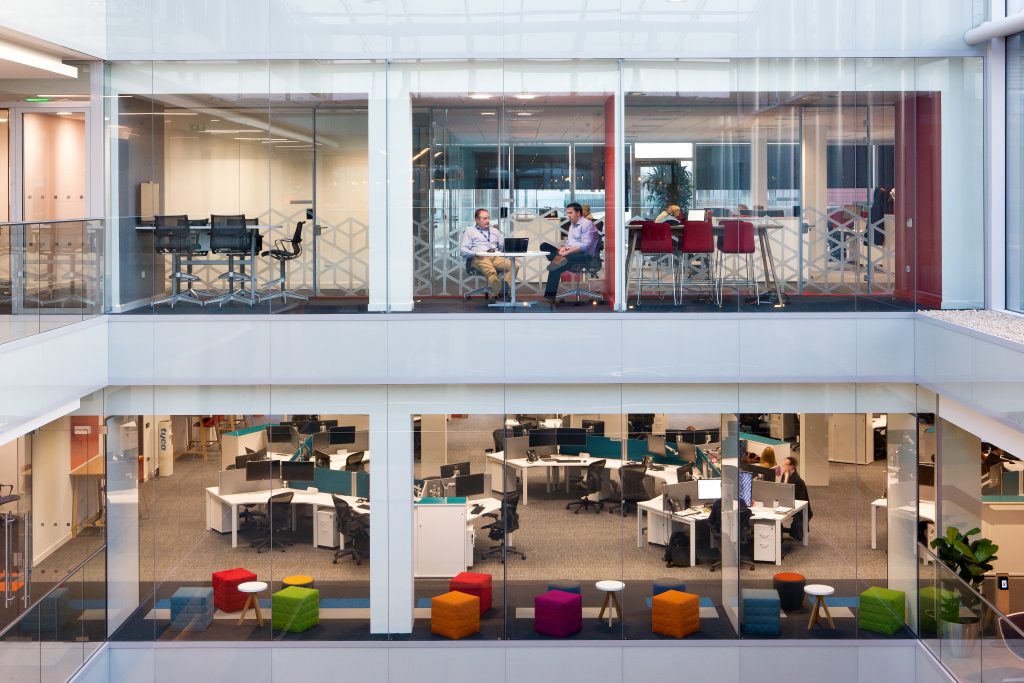
The challenge of data collection
While the data collected for digital twins can come from a variety of sources, a true digital twin must be a ‘system of systems’ integration. This includes the use of embedded sensors, wireless sensor networks, digitised building lifecycle data and systems, and integration with other cloud services and data providers. Wireless sensor networks, for example, collect data on temperature, lighting, occupancy, humidity, and many other factors from sensors installed throughout a building. These systems can easily be expanded or altered as needs change, making them a flexible investment for the future.
Other opportunities to channel data into a digital twin include data from BIM systems, smart HVAC systems, digitised pneumatic thermostats, smart plugs and smart elevator controls – but this is often only possible in modern, “smart” buildings, rather than older buildings.
The concerns around digital twins
As with every new technology, there are some concerns in the industry around the use of digital twins. Data standards have long been seen as something lacking in this area, meaning companies aren’t making smart technology investments. However, the Brick schema consortium is now working to standardise a unified approach to building representation to tackle this problem.
Cybersecurity is another key issue, as cyber “intruders” could potentially use a digital twin to gain access to confidential information about a building, though cybersecurity measures are generally built into a twin to avoid this. There is also the problem of tech ‘overkill’ – or a twin for twin’s sake – but creating a partnership with the tech provider who is right for your project will ensure that twins help, not hinder. Finally, BIM often came under scrutiny for systems not being kept up to date – and while a twin will also need to be kept up to date, it’s possible to build the digital twin with the capability to self-update, eradicating this problem.
Implementing a digital twin to innovate
If implemented correctly, twin technologies can have a major impact on building management and operations. Across the entire value chain, a digital twin enables the movement of a project from ideation, to visualisation of processes, to service and management at an ever-growing scale. Done right, digital twins enable decision support across a whole construction project or living building, as well as real-time visibility of products, assets, facilities and manufacturing.
The many applications from the planning stage to when the building is up and running – from the ability to predict maintenance and security risks to cost efficiency and better operational oversight – mean that digital twin technology is a must. Put simply, a modern smart building cannot be truly smart without a digital twin.
Matthew Durdin
Director
Twitter: @johnsoncontrols
LinkedIn: Johnson Controls
Great article Matthew that clearly describes the potential benefits and risks of a digital twin based on BIM. For some building types though, I think this concept has even more to offer. For example, in a data centre heat load and distribution vary significantly and poor configuration choices can result in significant losses in capacity (stranded capacity), not to mention increased risk and higher energy consumption. The use of the digital twin to understand the impact of choices can help the operator make the most of capacity, improve lifetime while providing training data for scenarios yet unseen which intelligent controls can use before live data supplements behavioural information. To my knowledge, these science based models (CFD for cooling in data centres) aren’t currently well integrated into BIM so the owner operator may need to think outside the box to get the most out of the digital twin.