Technology looks set to revolutionise construction, streamlining processes and improving quality, but is it ultimately a threat or opportunity for construction workers? Dominic Fahy, head of architecture, engineering, construction and manufacturing at Canon UK, takes a look
Industry 4.0 is set to fuel an £88.9bn increase in economic output for the construction sector by 2030, yet fears are rife that technological progression could displace humans in the workplace.
Enthusiasts see digital transformation – and its core pillars of data, analytics, automation and machine interaction – as a chance to drive a step-change and recapture the UK’s industrial strength. But with innovations such as robotics, artificial intelligence (AI) and the Internet of Things (IoT) poised to turbo-charge productivity, efficiency and speed, there is also concern tech advances could put 23.7% of construction roles at risk.
So, will the rise of the machines bring disaster for construction workers or a new beginning?
Building a better industry future
In short, humans won’t be phased out by digitalisation. Far from reducing prospects for existing employees, Industry 4.0 will bring evolution and opportunity. Increased automation of routine, repetitive and labour-intensive tasks will change the way jobs are carried out – enabling individuals to work faster, better and more productively.
Take for instance, Building Information Modelling (BIM). By creating shared insights for specific projects, BIM is already driving easier cross-team collaboration. Looking ahead, this smart tool could limit mistakes too, allowing designers to compare incoming data about on-site conditions and address discrepancies before they become costly errors.
To an extent, machines may take on some manual positions in areas such as assembly and production, but greater reliance on tech will stimulate demand for new abilities. In fact, the Word Economic Forum (WEF) predicts 133m jobs could be created globally by 2025, resulting in the need for more diverse skills.
The onus will, therefore, be on businesses to equip their workforces with the competencies and knowledge needed to manage digital disruption if they want talent to remain, and prosper.
Education: The foundation of success
Tomorrow’s construction sector is likely to necessitate an extensive array of roles, including virtual reality experts, robotics engineers, modular designers, data analysts and planners for prefabrication factories. For organisations, this means it’s vital to not only attract new talent but also to provide comprehensive training that will help current employees enhance their capabilities and master the skills that emerging positions require.
At the centre of development programmes should be tailored learning and support. After all, there is potential for those heavily impacted by automation – the employees who must work with new technologies – to feel demotivated or resistant to change if they don’t understand its benefits, or how to adapt.
Therefore, firms need to ensure educational initiatives offer continuous support, flexible practical and theoretical training, and specific direction about using advanced tools on a day-to-day basis. For instance, this might entail a blend of instructional sessions and augmented reality (AR) experiences where employees can safely test their skills in virtual workspaces and build confidence.
When implementing transformation at scale, it’s important not to overlook the value of strong leadership. To keep progress on track, every firm – no matter what sector – should consider creating a digital leadership council to enable integration of new products, services and abilities to run smoothly through shared commitment.
One final note: Don’t rush in
Current advice states adaptation is essential for construction to survive. As noted by Michael Burke, co-chair of the WEF Infrastructure & Urban Development community, today’s business models, strategies and capabilities “will not be sufficient” in any future world, which makes urgent preparation crucial. But how exactly they should prepare is less clear.
There is no standard formula for moving into a new industrial age; the right path for each company depends on its unique priorities, specialism and challenges. As a result, a considered and measured approach will be key. Before adopting the latest intelligent tech and adjusting roles, businesses should assess existing strengths and weaknesses. In particular, it will be vital to establish whether reconfiguring procedures or extending services will provide tangible, lasting gains or not – a goal most effectively achieved by testing innovations as they arise and making useful adjustments permanent.
Whichever route firms take, their core focus must be on securing the best long-term future for their people and business. New technologies have the ability to streamline processes and assist construction workers with autonomous tasks, resulting in overall enhanced efficiency and productivity. However, success is only assured if organisations invest time in training employees and creating a talent framework that leads to new beginnings, not a digital disaster.
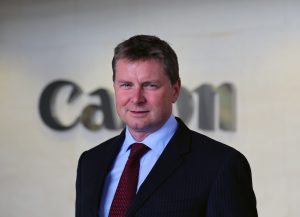
Dominic Fahy
Head of Architecture, Engineering,
Construction & Manufacturing
Tel: +44 (0)208 5888 000
Twitter: CanonUKandIE
Facebook: CanonUKLtd