Kingspan Insulation has published a new white paper with research from Currie & Brown exploring how different insulation specifications impact overall project costs
With the government committing the UK to achieving net zero greenhouse emissions by the middle of the century, the race is on to tackle our built environment. Estimates suggest that the heating demand for buildings and industry accounts for almost a third of the UK’s total greenhouse emissions. One obvious way to address this demand is by improving the insulation performance of building envelopes. These materials require little or no maintenance and, when installed with care and attention, can effectively minimise energy demand for decades.
As with all aspects of a construction, the upfront cost of materials is a clear consideration in the specification process. As you might expect, the drawback with cheaper insulation materials is that they are less thermally efficient. This means that greater thicknesses are required to achieve a desired U-value and this change can have significant implications for other aspects of the build.
Research from leading consultant Currie & Brown has now suggested that by specifying more thermally efficient materials in cavity wall applications it is possible to reduce overall project costs while achieving slimmer construction thicknesses.
Insulation options
Regulatory guidance on the level of thermal insulation required for new homes is covered within Approved Documents L1A to the Building Regulations 2013 (in England), 2014 (in Wales) and Section 6 (Energy) 2015 of the Building Standards in Scotland. To ensure compliance, it is a good idea to target an external wall U-value of 0.16 W/m²·K for properties in England and Wales and 0.15 W/m²·K in Scotland.
A key measure of an insulation material’s performance is its thermal conductivity (lambda). Products with a lower thermal conductivity are more resistant to heat loss through conduction, meaning a reduced thickness of insulation can be used to achieve a desired level of thermal performance.
Cheaper materials often have relatively high thermal conductivities. For example, mineral fibre insulation typically achieves values of between 0.032-0.037 W/m·K. In contrast, the latest phenolic insulation boards have a thermal conductivity of just 0.018 W/m·K.
As such, while these boards are more expensive than lower performing materials, they can enable target U-values to be reached using thinner insulation, reducing external wall construction depths.
To understand how this may impact overall project costs, Kingspan Insulation commissioned Currie & Brown to carry out an analysis.
Cost analysis
To assess how the choice of insulation could impact overall project costs, Currie & Brown developed scenarios for properties of three different scales:
- Large detached house.
- Small detached house.
- Mid-terraced house.
Each property was modelled using SAP 2012 and was designed to meet the requirements of Approved Document L1A to the Building Regulations 2013 (England). Two external wall constructions with a U-value of 0.16 W/m2.K were modelled for each scenario, one with mineral fibre insulation and the other with premium performance phenolic insulation. The full specifications are shown in Table 1.
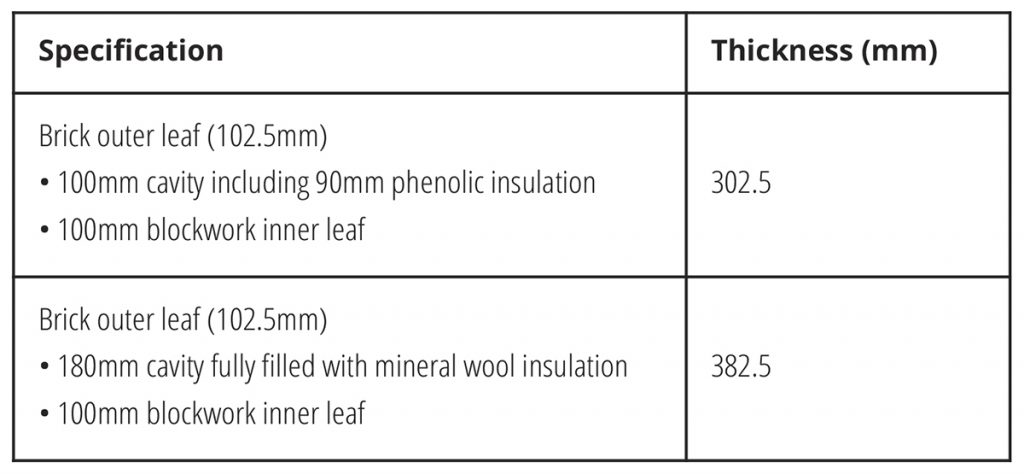
The cost analysis was then conducted by an experienced residential quantity surveyor. In addition to the upfront cost of the insulation, the analysis considered a wide range of variables linked to the cavity width and overall thickness of the external walls including the length of wall ties, rafters and joists, width of cavity closers and the extent of foundations.
In all scenarios, foundations are 300mm deep in a 600mm trench. It was assumed that the thinner cavity for the phenolic insulation specification would allow a narrower foundation of 650mm compared with 900mm for the mineral fibre specification.
Results
The analysis showed that while the cost of the mineral fibre insulation itself was less than the phenolic insulation, the increased cavity width with the mineral fibre specification raised the cost of all accessories such as lintels, wall ties and cavity closers. Furthermore, the need for more extensive foundations and associated groundworks, along with the additional roof and wall areas, also added significantly to the overall cost of the mineral fibre construction.
When all these factors were considered, the analysis showed that the overall cost for the large and small detached houses with the phenolic insulation specification and 600mm foundation was actually less than that of the mineral fibre specification with a 900mm foundation (as shown in Table 2). Meanwhile, for the mid-terraced property, the cost differential was negligible.
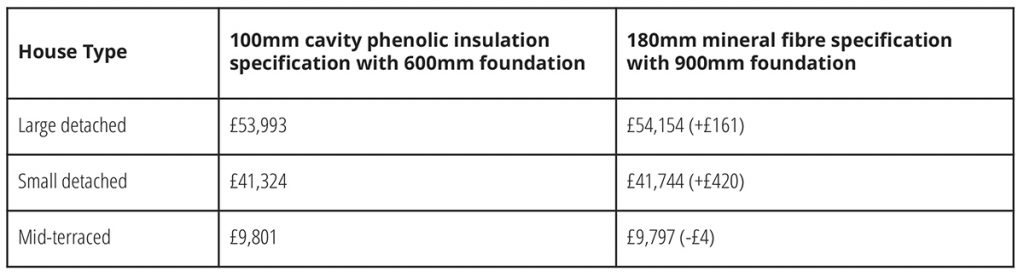
In addition to these cost benefits, the reduced construction thickness of the phenolic insulation specification should also allow window reveal depths to be minimised. Research has shown this can allow more light into internal spaces and may make them more attractive and saleable to potential buyers.
Forward-thinking approach
The zero-carbon commitment sets a clear direction for travel for the UK construction industry over the next three decades, with consultations into changes to Part L of the Building Regulation (governing the conservation of fuel and power) expected to begin in the coming months. The research from Currie & Brown shows that when specifying these materials, it is important to not only think about the upfront cost of the material, but to take a more holistic view of the overall project. With this approach, it may be possible to create lighter and more spacious properties that have lower heating demands and are cheaper to build.
Kingspan Insulation
Tel: +44 (0) 1544 387 384
Twitter: @Kingspanlns_UK
Please note: this is a commercial profile.