Sam Cocking, a PhD student at the Centre for Smart Infrastructure & Construction working under the supervision of Prof Matthew DeJong, reports on a structural health monitoring project in collaboration with AECOM and Network Rail, which is bringing smart innovation to a heritage asset
Sensing technologies are enabling asset owners to learn more about the structural performance of heritage assets and, alongside data analytics, provide valuable insights to inform better decision-making.
Our transport infrastructure is under pressure to expand and increase capacity to meet modern demand. Still vital contributors to the economy, many key assets of the UK’s current transport network were built more than 100 years ago.
Integral to today’s rail and road transport systems, many existing bridges were constructed to support canal, railway and more recently road development.
A large proportion of rail bridges are made from stone or brickwork and designed as masonry arches, which are widely acknowledged to be one of the most sustainable structures ever built. However, many have now provided service for more than a century and are meeting demands far beyond those they were designed for. These important structures also contribute to our country’s engineering heritage.
Making more of existing infrastructure
Government and industry recognise the need to focus on getting more from the existing asset base that forms the majority of our infrastructure – each year in the UK, we add just 0.5% to the capital value of our existing infrastructure. Advances in sensor technology and data analytics enable insights into how our infrastructure performs throughout its life, helping asset engineers to achieve this goal.
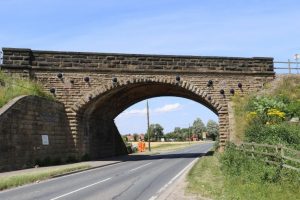
Network Rail owns, operates and develops Britain’s railway infrastructure, which includes 20,000 miles of track, 30,000 bridges, tunnels and viaducts, signals, level crossings and stations. In 2018, Network Rail commissioned AECOM and the Cambridge Centre for Smart Infrastructure & Construction (CSIC) – an Innovation & Knowledge Centre in the Department of Engineering at the University of Cambridge funded by EPSRC, Innovate UK and industry, with the aim of transforming the future of infrastructure through smarter information – to install structural health monitoring (SHM) technologies on a masonry arch bridge in north Yorkshire, referred to as CFM-5 and shown in Figure 1.
The technologies monitor how the 150-year-old bridge behaves structurally and how it is responding after repair work carried out in 2016. Network Rail also wanted to explore available monitoring technologies to determine a suite of potential structural health monitoring options which could be deployed on other masonry arch assets, as alternatives to the traditional system of deflection pole monitoring. This method measures vertical crown displacements at the arch soffit; however, it often entails difficulties with access and may require costly and disruptive road closures.
The CFM-5 bridge
CFM-5 is a single-span, skewed masonry arch bridge carrying local passenger, cross-country and freight trains. Historic damage to the arch includes separation cracks, between the arch and both spandrel walls, and a third longitudinal crack (see Figure 2).
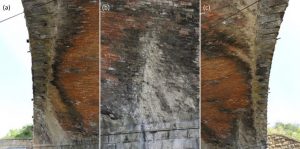
The 2016 intervention aimed to restore connectivity across these cracks, to reduce the liveliness of the arch under train loads. Crack stitching was comprehensive because the root cause of the damage was uncertain, which makes it difficult to judge the appropriateness of the intervention and the time period over which it is likely to remain effective. This provided motivation for regular condition monitoring, though alternatives to the deflection pole method were required to achieve this.
Collaborative approach
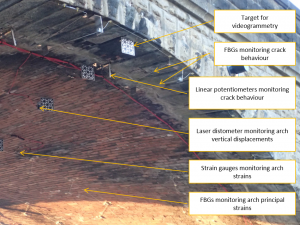
Collaboration between engineering consultancy and academia allowed for a broad range of structural health monitoring technologies, both readily available and emergent, to be used. AECOM installed an autonomous, remote monitoring system, comprising a range of dynamic point-sensing technologies such as strain gauges and linear potentiometers. CSIC implemented distributed monitoring technologies, including: laser scanning and vibrometry; fibre-optic Fibre Bragg Gratings (FBGs), for detailed dynamic measurement of strains in a variety of configurations across the arch; and videogrammetry to capture dynamic displacements. Figure 3 shows the devices which were installed on the arch soffit.
Bespoke monitoring system
Desk studies and site visits at the start of the project provided information for the specification of the monitoring installation. As part of this, CSIC deployed non-contact monitoring technologies – laser scanning to obtain detailed information on the visible ‘as-is’ geometry of the bridge and laser vibrometry to measure magnitudes of its dynamic live load deformations.
This highlighted environmental constraints and risks, particularly in relation to the A162 road and public footpath that CFM-5 crosses, which allowed mitigation of these hazards to be designed into the monitoring installation. For instance, locations were identified where videogrammetry equipment could be set up and operated at a safe distance from the road, which remained open throughout monitoring. Installation of videogrammetry targets was designed to accommodate the equipment being used in these locations.
Insight into past behaviour
The laser scan data was also fed into algorithms developed by CSIC to investigate historic arch deformations. These algorithms generated best-fit reference arch geometries, simulating its most likely ‘as-built’ condition, and compared the laser scan data against these references. The differences between these two data sets corresponded to the most likely historic deformations of the arch over its working life. By considering the mechanisms that arise in an arch subjected to various support movements, these deformations could then be used to predict the most likely support movements that had occurred at CFM-5 to lead to its current, deformed profile, including the magnitudes of these movements.
Using this technique, the historic behaviour of CFM-5 could be considered alongside its current response, as measured by the monitoring installation. This allowed for the fullest possible picture of structural behaviour to be developed.
Installation and monitoring data
Installation of the monitoring technologies was carried out across seven 10-hour night shifts, under full road closures. During this, monitoring data was recorded to test the equipment, which confirmed the trigger levels that had been programmed for certain devices to automatically start recording data as trains passed. Most methods were automated using these trigger levels, although videogrammetry still required manual operation.
It was economically viable for AECOM to automate their point-sensing network from the start of the project. This system, powered by a solar panel, recorded real-time data for train events and transmitted it to AECOM’s offices for analysis. Meaningful trends could be extracted by matching recordings to individual trains, for which information was available covering train class (and hence approximate load), train direction, number of carriages, and operator/route. AECOM developed new algorithms to perform this task.
Next steps
AECOM and CSIC analysed large quantities of data to co-author a series of reports for Network Rail. These summarised: the studies undertaken before installation; the reasons the system was chosen; evaluation of the technologies used; and the results to date.
An upcoming report will provide guidance on SHM technologies that could be used as alternatives to the deflection pole method. These reports will also be submitted to the European Shift2Rail programme as examples of research that Network Rail is supporting.
Network Rail is commissioning AECOM and CSIC to perform long-term monitoring of the bridge, which demonstrates the value of the installed monitoring system and the benefits of long-term structural health monitoring. As part of this, the CSIC FBG system will be upgraded to be autonomous and self-sufficient, utilising AECOM’s solar panel. This will enable FBG monitoring data to be captured automatically and transferred back to CSIC’s office.
The team have also presented the project results to other asset engineers at Network Rail to demonstrate the technological advances that can aid asset management into the future.
Benefits
Advances in sensing technology are enabling asset owners to learn more about the structural performance of heritage assets, while data analytics can distil large amounts of sensing data to provide valuable insights that can inform better decision-making. This project has enabled CSIC to continue the development of fibre-optic monitoring of heritage structures and carry out research into the fundamental behaviour of a heritage skewed masonry arch railway bridge. The project also provides an important comparison of emerging sensing technologies, to allow refinement and optimisation of future bridge monitoring systems so that these can better target the essential information needed to make decisions.
An AECOM spokesperson said: “The collaborative working arrangements between AECOM, CSIC and Network Rail enabled the organisations to bring complementary skillsets to this SHM research project. The project was a real success and all parties are excited about the future direction and potential of these techniques to improve management of these critical assets.”
On Track
This project is shortlisted in the 2019 NCE TechFest Awards for the Best Use of Technology: Driving Whole-Life Performance Award and the Team of the Year Award, which celebrates project teams driving development and adoption of innovation and technology in the civil engineering industry.
Alongside another CSIC project, it has also been shortlisted for the Rail Visionary Award, which recognises organisations developing pioneering ideas and designs to realise major changes in the global rail sector. Winners will be announced on 26 September.
Sam Cocking
PHD Student
Centre for Smart Infrastructure & Construction
Tel: +44 (0)1223 746976
www-smartinfrastructure.eng.cam.ac.uk
Twitter: @CSIC_IKC