Numerical analysis has major advantages over traditional methods regarding the level of detail and insight that can be obtained in geotechnical stability analysis, limit-state design, and soil-structure interaction problems
The key success factor in numerical analysis is an appropriate determination of constitutive model parameters based on the available, and often limited, soil data, and on engineering judgement. Prediction competitions demonstrate a large variety of results when different engineers solve the same problem. The question becomes whether automated parameter determination could narrow the variety of results and increase confidence in using and accepting the results from numerical analysis for geotechnical design.
From traditional methods to numerical analysis
Traditional geotechnical analysis and design methods, implemented in easy-to-use computer software, have been around for more than 35 years. They are well accepted in geotechnical design. In this respect, it is good to realise that easy-to-use numerical analysis software, based on the Finite Element Method or the Finite Difference Method, has also been available for 30 years, but is far less accepted in geotechnical design. It’s worth noting that in those 30 years, numerical methods and constitutive models have evolved and improved dramatically, whereas traditional methods are essentially still the same.
Given the advantages offered by numerical analyses, why is our geotechnical profession using old and less sophisticated methods whereas other disciplines seem to be innovating and adopting new technology much faster? Four reasons:
- Limited availability of soil data, variability in the methods of obtaining and interpreting this data, and the (mis)perception that this prevents the use of advanced numerical analysis
- Limited knowledge about the fundamental mechanics incorporated in numerical methods and constitutive models
- (Mis)perception that numerical analysis is time-consuming and less productive
- Limited confidence and understanding in the results of numerical analyses from a “black box” software application
The too-often limited availability of soil data and limited knowledge are the main reasons why geotechnical engineers are reluctant to perform numerical analysis. The (mis)perception that numerical analysis is time-consuming and expensive is a reason for managers to persist in the use of traditional methods, thereby overlooking the benefits that numerical analysis will bring (if performed correctly), namely:
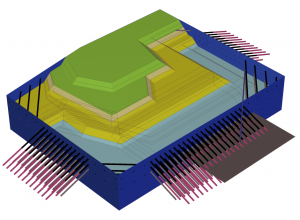
- Solving multiple engineering and design issues in one analysis
- Providing more insight into the soil response and soil-structure interaction, and the sensitivities therein
- Ability to realistically model complex situations and coupled processes [Figure 1]
- Opportunity to further optimise the overall design.
Limited confidence and understanding are a primary reason that geotechnical engineering consultants are reluctant to recommend and conduct numerical analyses as part of the scope of geotechnical engineering and design services.
A common perception is numerical geotechnical analysis is difficult; mainly because numerical models require more parameters to be determined than traditional methods. In numerical analysis, the soil’s stress-strain response is simulated by means of constitutive models. The models describe the soil behaviour qualitatively, while model parameters quantify specific aspects of that behaviour, such as stiffness and strength. Note that model parameters (e.g., a reference stiffness parameter in a formula for stress-dependency of stiffness) are principally not the same as soil properties (e.g., particle composition and pores, relative density, water content, plasticity index, and so on) or soil parameters (e.g., friction angle, undrained shear strength), although the latter may also serve as model parameters. Also, note that soil properties might change over time, or, as a result of the evolution of stress and strain during loading (e.g., grain crushing), whereas model parameters are supposed to be constant. In principle, proper selection of the constitutive model and the corresponding model parameters can properly account for the associated changes in soil behaviour.
Once an engineer has crossed the threshold and started performing numerical analysis, it takes another step to advance from using simplified, linear-elastic, perfectly plastic constitutive models to more complex, non-linear elastoplastic models. In general, more complex models include more features of soil behaviour, but also require more model parameters to be determined. Nevertheless, for many engineering issues it’s essential to take this next step, as illustrated by the following dialogue:
Neighbour: “You’re digging a big hole right next to my house; it will settle and get damaged!”
Mr Wiseguy: “Don’t worry. My numerical analysis has determined that your house will heave.”
Using too-simple constitutive models might lead to the wrong conclusion. Hence, when performing numerical analysis, it must be done thoroughly using constitutive models that capture the essential features of soil behaviour required for the application considered.
Model parameter determination
Ideally, the determination of constitutive model parameters is based upon comprehensive site investigation data and laboratory testing on high-quality soil samples. Project owners should be convinced that site investigation and lab testing are not just costs; they are investments that, provided they are thoughtfully planned and properly conducted, pay off by reducing project uncertainty and risk.
In my paper in GSP 128, I offered an overview of methods of parameter determination for various constitutive models. Proper parameter determination should be performed in conjunction with the application (e.g., stress levels, stress paths, strain levels, and loading rate), at least when simplified soil models are used. In this way, soil features lacking in the constitutive model can, to some extent, be “compensated” by adapting model parameters, but this can be risky. Hence, another reason why more advanced constitutive models are preferred is that their parameters are generally less dependent on interpretations by the engineer.
Parameter determination can be based upon:
- Correlations with field test data (from SPT, CPT, or DMT)
- Correlations with soil index properties like liquid and plastic limits, plasticity, and liquidity indices, and relative density
- Results from laboratory testing (triaxial, oedometer, direct simple shear)
- Tables, charts, databases
- Engineering judgement
Every method provides different parameter values and has its validity, restrictions, and limitations. The selection of model parameters requires knowledge of the methods and, more importantly, of their validity, restrictions, and limitations. The outcomes are not unique and must be properly interpreted, based on experience and engineering judgement. This makes parameter determination a difficult task.
A paradox
The technical ability to properly execute numerical modelling, with the most appropriate constitutive models and corresponding parameters selection, is a true sign of modern geotechnical engineering expertise and experience. A certain number of practising geotechnical engineers, who have used numerical methods and advanced constitutive models for several years, have developed their own workflow process for parameter determination. They have composed databases with local data, collected correlations from literature, created their own, elaborated formulas, and implemented them in spreadsheets and tailored software applications. They are the experts. Combined with their engineering judgement, it gives them a competitive edge in numerical modelling, and they sit on it; it’s their bread and butter.
New or infrequent numerical model users would love it if they could somehow benefit from the expert’s wealth of experience and data they possess. Such data as well as sets of correlations and their valid domain of application, and other sources of information, could be made available in public software to help determine model parameters. Some commercial software contains collections of correlations to generate soil parameters, but there is no publicly available software that automatically determines model parameters for advanced constitutive models based on site investigation data.
Most of the experts reject the idea of automatic parameter determination, even though, if properly implemented, automated parameter generation applications might provide a significant benefit to the industry.
Quality and reliability of numerical analysis
The quality of results from numerical analysis highly depends on the ability of the user to select the right constitutive model for the application considered and the model parameters needed for them. Data from prediction competitions and benchmarks show a large bandwidth of results, even if the application and corresponding soil data are clearly defined. This uncertainty does not contribute to the confidence in the use of numerical analysis for geotechnical design purposes. To build confidence, numerical methods and constitutive models used must be transparent, results must be validated, and the uncertainty bandwidth should be narrowed.
The quality and reliability of numerical results can be improved by combining the following elements:
- Education – Teaching/learning about the capabilities and limitations of constitutive models and numerical methods, and how to properly determine the parameters used in the models
- Experience – Practicing model parameter determination on published benchmarks and applying it in real applications to build the necessary experience
- Exchange – Exchanging and sharing knowledge and experience among geotechnical engineers in industry and academia
Despite the decades of attempts to accomplish these three elements via conferences, workshops, communication channels, online platforms, and so on, it seems that the (mis)use of numerical analysis in geotechnical design is growing at a faster rate than the quality of their results.
Automatic parameter determination
An effective way to go forward is to develop an online software application that automatically characterises and interprets the soil stratigraphy based on standardised site investigation data, and the subsequent automatic selection of constitutive models and corresponding model parameters for the different soil layers in the profile. The idea is that automation makes parameter determination less dependent on the user and reduces the variability of results. It is meant to mitigate the human factor.
Interpreting the soil behaviour type (SBT) and soil layering from field tests is common practice. All geotechnical engineers should be familiar with the SPT interpretation methods of Meyerhoff and the CPT interpretation diagrams from Robertson & Campanella. These data provide the geometric information about the thickness and lateral distribution of soil layers and the corresponding SBTs, which can be automated straightforwardly. For numerical analysis, a certain minimum layer thickness should be used to avoid generating very thin soil layers. This means that some manipulation and “averaging” of thin layers is needed while maintaining the influence of weak layers.
Automatically selecting the appropriate soil constitutive model must recognise and capture the essential features of soil behaviour for the soil type as identified from field testing and, ideally, good quality laboratory testing. In most cases, the selected model will be an advanced, non-linear constitutive model that takes stress level-, stress path- and strain-dependency of soil behaviour into account. Different models can be used, depending on the soil types encountered or the different types of analysis to be conducted. For example, a dynamic liquefaction analysis of silty soil layers might require a specific constitutive model be used, but it might not be the best model for static deformation analysis. The selected constitutive model implicitly defines which model parameters need to be determined.
To automate the selection of the model parameters, all commonly available knowledge should be implemented in an expert system. The system must “know” the validity and limitations of the correlations, formulas, charts, and tables in it. The system must also be flexible and extendable to new information as it becomes available and accepted in practice. It should have an algorithm to automatically generate valid correlation paths (i.e., chains of correlations) that link measured field-test quantities to model parameters via intermediate soil properties (e.g., relative density, plasticity index) and soil parameters [Figure 2]. Because in many cases more than one correlation will be valid, there are generally different paths, with different correlations and possibly different path lengths, which lead to the same model parameter. The system must be able to cope with multiple parameter values and check the outcomes. After eliminating the outliers, a mathematical procedure (i.e., a weighted average or more sophisticated procedure) can be applied on the remaining parameter values to calculate the final parameter value to be used in the analysis. Parameters determined in this way are supposed to be representative for serviceability limit state (SLS) situations, whereas for ultimate limit states (ULS) the applicable design approach with partial factors can be applied. Doing this for all model parameters and for all soil layers provides a collection of automatically generated material data sets (constitutive model + parameters, representing each type of soil) that can be automatically assigned to the corresponding soil layers in the numerical model.
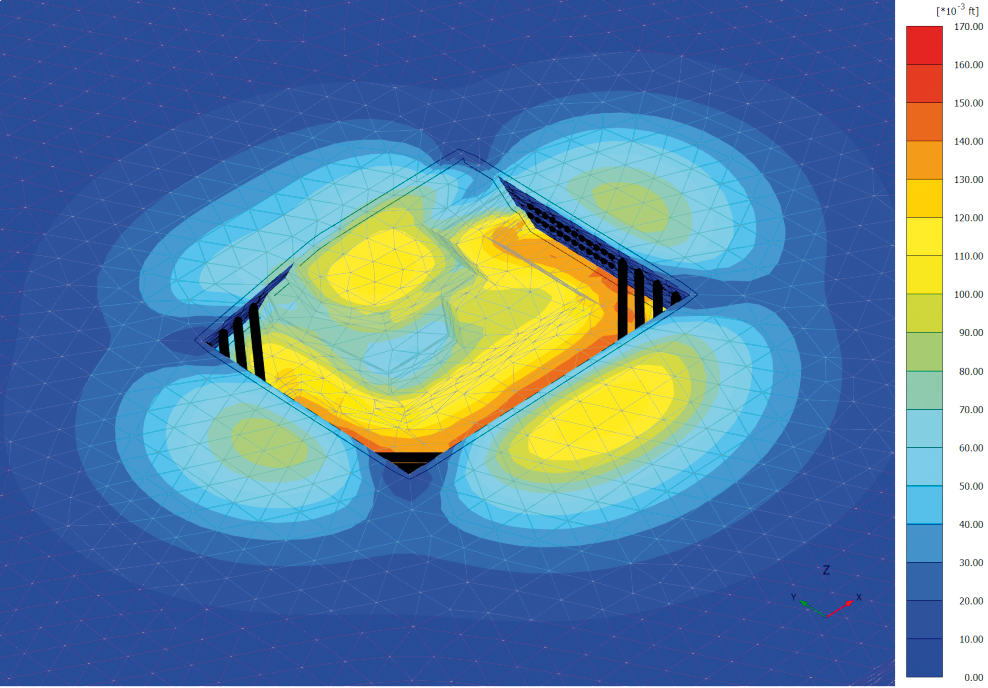
The automated procedure for constitutive model and parameter selection using standardised site investigation data is visualised in this flow chart:
1. | Automatic determination of soil types and layering from field test data | ||
2. | For each soil layer: | ||
a. | Automatic selection of appropriate constitutive model; this defines which model parameters need to be determined | ||
b. | Automatic selection of all applicable and valid correlations and formulas | ||
c. | For all model parameters: | ||
i. | Automatic creation of valid correlation paths from basic soil data via intermediate parameters to the model parameter | ||
ii. | Automatic determination of the outcome (parameter value) for all valid paths | ||
iii. | Automatic check of parameter values against an expected range and elimination of outliers | ||
iv. | Automatic calculation of final parameter value based on all valid values |
Liability and validation
Although automated constitutive model and parameter selection should lead to more consistent and more reliable results, the ultimate responsibility and liability for geotechnical design remain with the engineer. This means that the engineer must verify and validate the material data sets that are automatically created. Therefore, the procedure of automatic parameter determination must be transparent and verifiable.
Validating the behaviour represented by the constitutive model and its parameters can be done by simulating laboratory tests [Figure 3] and comparing the resulting stress-strain curves with high-quality laboratory test data, which is, ideally, part of a standardised site investigation report. Such a comparison gives a feel for the accuracy at which real soil behaviour is approximated by the model, and it offers insight into the capabilities and limitations of the model.
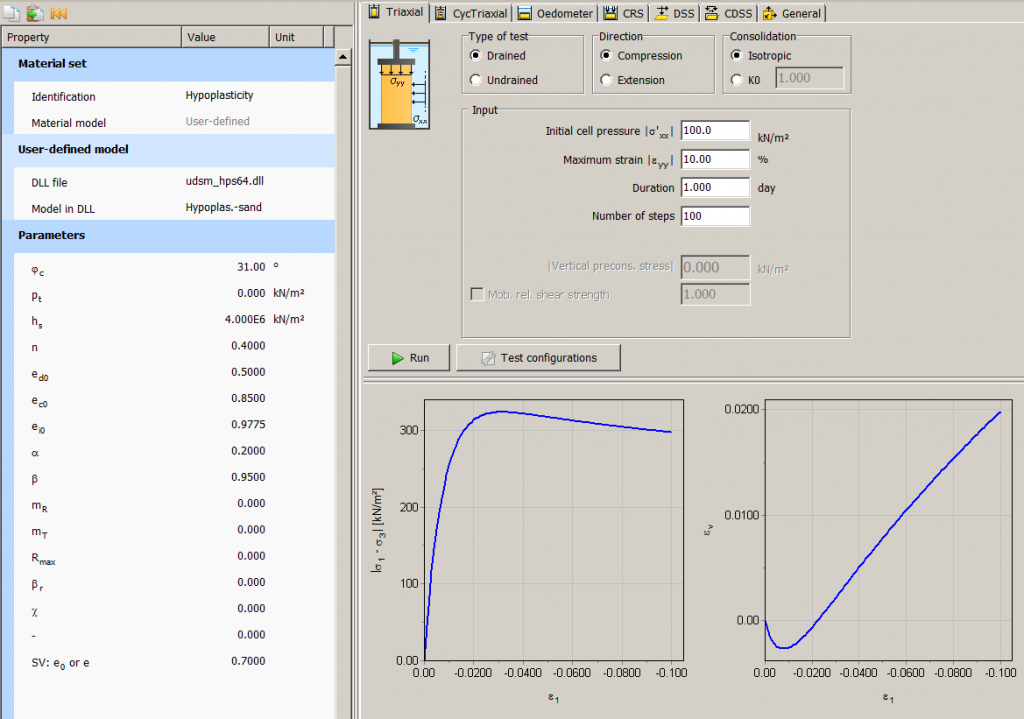
The next step
To date, geotechnical design is still largely based on traditional methods that are decades old. Numerical analysis continues to show great potential in providing more insight in the overall behaviour and to optimise the overall design, and the use of numerical modelling continues to expand within the industry. However, with increased use comes increased risk for misuse and misinterpretation. Automated soil constitutive model and parameter selection might provide an application to help mitigate the human factor, reduce the variability of results, and increase confidence in numerical analysis. If we join forces, we can develop such an application together, for the benefit of our profession. Anyone who’s interested is welcome to participate.
Ronald Brinkgreve, Ph.D., is the director of geotechnical research with Bentley Systems. He joined the company through Bentley’s acquisition of Plaxis. Brinkgreve is responsible for all geo-engineering related research and development of the PLAXIS Finite Element software. He is also an associate professor at Delft University of Technology. Brinkgreve’s main research interests include soil constitutive models and numerical methods. He can be reached at ronald.brinkgreve@bentley.com.