Construction data is key to achieving a greener, cleaner built environment, says Lee Jones, acting head of sustainability at Byggfakta Group and head of manufacturing solutions at NBS
The built environment is responsible for 37% of all global carbon emissions, meaning the construction industry has a crucial role to play in tackling the climate change emergency. For specifiers and building designers, it means a focus on greener, cleaner building materials and full transparency from building manufacturers as to the carbon impact of their products.
Construction professionals need to consider both direct and indirect environmental impact. Direct effects can be managed through things like energy and water use, committing to reducing carbon emissions. However, managing indirect impact requires being aware of materials, products and supply chains, including responsible sourcing.
Data-driven decision making
According to the Treasury and Green Construction Board, whole-life carbon has the most potential to be reduced at the design and planning phases. To leverage this successfully, specifiers and the broader project team need access to much better information.
This has resulted in rocketing demand for concise and structured information when it comes to building products. Detailed product information is now vital for delivering lower carbon outcomes on building projects because it allows specifiers to understand the environmental impact of each product – and the appetite will only increase.
During the design process, the specifier should be considering the whole-life costs of a material, product, system and, of course, the final building. Long-term costs can be reduced by specifying more durable options. While these may have a higher initial price, designing in sustainability from the outset can help mitigate the increase in overall project costs.
There are numerous opportunities to consider whole-life costs when specifying, and digital specifications and BIM processes allow specifiers and architects to make the most informed decisions possible. With sustainability front of mind, access to a robust database of construction product information allows for quick and efficient decision-making. Overall, it means better choices when specifying and ultimately, improved building quality.
Additionally, the ability to log specification records throughout the project lifecycle creates a traceable history of decision-making – supporting the much sought-after Golden Thread. This makes it easier to verify what was originally specified and why, so that construction stays as close to specification as possible.
Stepping up to the mark for a cleaner built environment
Building projects involve a lot of collaborators and as digital uptake increases, stakeholders at every step of the way need to ensure that they are doing their part. Manufacturers can do this by supplying comprehensive detail around the green performance credentials attached to each product in a digitally supplied format, which helps specifiers put their best foot forward when it comes to lowering carbon. However, for this process to be successful, it needs consistent and regular updates, as well as complete transparency in terms of the carbon footprint of a product.
Unfortunately, many green claims are not backed by third-party certification and can’t be substantiated. Manufacturers should look to provide certifications like Environmental Product Declarations (EPDs) to help specifiers gauge sustainability during product selection. EPDs are objective, third-party verified documents that provide transparent sustainability data around a product’s lifecycle.
Planning for tomorrow, today
The most recent Intergovernmental Panel on Climate Change (IPCC) report found that even with the progress we’ve made, the increase in global temperatures is very likely to exceed 1.5C by the early 2030s. Now, more than ever, the construction industry needs to take actionable steps to improve sustainability. Net zero targets are now on the horizon, and digital specification and building product data will certainly aid the industry on its mission to lower carbon emissions.
There’s a clear business case that BIM and other digital capabilities will help specifiers tackle the increasingly complex level of Building Regulations. Legislation, such as the Future Homes Standard, Building Safety Act and Fire Safety Act will all be underpinned by compliance supported by digital data. It’s said that “data is the new oil” and it’s easy to see why – construction data has the power to improve sustainability across the board while producing safer buildings in the process.
Lee Jones
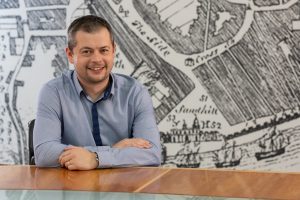
Head of manufacturing solutions
NBS Tel: +44 (0)345 456 9594