Gavin Bonner, head of digital engineering at Cundall, discusses the role of BIM and digital technology in decarbonising the built environment and why data is key to unlocking our net zero ambitions
At Cundall, digital engineering focuses on the use of data-driven technologies and processes to improve and further enhance how we deliver projects to our clients. Our primary aim is to collaborate with our clients and industry to deliver energy and the carbon solutions necessary to keep global heating below 1.5C. We believe digital engineering will play a significant role in how we do this.
We are now at a point where new and emerging technologies like artificial intelligence and machine learning are converging with more maturing technologies such as BIM. This, in turn, will generate a new wave of innovation over the next 10 years like we have never seen before. But before we truly benefit from these advances, we need to digitally evolve faster as an industry and the way to achieve this is through use of “intelligent data” to drive transformational decisions in the future buildings we design, thus delivering on the net zero promises we make now.
Is data the key to unlocking our industry’s net zero goals? 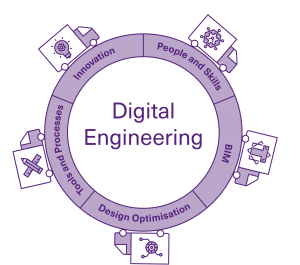
For a start, we need to stop saying that “data is the new oil” because it is so much more than that, and the concept is just wrong. Oil is valuable due to its scarcity; data is reusable and arguably becomes more beneficial every time it is analysed. Collecting and analysing data enables teams
to make better informed decisions on how future projects are designed and constructed, but the true benefit may come from how we analyse data during a building’s operational phase regardless of whether it’s a new build or retrofit.
Data-driven design should be our key motivator at all levels for any decisions for net zero outcomes. The more data we collect, the better the ability we must develop for out data-driven design protocols and procedures, which in turn should further develop into even better processes, such as generative design, which will enable us to explore thousands of combinations and iterations to reach the best solution based on the criteria we set for the most optimal building solution. We have only begun to scratch the surface in what we can achieve as an industry when it comes to analysing data and applying data-driven approaches to how we design, construct and operate our low carbon buildings of the future.
Could digital twin technology be the gateway to net zero?
Recent studies have shown that digital twins can reduce the greenhouse gas emissions of an existing building by up to 50%, as well as delivering cost savings of up to 35%. The UK government has already begun to invest and has established a National Digital Twin programme through its Centre for Digital Built Britain, a collaboration with the University of Cambridge, to build an eco-system that connects digital twins across enterprises, allowing them to share data more readily. This is all great, but we need to do more.
The concept of the digital twin could revolutionise the future of buildings and truly facilitate a faster route to achieving net zero buildings. The benefits are clear to see, from real-time data to help identify inefficiencies in a building to monitoring with IoT devices for proactive maintenance and improved energy use.
But there is a significant issue we need to address around the affordability of digital twin technology that does not normally get discussed. For digital twin technology to become mainstream across the whole AEC industry, the technology adoption and installation costs must be minimised if we want to realistically push this technology as a driver for achieving net zero buildings. We need commercially viable digital twin solutions that give the same benefit to building owners regardless of whether it’s a multimillion-pound new build project or a small retrofit project. We must make this affordable for everyone.
Does BIM need to be mandated on all retrofit projects and existing buildings?
It is estimated that 80% of the buildings we will have in 2050 already exist today. This is a well-versed statistic but one that normally gets overlooked slightly from a digital perspective. There needs to be an increased focus on digital and retrofit to maximise the value and performance of our existing buildings, and digital processes can provide a great opportunity to do this. Despite the urgent need to improve the quality and the functionality of the existing building stock, all the processes related to its transformation are still carried out with traditional methods and procedures.
The opportunity for BIM to support existing built assets in the future is pivotal if we are serious about reducing carbon emissions on existing buildings, particularly when linked to asset and facilities management, whole-life costing and incorporating programmes into the models. As the government did with the BIM Level 2 approach in mandating BIM on all publicly procured projects, we almost need a similar approach (minus the confusion) on how we develop, update and report on existing buildings. This, in turn, could potentially push building owners to digitise their assets through a “scan to BIM” process.
We have already seen the impact BIM has had with increased adoption of offsite manufacturing, which has significantly improved the quality of building components and materials used, ultimately helping reduce the overall cost and minimising waste compared to doing similar work on site. BIM has a huge role to play in how we maintain our existing buildings but we need to incentivise building owners to digitise their assets to see the full potential.
Why we must look closer at emerging technologies for net zero solutions
We are all now starting to visualise the benefits artificial intelligence can bring to the fight against climate change but that aside, there are other technologies just around the corner waiting patiently, quietly growing before that explosion on to the scene. We have seen it in the late 1990s with the internet and we are about to see it again with blockchain technology. This is a technology that is already heavily disrupting other industries.
When we talk net zero, we constantly hear about the need for transparency and accountability, which are just some of the fundamental characteristics you get with blockchain. Imagine a digital twin linked to a blockchain thus allowing unfalsified collection of operational energy data saved through an immutable ledger. This provides the transparency and authenticity on how we truly report on the data that’s important to fully understand where we are on our journey to achieving our net zero goals.
Blockchain technology can answer a lot of the issues around the security of data. The security and immutability being guaranteed by blockchains will take digital twins to the next level in the years to come. Add to that its supply chain transparency or peer to peer energy trading via smart contracts, blockchain is here to stay and has its eyes firmly set on disrupting the traditional and outdated construction processes.
Gavin Bonner
Head of digital engineering
Cundall
Tel: +44 (0)20 7438 1600
https://twitter.com/Cundall_Global
https://www.linkedin.com/company/cundall/
https://www.youtube.com/channel/UCMJrbvSUW_eoNd-qmqk0gQQ/videos?view_as=public