Build2Spec aims to meet EU energy efficiency targets by tackling the energy performance gap for both new and retrofit buildings. Divya Deepankar and Chris Thompson of BSRIA’s Sustainable Construction Group discuss their work in this ambitious project
The UK construction industry has long been faced by the problem of the difference between energy consumption of an asset assessed during the design stage versus what is actually consumed during operation. This is referred to as the ‘performance gap’.
The energy performance gap in buildings is the difference between the predicted energy performance of a building and its performance as-built. The difference accumulates through the design and operation stage and may result in buildings using up more than double their expected energy. Performance gap issues can occur at one or more of the following stages: Briefing, design stage, construction, commissioning, handover and in-use post occupancy.
The Built2Spec project aims to deliver the ambitious objective of meeting the EU energy efficiency targets by reducing the energy performance gap for both new buildings and retrofits. The project recognises that an integrated approach in which all important aspects of a building, from the design stage through to construction, commissioning and operation, are considered and can help reduce the performance gap often reported.
In order to achieve this, the Built2Spec project will deliver a new set of breakthrough technological advances such as 3D and imagery tools, building information modelling (BIM), smart building components, energy efficiency quality checks, indoor air quality tools, airtightness test tools, thermal imaging tools and acoustic tools; all of which will be connected to a virtual construction management platform (VCMP) supporting the collection and sharing of all project data, from initial design to the delivery.
The basic idea is to develop a process that makes it easier for the contractor on-site to achieve higher building standards without the need for an architect to inspect everything, while also allowing all associated parties to collaborate on a common platform to achieve better buildings.
The Built2Spec project consortium involves 20 partners, with Nobatek as the overall project coordinator. The technical parts of the project where BSRIA’s contribution is involved include: Stand-off U-value assessment, ie the use of thermal imaging to determine U-Value; low pressure air tightness testing; 3D model acquisition and imagery techniques; building information modelling (BIM); training and dissemination; and communication activities.
Currently, BSRIA has been involved in determining the requirements to integrate thermal inspection techniques with a VCMP system by looking at the technology involved, training specifications, systems operation and identifying potential limits for both now and in future.
The general idea is to create a platform for a construction worker with limited training to perform quality checks using a thermal imaging camera. The results would then be uploaded on the VCMP system so that the progress of construction could be easily monitored. Figure 1 illustrates this idea of the thermal imaging self-inspection system. Some of the main areas in need of development are outlined below as:
A) Location system.
B) Thermal imaging device.
C) BIM and thermal modelling software.
A) Location system
The ability to determine the location of the thermal imaging camera is key to the success of the system. The system put in place to do this would need the location to be as accurate as possible, locating the position, the field of view (FOV), elevation, orientation and distance to the object being imaged.
Many systems such as Structure, Google Tango tablet devices and Bluetooth Low Energy (BLE) technology for smartphones were researched to fulfil this purpose. The BLE system would use BLE devices located around the building from which a Bluetooth-enabled device such as a smartphone could receive the signal and determine its distance from each BLE device. BLE has its limitations as it relies on comparing signal strength between beacons to estimate distances from each, but the signal strength can also be affected by building components and features that intervene and by materials that cause reflections. The BLE system’s accuracy may prove too poor to make it useful for camera location systems so it was concluded that further research would be required. Google Tango or Structure could prove useful as they can provide accurate orientation and direction due to their 3D mapping capability.
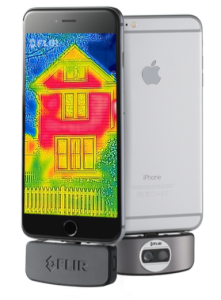
B) Thermal imaging device
Currently, a qualified professional equipped with an expensive thermal imaging camera is essential to take good quality, high resolution images and determine what is shown in the images. Having a qualified thermographer present at multiple stages during the construction process would be very expensive. Therefore, this project explored the possibility of having a site worker take the images.
The Flir One model cameras for smartphones (Figure 2) were researched by comparing the cost, technical specification and performance with a mid-range thermal camera, the T360 from Flir. After multiple tests, it was determined that the Flir One would be suitable for basic quality checks, such as correct installation of insulation. The Flir One could also take advantage of the smartphone features, such as being able to take a composite panoramic image shown in Figure 3, along with the added functionalities of a smartphone, which would help simplify other aspects of the project such as sending and receiving images.
C) BIM and thermal modelling software
Thermographers often have a problem in determining the building fabric composition being imaged, which could be solved by connecting BIM models and thermal images for analysis and quality inspection. With a location system working alongside the thermal imaging system, the images could be located on the building model, making comparison easier. This process could be improved further by feeding the environmental data collected on-site as input to the building model using the dynamic thermal analysis software to create a site-accurate 3D thermal model. This model could then be compared to the thermal images via location system placement; however, the software to perform these functions does not exist yet.
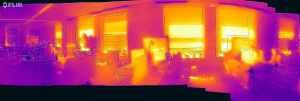
The future
The Built2Spec project is advancing the boundaries of construction practices. Some goals, such as using smartphone cameras for quality inspection, may be achievable in the short-term. Others, such as implementation of a complete system which would change the process of construction management, are long-term. This will help the industry realise the potential of new technologies in construction practices by bringing
together different areas of the process of building a centralised system, leading to more efficient building construction. The implications of Built2Spec extend beyond just achieving better energy performance; it could result in a more efficient building industry shaping better buildings with higher quality standards in all aspects.
This project has received funding from the European Union’s Horizon 2020 research and innovation programme under grant agreement No 637221. The sole responsibility for the content of this article lies with the authors. It does not necessarily reflect the opinion of the European Union. Neither the EACI nor the European Commission are responsible for any use that may be made of the information contained therein.
Divya Deepankar
Chris Thompson
Research Engineers
Sustainable Construction Group
Tel: +44 (0)1344 465 600
Twitter: @Energy_BSRIAWMI