Architect Lukas Thiel of White London Studio compares the rise of Modern Methods of Construction in Sweden and the UK, the difference with traditional building and calls for a clear vision for their successful adoption
Over the last five years, I have been working in a London studio on UK projects, but prior to this I was working as an architect in Sweden. Moving to the UK, I have been impressed by the high levels of enthusiasm for MMC and Design for Manufacture and Assembly (DfMA) within the industry and the exceptional levels of expertise in MMC research and engineering.
Since the first UK projects I have worked on started, however, there have been profound changes affecting the uptake of MMC. First, the Brexit referendum and the negotiations that followed then significant regulatory changes (most notably Part B of the Building Regulations), creating uncertainty regarding both supply chains and certified solutions. On top of that is the ongoing Covid-19 pandemic, which is changing the nature of construction sites.
Taken together, these changes have served to highlight the major shift that is needed to make MMC and DfMA viable and cost-effective options for housebuilding in the UK, turning it from an option that receives initial enthusiasm at the outset, only to be dropped in the face of compound obstacles, to one that is readily embraced from conception through to delivery.
Major shift towards MMC and DfMA
For me, the first step in thinking about this “major shift” is breaking it down and examining the key points of difference between modern and traditional methods of construction, which must be recognised and acknowledged – along with the impacts and challenges of change.
First and foremost to any shift is that the use of MMC and DfMA must be rooted in system process thinking; it must also be the foremost consideration in a project’s initial viability assessment. Lead-in times for MMC are longer than traditional methods of construction, so careful planning that starts at the very initial stage of a project must be put in place to avoid unnecessary pressures on contracts and supply chains.
Linked to this is the way that a project team is resourced and structured. Before a factory can go into production with building elements, every single design decision, around each and every element, must be made and signed off. Because production is such a key consideration in the MMC design process, a member of the MMC subcontractor should be on the design team, from RIBA Stage 2 and onward, to ensure any factory-specific limits linked to the means of assembly are incorporated into all decision making. Architects, more generally, need to invest, or receive funding, to make a basic understanding of MMC prerequisites and limitations part of their toolbox.
The developer also needs to plan for a different business scenario, as cost is distributed very differently through the process with MMC than with traditional means of construction. With MMC, designers spend more time in the earlier stages compared with traditional construction, and there is a substantial upfront cost for manufacturing MMC before construction starts on site. Whereas cost on manual labour and the contractor’s workforce is less, as is time spent on site, once the volumetric modules arrive on site. It is for this reason the shift to MMC in Sweden has largely been driven by the manufacturing industry and contractors forming their own development companies.
MMC logistics are also very different, with an emphasis on just-in-time delivery, with confirmed access routes for large building components. Of course, the different skillsets required for MMC must impact on local training, so as not to negate local job opportunities and uptake.
Difference between the UK and Scandinavia
A fundamental difference between the UK and Scandinavia, where MMC is prevalent, is availability of materials. Scandinavia is to a large extent covered in forest and the timber from these forests is stronger, structurally than that grown in the UK. With fewer CLT manufacturers in the UK, bottlenecks occur and competition on price is limited.
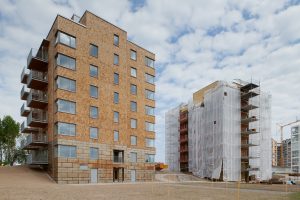
Of course, with Brexit, the emphasis on sourcing materials for construction within the UK is more prescient than ever, to overcome increased tariffs and concerns around delays. And so more innovative solutions need to be found. One such suggestion for promoting UK-sourced timber lies in the use of shorter structural spans, restricting plan layouts. Another could be the introduction of steel and CLT hybrid frames, which to date have been used exclusively for non-residential buildings to provide long spans and freedom of layouts.
There is also a very key role for local authorities (LA) to play when it comes to championing the use of MMC and CLT in the provision of new affordable housing. LAs can promote a shift through wholly owned development companies or in-house teams and when setting up their frameworks; also creating opportunities for contractors willing to invest in MMC know-how and production pipelines.
The use of MMC in housing, however, is also dependent on supportive legislation and certification through testing. It is key that MMC and CLT are supported together by regulations for it to be a viable option. There have been a number of legislative changes in recent years, driven by climate change and fire risk mitigation, that carry conflicting implications for both.
The release of Building Regulations Part L 2020, regulating conservation of fuel and power, is imminent and will serve as a stepping stone to even more stringent regulations expected by 2025. It is already challenging to meet regulations regarding overheating and limiting energy spent on maintaining a comfortable inner climate. The stricter regulations will have even more impact on building design and could ultimately pave the way for MMC, which provides better quality control, improved air tightness, and less waste.
There are obvious health and safety benefits in producing building elements in controlled factory environments. Further to this, using façade modules or volumetric elements reduces risks from accidents such as falls when in construction on site.
Use of CLT
The use of CLT, however, is currently subject to an emotional stigma, after being ruled against in Dame Judith Hackitt’s report that followed the tragic Grenfell fire. This ruling impacts on how CLT homes are treated by mortgage lenders and insurance companies, creating a deterrent effect for developers and homebuyers, resulting in the system favouring less sustainable MMC solutions, or even traditional means of construction.
This is despite extensive fire testing in other countries, such as the US, Canada and in other areas of Europe, where regulations allow the use of CLT in residential buildings. National testing and certification of CLT structures, including façade build-ups, is needed if CLT is to play a deciding role in providing new climate positive housing.
CLT frames have a number of advantages over precast concrete, which is why I hope that the issues with regulations and standards will be resolved. To name just a few:
- Building elements are significantly lighter, saving cost on substructure, crane capacities and transports while minimising risk when manoeuvring on site.
- Ease of carrying out building work and making any adjustments on site, using quiet handheld tools.
- Ease and speed of fixing services to structural elements.
- High precision, making for good air tightness and ease of installation.
- Elements can be cut out with CNC machines using a fully digital workflow (especially with DfMA using BIM).
- Embodied CO2 is significantly lower.
- Further opportunities for circularity and sequestering carbon, as elements can be modified and reused.
As mentioned, Sweden presents a useful model of how a major shift can be brought about by the manufacturing industry and most new homes in Sweden are built using MMC. With this, much contractor-funded research and development is dedicated to MMC engineering and raising the quality and environmental performance of new homes. Therefore, it is no coincidence that Skanska, a company founded in Sweden, is cited under Contractors Perspective in the RIBA Plan of Work 2013, Designing for Manufacture and Assembly.
Of course, every European country has its own context for its approach to MMC, with factors ranging from regulations and industry traditions to climate and the cost of labour. One thing we can learn from them all, however, is that with all these factors at play, baby-steps will not be enough to roll MMC out in any significant way, at any significant pace. The common denominator, for a shift to MMC, is always the systemic process thinking and new business models.
Looking at all the factors, we can also be sure that the UK’s shift needs to be joined-up, guided by a clear vision of the overarching benefits of MMC and a genuine commitment to move to climate-positive means of construction to meet climate goals.
Lukas Thiel M Arch RIBA ARB
Partner
White London Studio
Tel: +44 (0)208 068 7347
Twitter: @whitearkitekter
LinkedIn: White Arkitekter
YouTube: White Arkitekter
Instagram: @whitearkitekter