Innovative construction techniques have become key for the construction industry to adapt to the dynamic nature of the challenges facing the sector. Dr Poologanathan, head of structural engineering at Northumbria University, discusses the increasingly vital role of Modern Methods of Construction in addressing issues such as the UK housing crisis, emergency healthcare infrastructure and the future of safe and sustainable modular construction
The construction industry all over the world is facing many challenges, including material scarcity and labour shortage (both skilled and unskilled) due to the pandemic, Brexit and the increasing demands of building standards.
Modern Methods of Construction (MMC) refers to a broad range of novel technologies that relate to construction: including prefabricated offsite elements, constructing with volumetric modular units, 3D printing, application of thin wall structures, novel connection and assembly techniques, and many more.
MMC solutions are being adopted in many different types of applications. These include residential, commercial, educational, and healthcare.
With the increased efficiency, reliability, and cost-effectiveness associated with different types of MMC, a variety of complex construction applications have become attractive in situations where traditional construction methods would yield much more design and construction time, resources and labour.
Most of the MMC construction techniques consist of cold-form steel and other metal related structures which can demand higher energy requirements and be quite susceptible to critical failure in fire accidents.
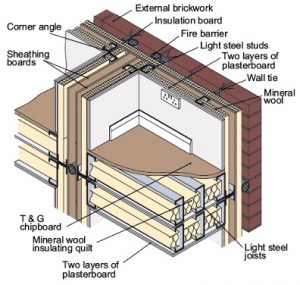
Solving the UK’s housing crisis
The UK government has recognised MMC’s potential to become a large-scale solution for meeting, for example, social housing demands and promoting growth and sustainability in the construction industry in terms of these benefits.
Modern methods of construction, also known as modular construction, allows us to rethink how we visualise, design and build much-needed housing. The design process allows for faster development, the viability of difficult sites, and the creation of a diverse and adaptable housing stock that meets the needs of local residents and communities.
Although MMC has lured the construction and housing industry for decades, less than 10% of housing in the UK is actually constructed this way – despite the ongoing housing crisis and the need to construct millions more homes in the coming years. The following figure shows the MMC percentage of new housing in a range of different countries.
Prefabricated homes were seen as a temporary response to the housing crisis in the post-war years. Many were not supposed to last more than a decade, so the fact that some are still standing after seventy years is very surprising.
To pave the way for a new generation of modular housing adoption with public acceptance, it is necessary to overcome this perception, that modular construction only provides short-term building solutions.
The root issues that are causing the housing crisis are much more complicated and political than simply seeking a faster way to develop. Modular factory-built houses, do however, solve some of the problems, such as speed of construction and addressing the skilled labour shortage.
Modular construction and Covid-19
As the Covid-19 pandemic hit at the beginning of 2020, emergency facilities such as testing and treatment centres, critical care or first-aid facilities, command centres, administration offices, wash facilities and bathrooms, distribution centres for vital services, portable training facilities, and storage for medical supplies and equipment became increasingly necessary.
The Covid-19 virus was spreading unabated, resulting in a large number of people becoming infected. As a result, health services and room requirements were, in many countries, inadequate to treat all affected patients.
This called for additional space and hospital expansions, but in a timely manner. Consequently, factory-designed, factory-manufactured, and onsite-installed modular buildings proved to be the perfect solution for healthcare systems across the globe. It demonstrated that modules and associated inventory infrastructure can be used to meet healthcare needs and can be personalised and distributed short-term on site.
Prefabrication also decreases traffic, noise, and dust in healthcare facilities, which is important when constructing or expanding infrastructure around patients with weak immune systems.
Northumbria University modular building research
The sudden surge in development of MMC in the construction industry and the interest of government and property developers in modular construction has given us (the Northumbria research team) scope to contribute to the development of novel affordable steel-framed modular units for construction with enhanced overall (healthcare, structural, fire, energy and lightweight) performance; ideally suited for emergency response situations, such as the current Covid-19 pandemic.
Our research team is currently focusing on modular units made of steel components as they are a leading choice of modular building investors due to the exceptional strength and rigidity for lightweight construction. Considering the sustainability and green building aspects of construction, future research has also been planned around hybrid construction for developing modular building units that are less resource-intensive.
Based on a thorough analysis of current modular units, experiments and numerical findings, a performance-improved steel-framed corner post modular unit has been proposed by the Northumbria University research team and is being developed as a short-to-medium-term as well as long-term solution for the construction industry.
Sustainable modular construction
Sustainability of construction could be mainly identified as two components. Firstly, the sustainability concerns at the construction stage; secondly, the sustainability aspects at the operational phase of the building.
MMC techniques like modular construction and other prefabricating options would lead to much-reduced waste generation throughout the construction process. When structural components are produced in a factory, often mass-scale manufacturing is the practice, meaning that precise amounts of material are used. The reduced waste products are then also subjected to recycling in a systematic manner.
Factory-built and mass-scale manufacturing produce optimum solutions in terms of manufacturing time of labour and energy use hence, the reduced energy consumption during the construction process is also a driving force towards sustainability.
Sustainability aspects of the operational phase of construction are related to the energy consumption of the building. In countries like the UK, the cold climate conditions cause the energy requirements of a building to increase drastically if the heat transfer rates through walls and ceilings are higher.
Since most of the modular construction practices are based on cold-form steel structures and those have very high thermal conductivity compared to other similar construction materials, appropriate use of thermal insulation and innovative designs are quite necessary.
Northumbria University is conducting a series of studies on the energy performance of modular constructions covering a broad range of parameters that will enhance the knowledge and understanding in this area.
Fire safety of modular buildings
Fire safety standards in UK are being critically reviewed and elevated recently due to the possibility of fatal accidents in the event of a fire, for example, the Grenfell tower and Moorfield hotel fire incidents in recent years. Therefore, fire safety of construction is a prime requirement now more than ever. As discussed previously, use of cold-formed steel structure in MMC and modular constructions is quite common.
However, due to degradation of structural properties of steel at elevated temperature, fire performance of these MMC and modular constructions must be carefully addressed at the design stage.
To tackle this research gap, several studies are currently being conducted at Northumbria. Some of these investigations are on existing wall, floor panel configurations, others aim to propose innovative designs that optimize structural behavior, energy demand and cost while asserting the required fire resistance level.
Research team
The Northumbria University MMC research team is led by associate professor Dr Keerthan Poologanathan and is part of the wider International Centre for Connected Construction (IC3) partnership.
IC3 is a collaboration between industry, academics and the public sector that contributes to the transformation of the built environment and the construction sector worldwide by driving productivity and performance through digital technologies and smarter working processes and applying them to the entire building and infrastructure lifecycle.
Dr Poologanathan
Head of structural engineering