Advanced Industrialised Methods for the Construction of Homes (AIMCH) is a pioneering project that puts collaboration, digital working and large-scale offsite manufacturing at the heart of tackling the housing crisis. Stewart Dalgarno, director of product development at Stewart Milne Timber Systems, explains how it works
The UK is currently experiencing a housing shortage, with government statistics stating a further 120,000 homes are needed annually. Specifically, there is a shortage in the provision of affordable homes, and the rate at which these additional homes need to be built cannot be achieved solely using traditional construction methods.
Advanced Industrialised Methods for the Construction of Homes (AIMCH) is a flagship three-year housing innovation project, which aims to combat the UK housing crisis through a collaborative effort from significant players within the housing sector. Managed by Limberger Associates, the collaboration includes Stewart Milne Group, Barratt Developments, London Quadrant Housing Trust, Tarmac, the Manufacturing Technology Centre, the Construction Scotland Innovation Centre and Forster Roofing Services.
Speed, quality and efficiency are challenges the sector faces in the fulfilment of additional housing, and so finding methods to build affordable, high-quality and low carbon efficient homes is a priority. Through digital working, offsite construction and lean site assembly, a strong sustainable, viable, integrated construction method can offer an alternative to traditional construction methods.
Offsite construction is quickly becoming a popular way to build, driven by the demand for homes, skills shortages in the building industry and environmental considerations. Offsite construction is a practical alternative to traditional building methods as it is more sustainable and significantly increases the speed at which the home’s structure can be created, reducing wastage and risk more efficiently and cost effectively.
AIMCH aims to identify and develop industrialised offsite panelised solutions to meet current and future housebuilding demands. The offsite solutions will be trialled on live housing projects across the UK, with successful methods then commercialised and brought to market on a large scale.
The goal is ultimately to help the housing sector fulfil the housing shortage through delivering the tens of thousands of additional homes the UK needs to meet current demand, while reducing cost and improving quality, compared to masonry construction methods. The aim is to achieve this by delivering cost-effective homes in volume, reliably, quicker and with minimal defects.
The £6.5m AIMCH research and development project has the potential to impact on up to 35,000 of the homes to be delivered by project partners across the UK annually. The project will gather data and hard evidence from live construction sites to provide insight, inform decision-making and aid business cases for change and investment across the industry. The project seeks to advance digitally integrated solutions in design standardisation, design for manufacture, supply chain integration, enhanced offsite panelised systems and lean construction processes.
Speed of build and de-risking the build process are essential to increase the number of new homes delivered with confidence. This can be achieved through offsite panelised construction, where there is the ability to produce large volumes of homes to exacting standards, at pace and viably. With valuable experience and expertise in all aspects of offsite panelised construction, specifically with the use of timber systems, Stewart Milne Group plays an integral role within AIMCH.
Stewart Milne Timber Systems manufactures high-quality, high-performance timber systems ready to be transported on-site and erected, wind and watertight in as little as one day. Offsite timber systems ensure robust quality and guaranteed performance standards are consistently met, during the design and manufacturing process. Adopting a low embodied carbon ‘fabric first’ approach will support the government’s planned introduction of a Future Homes Standard by 2025, delivering future proofed new build homes with low-carbon materials, heat and power and first-class levels of energy efficiency.
There is scope for reduced labour and material costs when utilising offsite panelised construction as there is less reliance on trade skills and on-site supervision during the key superstructure construction process, and the faster build of the main structures reduces management and supervision requirements, while de-risking the process. Enhanced specification standards and build quality can reduce costs related to energy use, defects and repairs, and an accelerated build time provides a faster return on capital outlay.
Offsite construction provides housebuilders with many answers to existing problems faced by the industry, but its collaboration within industry through projects like AIMCH that will be critical in bridging the housing gap. It is expected the project will deliver new valuable digital design tools, manufacturing advancements and leading offsite systems that can be adopted by others within the housing sector to improve and increase housebuilding efficiency and quality.
The project provides a promising foundation to addressing challenges faced by the sector, while demonstrating improved construction methods that deliver high-quality homes quickly and viably. In the meantime, only through continued innovation such as AIMCH and government funding into housing via schemes such as the Home Building Fund will we be able to create and sustain a long-term solution to meet housebuilding demands.
For more information, please visit: aimch
Stewart Dalgarno
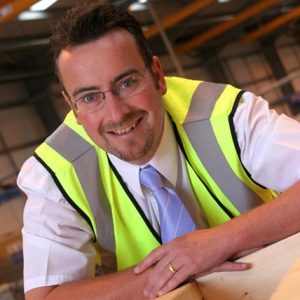
Director of Product Development
Tel: +44 (0)7788 432798
Twitter: AIMCH2
LinkedIn: aimch
*Please note: this is a commercial profile.