The market for offsite housing construction continued to grow during 2021, despite the impact of the pandemic, as confidence, capacity and quality in the sector continue to grow, according to the Offsite Construction Market Report – UK 2021-2025 from AMA Research
The Offsite Construction Market Report – UK 2021-2025 shows the market for offsite housing is estimated to have increased by 6% at manufacturers sales prices in 2020, although this is lower than the 2019 estimate of 12%. This is due to the impact of the pandemic throughout 2020, which caused a decline of around 11% due to huge disruptions, such as distribution issues and site closures at the peak of restrictions.
Many areas will be responsible for the demand in offsite housing construction. There is still an ongoing shortage of homes, especially across England. We must also look towards the continued decline in numbers of key skilled trades and professionals. On the plus side, there has been an increase in the capacity for offsite housing manufacturing, as well as the number of systems with quality assurance.
Timber panels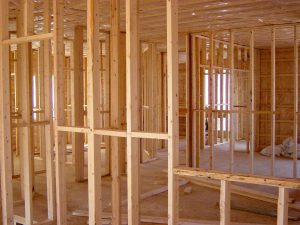
Open panel timber frame still maintains its majority share in the offsite housing construction market. These types of building systems still require a considerable amount of onsite work to complete the build. There is steady growth in demand for volumetric and closed panel building systems, particularly as there are now several large factories that have started operation in recent times that can deliver at scale. The larger of these new factories have the production capacity to deliver 2,000+ units per year.
While softwood timber and light steel frame are well established materials used in offsite house construction, the volume of completions delivered using cross-laminated timber panels (crosslam or CLT) and glue-laminated (glulam) beams had been low level, due to both lack of large-scale production and lack of accreditation.
Steel framed panellised systems are an area which is forecast to see growth over the longer term. This will not only cover new build developments but also refurbishments. Many companies within this area are modular building manufacturers with the capability to offer complete housing systems, as opposed to panel products that are mainly used for components only.
Offsite quality
Typically, the UK construction industry has been reticent to use offsite building technologies due to the poor reputation given to 1950s prefabricated housing. This has historically been considered the main reason for why many lenders will not offer mortgages on homes where offsite building systems were used. However, the overall quality of offsite building systems has improved considerably in recent years.
Availability of quality assurance and warranties for offsite housing systems are key to growth. The broad lack of these has, up to this point, been a barrier. There has been an increase recently in the number of firms and proprietary offsite housing systems that are obtaining BOPAS certification and/or NHBC, or other provider warranties. BOPAS provides an assessment of rigorous durability, maintenance and process accreditation and having BOPAS accreditation confers confidence on main lenders like NatWest, Barclays, Lloyds, Nationwide and Santander in offering mortgages for offsite built homes.
Confidence in the quality and durability of offsite housing has been further reinforced by the government agreeing to create a minimum standard for modern homes in the UK in late 2020. The new standards will apply to all homes built using modern methods of construction, including offsite homes construction and modular homes. Several industry bodies have signed the memorandum of understanding (MoU), including warranty providers NHBC, BLP Insurance and MD Warranty Inspection Services (MDWIS). The MoU is expected to generate more confidence among potential customers, lenders and insurers as to the quality and durability of these homes.
Government funding
Until recently, there has been limited government fiscal incentives to assist with certification. This lack of support may hinder companies’ abilities to grow and expand into this area of the market. Over the short term, key to increasing the roll-out of offsite housing is Homes England’s Strategic Plan 2018-19 to 2022-23. With a budget of £27bn, key programmes include the £4.5bn Home Building Fund: available to SME developers that cannot obtain private finance, to turnkey manufacturers of offsite housing systems (as these also act as developers/main contractors) and self-builders. There is also the £1bn Housing Delivery Fund, in partnership with Barclays, to make credit more easily available to SME builders.
Alex Blagden, senior market research analyst at AMA Research and editor of the Offsite Housing Report, said: “Offsite construction is key to accelerating the development of affordable homes, both social housing and build-for-sale properties.
“Many factors are driving up both demand and supply, among the most important being the urgent need to increase affordable housing supply; a chronic shortage of skilled ‘wet’ trades; strong growth in offsite housing manufacturing capacity and an increase in the number of firms and proprietary offsite housing systems obtaining BOPAS (Buildoffsite Property Assurance Scheme) certification and/or NHBC or other providers’ warranties.
“Confidence among prospective buyers and mortgage lenders will be reinforced though a Memorandum of Understanding that was signed by warranty providers in August 2020 to develop a set of standards for assessing homes built offsite.”
Lesley-May Baker
Marketing executive
Tel: +44 (0) 1242 235724
Lesley-MayBaker@amaresearch.co.uk