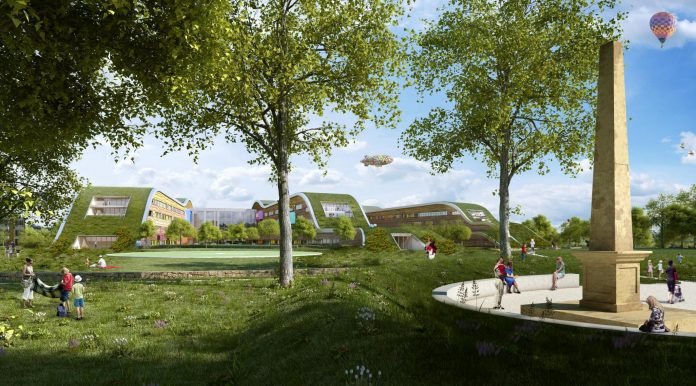
Though not a new idea, recent government reports and the housing shortage have brought renewed interest in offsite as an alternative to traditional building methods and consultancy WSP is already seeing the increased use of offsite manufacturing in their design requirements
Offsite modular construction is the process of planning and designing buildings for manufacture and construction in separate parts or modules, within a factory setting rather than a traditional construction site which are then transported and assembled on location.
Why go offsite?
“While there are challenges, the benefits include increased productivity, speed, quality, sustainability and cost predictability – and reduced health and safety risks, as construction in a factory involves less physical labour,” explains Jane Richards, Director of Structures at WSP.
Getting it right
WSP explains that early conversations at the starting process of projects are essential as these early decisions to implement offsite solutions will reap the greatest value. Projects can then be assessed and designed for any challenges in delivery from advising on what will work in the space and any operational constraints, to navigating issues around transporting buildings or components to site.
There are some common preconceptions that assembly-line homes are boring and need a rethink but Jane explains that with digital automation current modular design can be very flexible with an emphasis on quality.
Offsite off ground
There are a number of different areas where offsite is seeing significant growth with one of these being in the aviation sector.
WSP is currently working on the only piece of large-scale offsite happening in UK aviation at Gatwick’s Pier 6.
“Offsite construction has always been important in aviation,” explains Tim Morrison, Director of aviation at WSP. “It’s a safer, neater, more sustainable way of moving large buildings into location. The faster delivery means we can keep the airport facilities live until the last minute and keeping disruption to passengers to a minimum.
“For Pier Six we tabled the idea of a 200m-long building which could be broken into four modular elements (weighing in at an impressive 5,600 tonnes each) and moved into position overnight.”
WSP has also been involved in the design of futuristic Tetra Hotel which would contain 19-metre high pods that will be pre-fabricated and assembled on-site at remote locations for speed of delivery.