Simon Horn discusses why offsite construction utilising timber frame as the external wall fabric and overall structural solution is key to meeting sustainability targets
UK-wide demand for new homes continues to rise amid major government targets that underline a heightened need for greater efficiency and sustainability to be achieved.
With England alone needing up to 345,000 new homes annually, it’s clear that fresh, innovative solutions that disrupt the market are required to bridge that significant gap.
While the total housing stock in England increased by around 241,000 homes in 2018-19, that figure was still some way short of the estimated need, and housing minister Robert Jenrick’s pledge to “get Britain building” has so far failed to translate into firm action.
Nevertheless, the government recently unveiled plans to revamp the planning system in a document entitled Planning for the Future, with Jenrick calling it an opportunity to “think boldly and creatively about the planning system to make it fit for the future”.
Those changes should make it easier for developers to demolish vacant buildings, or old disused garages-on-block, and build new homes in their place.
With demand showing no sign of slowing, the key challenge for the industry is how it can achieve the required volume in a cost-effective and sustainable manner, while maintaining quality and profitability.
Many solutions have been offered but offsite construction represents a strong fit for a multifaceted situation, bringing a wide spectrum of benefits to housebuilders, from accelerating the construction process to reducing costs, increasing sustainability and reducing health and safety issues.
While the industrialisation of housebuilding that offsite construction presents is a significant opportunity to drive greater affordability, which can be passed on to the house buyer, we still need to see a dedicated move away from masonry construction to a greater embracing of timber frame buildings and prefabricated modular homes.
The potential for both of these Modern Methods of Construction is vast.
Benefits of timber frame and modular homes
Many believe offsite construction will overtake traditional onsite methods due to sustainability factors – with panellised and modular homes being made from recyclable materials and using up to 67% less energy in the building process than equivalent traditional onsite builds.
Meanwhile, timber frame allows for greater flexibility in design and, as a sustainable material, is cost-effective, together with aiding the effort to reduce construction’s carbon footprint.
Built offsite in a factory, with fittings included, modular homes can be installed on site significantly faster than other methods of housing construction. As such, both modular homes and timber frame homes work very well alongside each other, complementing offsite manufacturing.
Furthermore, on larger proposed developments, there is likely to be an improved benefit for the construction phase planning, providing better delivery of housing at scale and therefore delivering competitive pricing.
Offsite construction
Offsite construction offers a tried and tested method of building homes with higher quality and which comply with a variety of performance standards. It also reduces the amount of additional labour on site and simultaneously heightens both cost-effectiveness and delivery capacity.
In essence, offsite construction can significantly reduce both labour and material costs, with less reliance on trade skills and multiple suppliers. Shorter build of the main structures will also reduce the management required to supervise and coordinate the on-site contractors, improving working efficiency. The more rigid design constraints of modular housing can be restrictive at times, compared with those of panellised timber frame homes, which can often allow a greater amount of design flexibility.
While neither modular nor panellised timber frame housing alone will be completely suitable for every site or building design, ie height restrictions in timber frame or site constraints for modular homes, a combination of both does have advantages in driving building efficiency and quality.
Using a sustainable material, as timber is, also provides the ability to drive down carbon emissions and move to a lower carbon industry. The offsite construction of timber frame provides the building with a superior thermal envelope that will require minimal maintenance and enable a fit-and-forget solution for the lifetime of the building.
Building performance is improved with better heat retention and subsequently reduced energy demand, resulting in a fuel-efficient dwelling.
Financially, the accelerated build time of offsite construction delivers as well, providing a quicker return on capital outlay, and lower site preliminaries expenditure, by up to 30%.
In practice 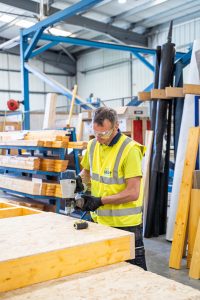
Across the UK, we have the capacity to produce around 10,000 timber frame homes per year. That ability to manufacture offsite means we can build 10 typical blocks of two-storey housing in terraces of three or four units, five weeks earlier than if building with masonry, or other on-site solutions. A further example of construction time benefit would be a typical four-bedroom detached home, which could be erected, wind protected and made watertight in as little as five days.
With major housing targets continuously on the rise, such innovation must be considered a vital solution, particularly as it contributes to a more efficient, sustainable, high-quality and cost-effective housing sector.
With that in mind, we invest significantly in research and development: we have a Centre of Excellence at our Witney automated facility and we partner with various housebuilders and constructors to develop new products to bring to market that, in turn, will deliver better homes for the future.
When housebuilders engage with us to develop timber frame solutions for their projects, we consider it essential to get involved from the earliest stages, enabling us to value engineer the designs; work with client construction teams to improve build programmes; generally deliver project efficiencies; and ultimately reduce costs.
One of our most successful product innovations is our award-winning Sigma II Build System – a closed panel system that is BBA-certified, able to be built to six storeys structurally and delivers performance standards to BREAAM Excellent. The Sigma II Build System has also just received the Housebuilder HBF 2020 Product Award in recognition of performance and quality.
Fundamentally, Stewart Milne Timber Systems offers a tried and tested way of building, using timber frame components manufactured in factory-controlled environments – similar to modular homes providers, but with greater flexibility and no constraints on capacity.
Offsite manufacture also supports housebuilders at a time when the skills shortage threatens growth and material cost increases in some areas puts pressure on profits. Stewart Milne Timber Systems has a long-term sustainable material supply through direct partnerships with the timber producers, as well as strong partnerships throughout our supply chain. Add to this the on-site efficiency offsite brings, it is the solution to the housing demand.
Homeowners will also want a property that meets their needs at varying life stages – so that means one that will last and requires low maintenance, at the same time as being able to be easily adapted if required in future years. Timber frame does just that.
Using timber frame construction, a home can be designed as one integrated system with a fabric first approach and energy efficiency locked into the home’s core; reducing the need for other micro-renewables or wider newer technologies to be added later. Ultimately, this will save the homeowners money and gives them peace of mind in delivery of energy performance.
Amid wide industry demand for increased production, it is critical that low carbon sustainability remains at the forefront of developers’ minds – and by placing a greater onus on the building fabric, together with ensuring careful selection of construction method, sustainability targets can be met.
Taking a fabric first approach and applying offsite construction methods is a proven vehicle for ensuring that sustainability compliance is part of the building process – from the materials, to construction and the remainder of its lifecycle.
Why timber?
On average, timber frame homes can be built in lower timescales than traditional masonry construction methods, while the material’s renewable low carbon credentials are much stronger. It is also readily available and economically viable.
For every tree used in the construction of a timber frame home, more are planted. Masonry construction with bricks and blocks is certainly not as viable for a low-carbon future, being more time-intensive and non-renewable.
Timber frame homes have a track record of superior energy efficiency and low embodied carbon. The homes are naturally warm in winter and yet still cool in summer, allowing residents to enjoy significantly lower heating bills overall.
Ultimately, offsite timber frame construction can provide housebuilders with many of the answers – but it is true collaboration within the industry that will be crucial in helping solve the climate crisis.
However, with so many positive elements to this timely transition, the UK can lead the way in an exciting new offsite industry – and it is an opportunity that must be fully embraced.
Simon Horn
Technical manager – England & Wales
Stewart Milne Timber Systems
+44 (0)845 009 2774
www.stewartmilnetimbersystems.com