Raymond Millar, construction director at The McAvoy Group, looks at how Dublin Airport used offsite construction and the latest digital technology to expand its passenger boarding facilities and achieve one of the fastest projects ever completed at the airport
Dublin Airport is one of the fastest-growing airports in Europe. South Gates is its new €22m, 2,200m2 passenger boarding facility, which has been developed to meet the huge growth in passenger numbers. The building provides seven boarding gates to serve nine aircraft stands and can accommodate around 1,000 passengers at a time and up to 8,000 people a day.
The offsite construction solution
The dedicated passenger boarding zone was constructed offsite by The McAvoy Group to reduce the programme for earlier occupation in order to meet the rising demand for flights from the airport. The new facility was manufactured at the group’s offsite production centre and was craned into position in just 16 days as 77 steel-framed modules, up to 12m long and weighing up to 13 tonnes each.
The use of an offsite solution allowed the airport operations to continue uninterrupted, with the minimum disruption. It also allowed the fast-track programme for the project to be achieved.
Dublin Airport project challenges
McAvoy had to address a number of challenges on this project:
Programme
The building had to be delivered to a critical and short programme to accommodate additional flights. It was operational within a 16-month planning, design and construction schedule.
A highly constrained site
The space for the new facility was restricted within the South Apron and the fully operational airport site.
Full integration of airport M&E services
All mechanical and electrical services – including data communications, fire and security – had to link into the existing live airport terminal systems, which was a hugely complex operation.
Open plan environment
Clear uninterrupted spans of over 19m were required for the 120m-long facility. This was achieved by engineering the building modules to incorporate hot rolled structural steel beams, which removed the requirement for internal columns – a modular industry first.
Stringent fire safety standards
The scheme had to be designed to meet stringent fire safety regulations that exceeded Building Regulations.
Enhanced acoustic specification
A specially designed ceiling solution was developed using suspended panels in different shapes and orientations.
This provides a high standard of acoustics and a strong visual feature, as well as a sense of space.
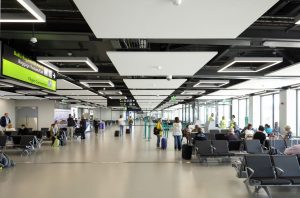
Digitising offsite construction
BIM was used extensively in the tender and design stages. McAvoy created a virtual reality model of the building to demonstrate the design and offer a fully immersive VR experience. This allowed the client team to review the internal environment and in particular, the innovative acoustic ceiling solution.
Virtual reality fly-throughs at the earliest stages of the project facilitated client engagement and informed key design decisions.
At the detailed design stage, the client was able to make real-time changes to the internal layout. The use of analysis tools also allowed McAvoy to simulate building construction processes, including the complex module delivery process on a highly restricted airport site.
All the principles of BIM were used for the project. 3D drawings and models were produced for both the steel structure and architectural modelling, and a common data environment was created. BIM was also beneficial for clash detection for the installation of complex M&E services.
A range of simulation tools were used to validate the performance of the proposed building against international airport standards while meeting the functional requirements of the client, Dublin Airport Authority. A facility was developed that would provide a safe, comfortable passenger environment with the appropriate levels of service, amenities and passenger information.
The customer perspective
Iain Heath, project manager at Dublin Airport, said: “This is one of the fastest projects we have ever completed at the airport – from planning to the first flight in just 18 months. The finished building speaks for itself. It is a handsome new facility with high quality finishes and clean architectural lines.
“We were working to a very constrained programme to have the building operational ahead of the busy summer season. The project and its innovative use of offsite construction is a fantastic achievement for the whole team.
“We were impressed with how McAvoy used BIM and virtual reality. As an airport, we have a complex approvals process but the digital techniques allowed the senior management team to ‘walk through’ the building and to experience the facility, which facilitated design sign-off. In addition to the programme benefits, offsite construction also meant fewer trades working on site and a smaller site footprint. This approach had far less operational impact for the airport and the closure of fewer aircraft stands with reduced timeframes.”
Brian Looney, contracts manager at Flynn Management & Contractors, added: “The principal driver for offsite construction was to reduce the programme. The McAvoy solution allowed the building to be delivered to site within weeks of planning approval.
Having fewer trades on site is also a benefit for airport projects, where sites are very constrained and the highest standards of security have to be maintained at all times.
“This project has pushed the boundaries of offsite construction to create a valuable infrastructure facility. The quality of the finished building is excellent, and you would never know this is a modular building. The McAvoy Group’s production facilities are impressive, and their systems are robust. We would welcome the opportunity to work with their team again.”
Raymond Millar
Construction Director
Tel: +44 (0)28 8774 0372
Twitter: mcavoygroup
YouTube: The McAvoy Group
LinkedIn: McAvoy Group
Facebook: McAvoy Group