The UK construction industry has been set a steep challenge by the incumbent government of building 300,000 homes a year by 2022
Against the backdrop of a UK housing crisis where the industry is struggling to house future generations, failing to reach this target is simply not an option. There is no silver bullet and a solution can only be found if the industry innovates, not least in the fundamental areas of construction.
Kim Vernau, CEO at BLP Insurance, highlights the key points raised at an interactive discussion organised for industry peers. This focused on the role of precision-engineered factory manufactured homes, delivered on a large scale, in disrupting the UK housing industry. Guest speaker, Rosie Toogood, chief executive of Legal & General Modular Homes, provided a wake-up call that without disruption the future of housing construction will not be able to progress.
Introduction
The case for change in the housing sector is clear. Looking back over a number of years, it’s only on very rare occasions that there has been such a stark gap between supply and demand in an industry which has failed to resolve itself over time. Furthermore, this gap of around 100,000 homes exists in an environment where the workforce is expected to decrease by 20% to 25% over the next 10 years. It’s a crisis that’s only going to get worse.
Against this backdrop, it’s clear that there are challenges getting onto the housing ladder, and there is a struggle for those who are unable to rightsize or relocate due to the absence of suitable accommodation.
L&G’s role in the UK housing market
Legal & General has been involved in supply-side housing activities for nearly 20 years, investing for the long-term to deliver both societal and economic benefit.
Legal & General is investing into a number of different infrastructure projects, bringing housing back to the UK’s cities through large scale regeneration, including the Media City in Manchester, Thorpe Park in Leeds, Science Central in Newcastle and Bracknell town centre.
Legal & General’s multi-tenure housing investment strategy is providing housing solutions for all stages of life, aiming to deliver 6,000 Build to Rent units by 2019, a later living property portfolio of 3,500, three new communities through its housebuilding arm, Legal & General Homes, with a pipeline of almost 3,000 properties. It is also revolutionising the construction industry through its Leeds modular housing factory.
This holistic approach provides Legal & General with the mechanisms to deliver high-quality returns throughout market cycles by pivoting investment to where the need is greatest.
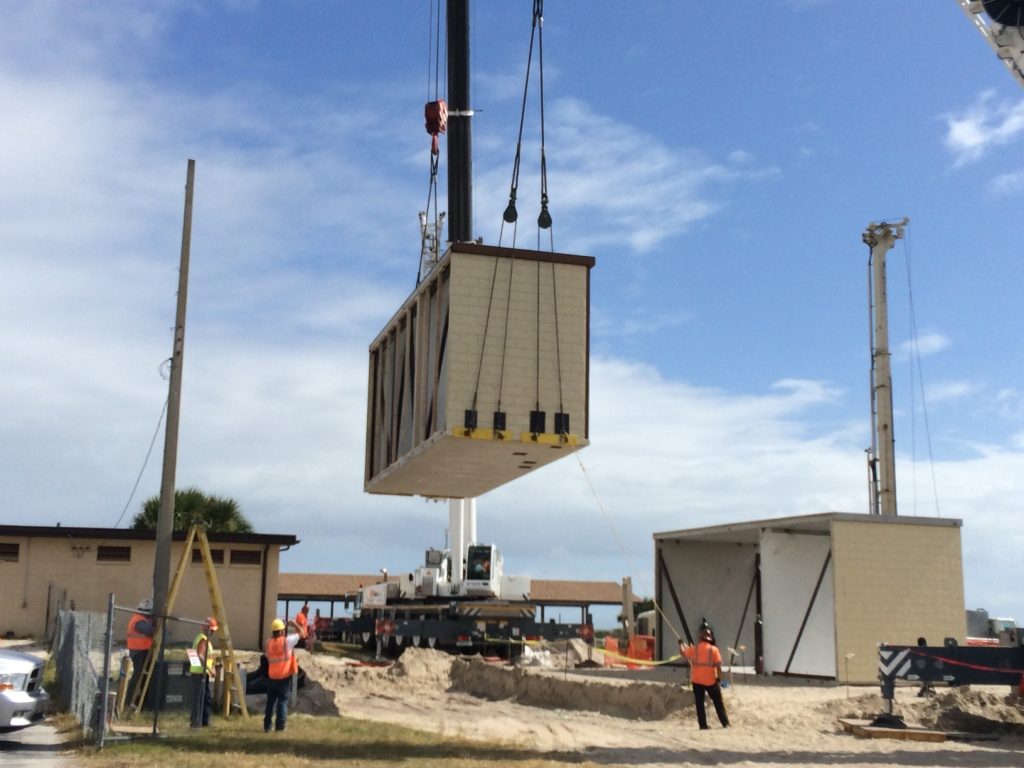
Calling for industry disruption
Overcoming the UK’s housing shortage will not be resolved by simply doing more of the same and investing in more of the same, but by disrupting the industry through a different mind-set. The challenge lies in bringing new methods of construction to the industry and, when at capacity, Legal & General Modular Homes will be producing 3,000 factory made homes a year.
Legal & General are working closely with a number of local enterprise partnerships, local councils, and housing associations in the social and affordable market to help to understand the customers’ requirements and align the product development programme accordingly. When it comes to the next step of actually designing these products, Legal & General are once again taking a different approach; adopting digital platforms and digital tools and working collaboratively with design consultants.
This approach creates a better understanding of the impact of design for manufacture, including how the product is assembled, and how it can be produced on a consistent and repeatable basis on the assembly line. This isn’t an easy journey, and requires collaboration between the design team, the manufacturing team and supply chain team to work through any issues as well as continuous improvement. But if you get it right, there is a real opportunity to enhance product quality through standardised and simplified techniques that can be replicated at scale.
Collaboration is key
Legal & General can’t change the industry on its own. There needs to be collaboration with an ecosystem of customers and clients who understand both the benefits of modular construction as well as the design requirements, and begin to accommodate this in their specifications.
The industry needs to get to the point where it can standardise the product, and drive quality and value, while also providing an element of choice and customisation. This is a structural issue and needs to be tackled by the industry together.
Supply chain innovation is required to bring new ideas and concepts needed to move the industry forward.
The industry needs to move away from one-off contracts, spot relationships, and aggressive commercial behaviour, and towards long-term supplier relationships and an environment which encourages R&D funding and therefore innovation. This will really only come from more collaboration at the primary level in the industry.
Enhancing the industry reputation
It’s important that the industry has standards that are recognised, accepted and adhered to so that customers can be assured in terms of the quality of product they are getting. There is a vast range of accrediting bodies within the construction sector, and the industry would benefit from a level of consolidation in raising standards across the board to ensure product quality.
Negative media headlines on the traditional construction industry have impacted the public’s perception of the sector as a whole. If the industry has a bad reputation and customers come to expect poor quality from the outset, then we will not be successful in this environment.
All industry participants have a responsibility to take this on board to drive up standards, starting with individual performance and also leaning on the rest of the ecosystem to move it forward.
Conclusion
While the sector is still in its infancy, pockets of developments and innovative designs are starting to come to fruition and momentum is building in government and local councils to make modular construction successful. There is a significant opportunity to grasp, but it will only be a success if the industry can work together and put aside the traditional adversarial relationships.
This won’t happen overnight, but ultimately we need to move to a more collaborative approach which is longterm and provides an environment that encourages businesses to invest confidently in R&D to deliver innovation, and invest in developing skills to advance the industry as a whole.