Lewis Taylor of TRADA discusses the evolution of offsite timber frame construction into a fully modern method of delivering high quality, cost-effective and sustainable buildings
Although timber construction is often referred to as a Modern Method of Construction and there is much industry buzz around modular and offsite construction, the timber frame industry has been thriving in the UK for over 50 years, with a much longer history of importing panelised or modular timber frame buildings from North America and Canada.
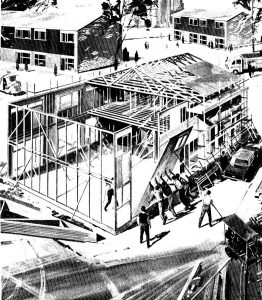
Looking back through the TRADA archives finds a plethora of information on timber frame construction dating back to the 1960s, with TRADA’s Timber Frame Housing Design Guide first being published in 1968 – the foreword of which discusses many of the same issues which we are facing in today’s housing market: “If the National Plan target of 500,000 dwellings a year by 1970 is to be achieved, a substantial number of them will have to be built by non-traditional methods.”
Looking at today and forward to tomorrow, we are still facing similar challenges to build housing quickly, efficiently and to a high standard; and still one of the most attractive ways of achieving that is through the use of prefabricated, panelised timber construction. Timber frame construction has now been a mainstay of the UK construction industry for decades; however, the increasing popularity of timber, offsite construction, Modern Methods of Construction and sustainable buildings has seen its market share swell over the last 10 years to approximately 27% in the UK (based on Structural Timber Association market share data).
Recent data published by the Structural Timber Association showing the potential cost saving (2% to 3%) and time savings (up to 30%) when constructing houses using timber frame offsite construction methods when compared to masonry helps to show why offsite timber construction market share has been steadily growing.
While timber frame construction itself is not a new concept, modern engineered wood products and systems have helped innovation and growth in timber construction. Engineered timber composite floor joists such as timber I beams and metal web joists, LVL and glulam have helped timber floors span larger distances and these products’ improved dimensional stability have helped reduce problems associated with shrinkage and squeaky floors.
Glulam beams are not just limited to use in flooring. We have seen great advances in the use of large-section glue-laminated timber post and beam frames, which are now commonly being used for schools, sports halls, education buildings and retail buildings.
The benefits of glulam versus solid timber are many but they include being able to use smaller, kiln-dried sections of timber bonded together to form the larger posts and beams. This enables the use of smaller trees and results in finished beams manufactured close to their in-service moisture content, all but eliminating shrinkage and movement typically associated with large-section solid timber.
Perhaps the most notable recent development in engineered timber construction systems is cross-laminated timber (CLT). Large solid wood panels formed in a similar way to glulam beams, but with laminations in two (cross) directions rather than one, are now being used as floor, wall and roof elements in residential, office, education and commercial buildings.
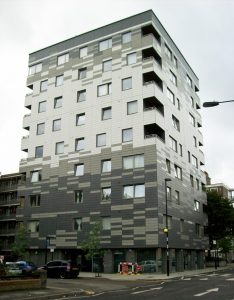
Buildings constructed using CLT have seen the envelope being pushed on what was traditionally thought possible in timber – the tallest, the largest, the longest etc. Notable CLT milestones include Murray Grove in Hackney which was, for a time, the tallest residential timber building in the world (although now 10 years old) at nine storeys tall. This has since been surpassed by other buildings in the UK and across the world. Other notable buildings include the Believe in Better building in London, which was the UK’s first four-storey commercial office building constructed using timber.
With softwood platform timber frame construction, there has been a notable trend over the last five years to bring more aspects of construction offsite.
An example of this is the move to factory fitting thermal insulation products, where quality control is generally far better than can be achieved on site.
Along with this, many timber frame manufacturers now also factory fit vapour control layers and service void battens to external walls, enabling follow-on trades on site to quickly and easily install services, while maintaining the thermal and air tightness performance of the building envelope. Most timber frame manufacturers now prefabricate large section floor cassettes (rather than stick building floors on site) helping to further improve the speed of construction.
The timber frame industry has benefited from the demand for increased performance in air tightness and lower U values, which has been easily accommodated without substantial changes. The use of reflective membranes, more efficient insulation materials and continuous air barriers have helped deliver this.
While innovation in products and design help the industry meet the demands of the 21st century, it is important not to lose sight of the basic principles of good construction, both in terms of design and construction. It is also important to keep quality at the forefront, when speed may seem like the dominant factor.
As much as innovation can result in new ideas and methods of working, the lack of skilled labour and the need for ease of construction on site should not be overlooked. Modern timber frames are an established and conventional method of construction in the UK. The current methods of working have evolved over decades, resulting in an excellent balance between the benefits of prefabrication and the benefits of completing work on site – for example, where higher levels of prefabrication are carried out in the factory, we have learned that it is very important to protect panels from exposure to rainwater during the construction phase.
In summary, both innovation and evolution in timber offsite construction in all its forms has resulted in high quality, cost effective, environmentally responsible and aesthetically desirable buildings, which are fast and easy to construct. Timber offsite construction market share is improving year-on-year and homeowners are actively and enthusiastically choosing them. Perhaps the future imagined in the early TRADA timber frame articles, promotional and technical documents is at last here – now we need to share the success story of prefabricated timber buildings.
Lewis Taylor
Timber Frame Consultant
TRADA
Tel: +44 (0)1494 569603
Twitter: @TRADA_
LinkedIn: Trada