After 20 years of stagnation, what will it take to kick-start productivity in construction? Martin Feakes, head of buildings London at Ramboll, believes the conditions are right for change
While there is much speculation about the impact Brexit may have on the UK economy, one unexpected effect may be the much-needed impetus to drive changes that will finally address the biggest issue facing the construction industry: improving productivity.
We see the effects of this across construction, with the inability to deliver housing being the most obvious. We haven’t built enough houses for years. While other industries, such as automotive manufacturing, have developed in response to foreign competition, construction hasn’t had the same external forces and, therefore, the drivers to follow suit. The result is stagnating productivity for over 20 years.
It seems that the cyclical nature of the UK construction industry prevents impetus for longstanding structural change. In good times, it just wants to get on and get things done – with no time for wholesale innovation that diverts resource away from the ‘boom’.
Conversely, economic downturns hit our industry particularly hard and during these times, there is little appetite for investment in new technology or ways of working.
Parts of the industry are innovating but there needs to be a concerted effort if we are going to make sustainable changes to the way we design, procure and construct our buildings and infrastructure. This was recognised in the 2016 Farmer review, in which the industry was challenged to “modernise or die” and, it seems, this has been heard by to by both government and the private sector.
A unique shock to the market such as Brexit, on top of an already chronic lack of labour, may create the conditions needed to deliver lasting change in the construction industry.
While productivity solutions are often spoken about in isolation, the way to accelerate and realise their potential is surely to pursue them in a more holistic way. How much progress could be made through a coordinated effort involving attracting new talent, digital design and offsite construction?
In fact, the three are intrinsically linked. The UK is recognised for world-class design and construction and we need to enthuse and engage young people about what we do and the opportunities for them in construction.
At the same time, if we can evidence the use and desire to use more cutting-edge digital technology, we can start to compete with the tech giants for leading talent. Greater focus on creating a more inclusive and diverse industry will help improve our image, while more offsite manufacture will improve safety and working conditions, which are again negative preconceptions of the industry and put people off making a career in it.
Years after the first wave of modular building in the UK, the industry now seems poised to embrace a different way of constructing. We have seen a wave of high-profile papers and initiatives that respond to the challenges set out in the Farmer review. These range from the London Assembly’s Offsite Manufacture to Solve the Housing Crisis to Heathrow Airport’s call for offsite logistics hubs to deliver its expansion programme.
However, the offsite industry is fragmented. A myriad of systems compete to be selected with an assertion that selection should occur even before planning approval.
Government is now proposing that for major departments, there will be a presumption that projects are designed and procured in a way that promotes a standard kit of parts and the use of offsite solutions.
If this seems far-fetched, we only have to look to Scandinavia, where they have worked this way for 60 years, constructing 80-90% of components offsite to deliver a rate of housebuilding we can only dream of.
While the benefits of offsite construction are well known, it takes longer to design and will cost more unless we develop components that suppliers want to build. The answer to this must be digital design.
The modern workforce now has digital skills that even a few years ago we could only dream of. Why risk losing talent to a tech firm if we can entice them into our industry?
For years, architects and engineers have delivered code-based design; this means that much of what we do is ripe for future coders to revolutionise the industry. The burgeoning digital categories at awards ceremonies show that the industry is advancing rapidly.
We can now prove that the ‘heavy lifting’ in design can be streamlined by using digital tools, saving huge amounts of time. Far from being nervous about dumbing down their product, this surely offers designers a golden opportunity to put more time into the bespoke elements of a project and to deliver higher quality, more predictable solutions.
After over 20 years of stagnation, the conditions may now be falling into place to deliver the change needed to solve the construction industry’s productivity problem.
Martin Feakes
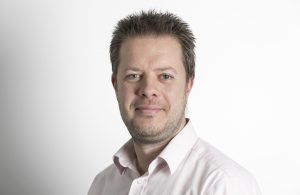
Head of Buildings London
Tel: +44 7436 588 570