Alex Lubbock, head of digital construction at the Infrastructure & Projects Authority, discusses how Modern Methods of Construction can reshape the sector to deliver higher productivity, quality and performance
Modern Methods of Construction (MMC), as a term, has a history in the construction sector that long precedes its recent revival as a catch-all label for the different types of manufacturing processes and digital construction methodologies.
MMC is at the start of a new journey to becoming synonymous with Value for Money. It may not be called Modern Methods of Construction, offsite, SMART construction, modular or any of these terms in the future but the goals are clear: higher productivity with a higher quality performance and outcome over the life of the assets we construct. Why will this work now? Primarily I believe this is related to people and culture.
From a people perspective, in 2015 HM Treasury published the National Infrastructure Plan for Skills, which recognised a requirement to recruit and train approximately 100,000 additional workers. It also identified that 250,000 of the existing workforce needed retraining or upskilling to meet the type of work required within the pipeline. The National Infrastructure and Construction Pipeline 2018 has increased to a projected £600bn over the next decade. Therefore, one could assume that the shortfall in skills and the need for re-training has increased in that period.
Using Modern Methods of Construction provides a significant opportunity to reshape the peaks and troughs of demand for labour and establish a sustainable, skilled workforce that is not limited by location or the type of construction. This could also assist in managing overheated areas of the country where labour is in high demand, which can be a contributory factor to increased risk, cost, time and lower quality.
From a cultural perspective, this is far harder to quantify. Digital has become synonymous with productivity within all walks of life, including construction, where it was catalysed by the UK Government Construction Strategy mandate for Building Information Modelling Level 2, which has led to an explosion in digital technologies in the sector.
At the heart of this race for digital is consumer behaviour. Ever since the iPod and the iPlayer, we have been moving towards an experience-based and on-demand culture. A mass-customised but tailored middle ground that provides value for money for consumers at multiple levels.
So how do we move from a goods-based, transactional sector to a service and experience-based part of the economy? Recently, the Infrastructure & Projects Authority (IPA), in partnership with the Department for Business, Energy & Industrial Strategy (BEIS), released a call for evidence on a new approach to building, Platform Design for Manufacture and Assembly. How should government create its own digital Lego set for what it constructs and achieve the same level of mass customisation in what it builds?
In December 2017, the IPA launched the Modern Methods of Construction working group across central government to support departments meet a presumption in favour of offsite. To date, we have explored the barriers and are putting in place the mechanics for addressing the technical, commercial and cultural challenges ahead.
This call for evidence is a result of this working group and previous work delivered through our Transforming Infrastructure Performance programme to enable departments to aggregate demand, leverage government’s buying power and bring consistency to departmental digital and manufactured approaches to buildings. Please contribute to the Call for Evidence and influence the direction of our proposal.
Underpinning the work, we plan to do in the future is a need to increase the client’s capability. Part of that upskilling is deskilling the process of engaging with the sector to achieve its desired outcomes. Enabling stakeholders to determine what is value for money for them without limiting their ambition. To do this, we need to reduce the choice available for a small number of aspects and allow innovation and continuous improvement to thrive.
An example of this is in buying a kitchen; the standard depth and height of the worktop is the same; therefore, the manufacturers of components such as a dishwasher know exactly what space constraints they have to work with. This allows the consumer to benchmark its procurement of the dishwasher based on value.
They may still choose the lowest capital cost but properties such as energy performance rating, decibel level and whether you can work it from your mobile phone all become viable considerations through the data provided by the manufacturers and compared side-by-side on a platform like AO.com or Amazon. Why can’t we buy construction in this mass, customisable and transparent way that we are so used to as consumers in other walks of life?
With the recent establishment of the Core Innovation Hub and Active Buildings Centre through the Industrial Strategy Challenge Fund, we are focused on creating the environment for change and transformation in the sector.
The IPA will continue to convene the departments that are committed to a presumption in favour of manufacturing offsite construction, and work with industry and academia to transform infrastructure performance over the next decade.
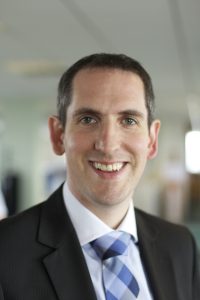
Alex Lubbock
Head of Digital Construction
Infrastructure & Projects Authority
Tel: +44 (0)20 7276 1234
GOV: infrastructure-and-projects-authority
Twitter: ipagov
LinkedIn: ipa1