An HS2 tower crane is trialling technology developed for Formula 1 (F1) to significantly cut fuel consumption, carbon emissions and improve air quality at one of its London construction sites
An HS2 tower crane on the station’s Euston approaches site is being powered by a 200kVA diesel generator – less than half the size of its usual 500kVA diesel generator to lift loads of up to 24 tonnes.
The generator’s power difference is bridged by pairing it with an energy-storing flywheel system developed and supplied by Silverstone-based engineering specialist PUNCH Flybrid.
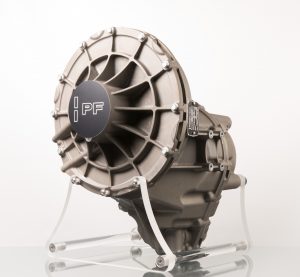
Incorporated inside the PUNCH Flybrid-supplied unit, the flywheel, measuring just 35cm in diameter, is housed in a vacuum chamber to all but eliminate energy-sapping resistance that would result from contact with the air.
PUNCH’s Flybrid’s flywheel matches the power of larger generators by using the 200kVA generator’s surplus power during the crane’s low load periods to charge the spinning flywheel to very high speeds, equivalent to a ground speed of 550mph. The kinetic energy stored by the flywheel can then be quickly released to support the generator when the crane demands maximum power to lift heavy loads.
It is able to perform up to 10 million charging cycles compared to 3,000 of a typical electric vehicle battery.
How is the science, developed for F1 is being applied to HS2?
Tobias Knichel, PUNCH Flybrid MD, explained:
“In motor racing, a teams’ quest for higher performance spurs the search for greater efficiency – essentially doing more with less. Racing cars typically accelerate and brake around 500 times during a 90 minute F1 grand prix. Each time the car brakes into a corner at high power our flywheel system spins up, storing energy which is then released quickly to boost acceleration performance as the car leaves a bend.
“We developed our flywheel technology to improve performance and efficiency at the very pinnacle of the automotive industry, but its fundamentals mean there are opportunities to deploy its benefits in other sectors. That’s why we’re very pleased to have an opportunity to utilise the technology for the construction industry under HS2’s Innovation programme.”
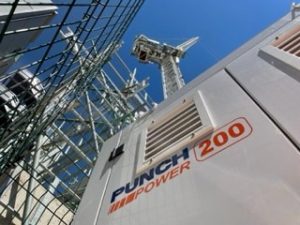
HS2 innovation manager, Rob Cairns said: “Delivering Britain’s zero carbon, high speed rail network for the 21st century is a national endeavour that is drawing on skills and technology both in and beyond the rail and construction sectors.
“Our trial work with PUNCH Flybrid is another great example of how investing in long-term national infrastructure programmes creates opportunities to draw on technology from across the economy that could potentially unlock significant benefits for our industry.”
Commenting, innovation lead for Rail at Innovate UK, Kelvin Davies said:
“Innovate UK is delighted to work with HS2 in the delivery of innovation for this prestigious programme, and through this collaborative working a new relationship between HS2 with PUNCH Flybrid has created the opportunity to explore the potential offered by a tried and tested automotive technology to save fuel, cut costs, reduce CO2 emissions and create possibilities for future economic growth in the high-value manufacturing and engineering sectors.”
The site is operated by Skanska Costain STRABAG joint venture (SCS JV)
The site, where HS2’s London tunnels surface is, is operated by the project’s tier one civils contractor Skanska Costain STRABAG joint venture (SCS JV).
SCS JV managing director, James Richardson said:
“SCS JV is committed to reducing our environmental footprint by identifying innovations like this flywheel technology, which has immediately halved our diesel consumption of one of our cranes operating at our Euston approaches site.”