For more than 80 years, the Modular & Portable Building Association (MPBA) has spearheaded the growth of the sector. Chief executive Jackie Maginnis discusses how far the industry has come in recent years and how exciting the future looks
Keeping ahead of current thinking as well as anticipating future trends has meant the MPBA and its members have remained relevant.
Although some may consider modular construction to be a recent innovation, the MPBA’s oldest members have been trading since the 1930s. As the market for permanent and temporary modular buildings continues to expand and develop, hitting a milestone anniversary means it’s a good time to reflect.
What are the origins of the MPBA?
Originally known as the Prefabricated Building Manufacturers Association of Great Britain, modular construction was born out of adversity. As the UK emerged from the devastating consequences of World War II, it was a time of great innovation to get the country back on track.
With extensive destruction in many areas of the UK caused by bombing, this resulted in a need for new buildings to be made available rapidly and be transported where needed without significant haulage demands.
Former munitions factories began producing the components required to create “prefabricated” buildings. These cost-effective, factory-manufactured buildings were erected throughout the UK for housing and other purposes.
The need for a trade association back then was the same as today – to provide one consistent voice for all manufacturers to government, create an element of standardisation and develop a specific supply chain to meet the industries growing needs.
How has the MPBA changed since its conception?
Trade associations are unique. We are an association for the members, run by the members. By that, I mean our members collectively call the shots. From major players to smaller niche companies, all opinions count.
With some founder members still within our ranks, it is hard to believe that industry pioneers in the sector such as Wernick Group have been around since 1934.
Not long after, other major players in today’s industry joined the ranks, with the foundation of Portakabin in 1961, followed by Elliott Group (now Algeco) in 1963, Pickerings in 1969 and Thurston Group in 1970.
The MPBA has also been a quiet trailblazer across manufacturing and construction. There are very few organisations that had a female chief executive 15 years ago – a position I still proudly hold today.
A recent industry survey found that almost 50% of all staff across our members were female, particularly in the temporary building market as hire controllers and project managers.
The association is run by its members – how is this managed?
Governance is a high priority. As the CEO, I am accountable to an elected council of members that meet on a quarterly basis and guide our strategy and direction.
Feeding into this, we have technical, health and safety member committees that have collectively influenced Building Regulations and industry guidance.
Our most recent members group is the sustainability committee, with a collective focus on carbon cutting and net zero, what this means to the modular industry and what an important role the circular economy plays in reaching this objective.
We will be launching our Roadmap to Net Zero later this year. Our very active marketing group ensures that we continually provide education and awareness of the sector to the entire construction industry.
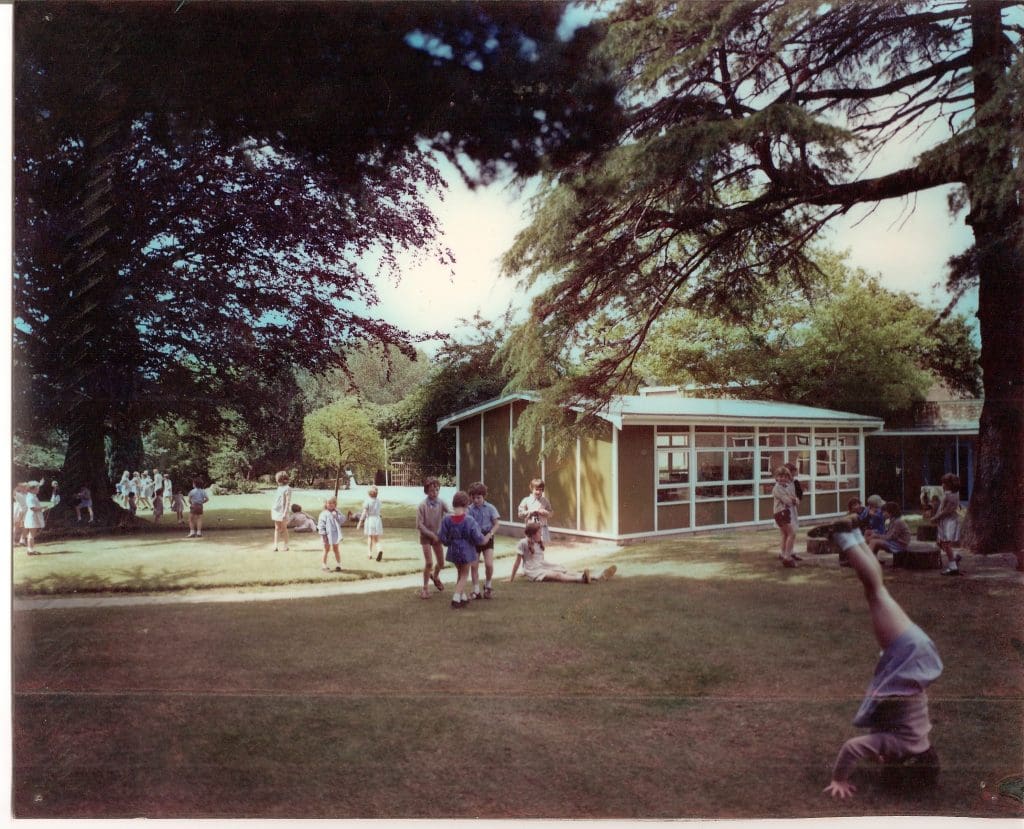
The MPBA is very active at industry events – how do you maintain this presence and stay relevant?
The industry is constantly developing. As early adopters of offsite construction, councils and local authorities were using modular technology across all sectors in the 1970s and 1980s to cope with the baby boom and the need for more education buildings. This was the development ground for Modern Methods of Construction (MMC).
The MMC Definition Framework as we understand it today was developed in 2017 following the publication of the Fixing our Broken Housing Market White Paper for the UK government.
We have fully embraced the terminology, specifically as Category One and Two in the non-domestic sectors relates to the approach our members have been developing for over 80 years, sometimes the construction method is not new, only the terminology.
We are part of the wider offsite sector and are proud advocates of Offsite Construction Week, Offsite Expo and have supported the Offsite Awards since their inception.
While backing the wider offsite industry, we are careful to retain our own identity and objectives and not become lost as the sector continues to grow. We recently hosted our second annual conference and MMC Awards, focusing on non-domestic modular construction, which is an area that has reached a level of maturity that the modular homes industry is looking to achieve.
Can modular construction solve the housing crisis and improve efficiency?
There is still a lot of work to be done. The underlying challenges of the housing shortage are more complex and political than simply finding a quicker way to build.
Manufacturing facilities require a substantial investment of time and money to set up and need a constant pipeline of work to provide a return on that investment. The ‘stop-start’ nature of residential construction is not conducive to keeping a factory constantly running at capacity. This is why so many of our members operate in sectors such as healthcare and education, where modular approaches have been successfully applied for decades.
So modular construction can play an important part as it did back in the 1940s but it is also essential to recognise that the non-domestic sector has differences – different Building Regulations, different fire regulations – to say that all modular construction is the same, is to say that all sports are played with the same shape and size of ball.
Pre-manufactured Value (PMV) is now a prerequisite – albeit needing a clearer definition – but it is having a positive impact on our industry and is influencing many specification decisions across the built environment.
What does the future of MPBA look like?
Modular technology is far removed from the “prefab” buildings of yesteryear and so is our association. We now have a seat at the top table, influencing government decisions.
The support for government projects, particularly in healthcare and education, has come from lobbying over the years from the MPBA and our members to get specification and procurement changes in place.
A lack of appropriate training was a major issue for our sector, so we developed a training centre in 2018. Based in Coventry, the MPBA Learning Hub now offers National Vocational Qualifications (NVQ), electrical and specialist training, as well as online courses. We also have approved an Apprenticeship Trailblazer that we are looking to roll out with a key partner soon.
After all these years in the industry, I am still committed and fiercely passionate about representing the MPBA and our members – this dedication and drive is shared by the entire MPBA team.
Our association and the modular industry have come a long way in the last 80 years. From simple single storey prefabricated buildings to complex manufactured school and hospital buildings, which are digitally designed, rigorously tested – and according to data from RICS members – completed 50% faster than traditional on-site methods. We cannot yet claim to be ‘mainstream’ but we are constantly working on making that a reality.