Hertfordshire Building Control explores the development, adoption, and application of their Gold Guide for thermal insulation standards in building regulations
Origins of the Gold Guide
Way back in 2006, The Hertfordshire Technical Forum came up with the idea of a handy guide to help architects and builders adjust to amended Part L thermal insulation standards that came into the building regulations.
We thought that they were high standards – looking back, little did we know!
The Forum was made up of senior building control surveyors from the ten Herts local authorities who all contributed to formatting the tables offering solutions on how to comply.
We had a lot of surplus orange paper to print it on, so it became affectionately known as the ‘Gold Guide’.
Nationwide adoption and validation of the Gold Guide
The guidance on thermal insulation was tailored to cover requirements for home extensions where regulations generally look for roof, floor, and wall elements to achieve target maximum U-values.
It proved to be very popular and became a reference for local authority building control surveyors and clients around the country.
That led to it being adopted as a national publication by LABC at which point we worked with The British Board of Agrément and the Insulation Manufacturers Association to ensure that all solutions were properly validated.
The new Gold Guide for Future Homes Standard
Fast forward to June 2022, and there was a clear demand for a re-publication of the guide to cover another amended Part L, bringing in interim requirements for the Future Homes Standard.
Once again, Hertfordshire Building Control managed to get most of the key players in the insulation market around the table and repopulated the tables with a new set of suggested solutions to ‘hit the marks’ on lower target U-values for walls, floors, and roofs.
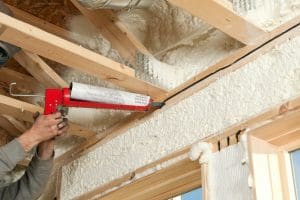
Challenges with foam insulation in cavity walls
This year, feedback from our building control surveyors who inspect work in progress in this county suggests that builders seem to be getting to grips with the new thermal insulation standards and specifications overall.
An exception appears to be their use of foam-type ‘full fill’ insulation in cavity masonry walls. These materials were less popular prior to the lower U-values for walls coming into force but are now more common.
The typical format is a 90mm thick board, leaving a 10mm residual space in a 100mm cavity as part of a 300mm cavity wall.
As with many new technologies, some busy builders often don’t find time to familiarise themselves with manufacturers’ advice.
Relying on initiative and common sense can be perilous and expensive!
Handy hints for building cavity walls with foam insulation
The following is a list of handy hints to bear in mind when building this type of wall.
It is by no means comprehensive, and it is always best to refer to the manufacturer’s own technical advice or the Agrément Certificate for the product.
- Boards are either butt jointed or have a tongued and grooved interlock.
- Some boards have inner and outer faces covered with foil and fleece respectively.
- The inner leaf should be built up, with excess mortar removed from the cavity face, before fitting a course of insulation boards. Temporary use of cavity boards is good practice to keep mortar droppings off the exposed board’s upper edge and keep the small cavity clear while the next courses are built.
- Systems typically look for a 10mm residual cavity to be maintained, and proprietary clips should be fitted onto wall ties to maintain it. Obviously, it is impractical to expect that to remain clear while building the outer leaf, but it provides space for mortar to exude.
- The first run of boards is usually set 150mm below DPC level on wall ties, maintaining at least a 25mm gap to the concrete cavity fill.
- If butt jointed, then all joints must be sealed against moisture with the manufacturer’s recommended adhesive tape. The tape must overlap 50mm from the joint, so it is usually 100mm wide.
- Corner details need special attention and can be either butt jointed or mitred (unsurprisingly, we are yet to see the latter option being adopted). The T and G systems incorporate an additional 400mm wide vertical damp-proof course on the outer face of insulation wrapped around the corner to overlap the vertical joint.
- For butted systems, the same adhesive tape can be used to seal the vertical corner joint. It needs to cover the exposed edge of the foam and overlap 50mm onto the foil faces of abutting boards.
- Builders are used to fitting wall ties at every block course vertically adjacent to openings, which necessitates ties penetrating the insulation board. A practical solution is to form a small slot through which the tie can be pushed, finishing with overlapping tape to seal. Some manufacturers suggest the alternative of fitting two ties at every second block course, although that may not accord with the structural requirements of BS EN 1996.
- Finally, don’t leave your insulation boards out in the sun. They can warp, making it difficult to fit within the wall cavity.
Mineral fibre/ fibreglass batt full fill solutions
Mineral fibre/fibreglass batt full fill solutions for cavity walls seem less problematic as builders are already well-accustomed to such technology; they just need to apply it to the much wider cavities identified in our guide.
We sometimes find a need (hopefully very early in the build!) to remind builders that the selected wall ties must be compatible with cavity widths and that at least 50mm end embedment must be achieved in both leaves of the wall.
Allowing 25mm for site tolerances, a wall with a 150mm wide cavity needs 275mm long wall ties. General purpose (type 2) ties can still be used at the usual spacings to meet thermal insulation standards.
Trevor Clements
Training & Development Principal
Hertfordshire Building Control
01438 879990
building.control@hertfordshirebc.co.uk
www.hertfordshirebc.co.uk
X
LinkedIn
Instagram
Facebook
YouTube