Leaving the design of passive fire protection until the construction phase is preparing to fail, writes Adam Shipstone of the Association for Specialist Fire Protection
Construction programmes are usually split into separate packages and are designed and developed at a different pace from each other. Think of the four major construction packages as silos: structure, dry lining, MEP & PFP.
Passive fire protection is usually not considered in the design phase until decisions in the other three silos have been made and implemented. Decisions made at the design stage can hardwire problems in the final silo.
The silos move through the RIBA Plan of Work independently and at different times.
For example, our structural silo can move through RIBA 0, 1, 2, 3, 4, 5 before passive fire protection has even got to RIBA 2 or 3.
This usually means the structural silo that has got to RIBA 5 and is being erected on site may have to go back to RIBA 4 (Technical Design), as no consideration has been given to the passive fire silo, which still may not have got to RIBA 2 or 3.
Incomplete design and site changes
Looking at an example, we have a steel frame with a CLT floor slab. There is no standard for steel frame and CLT slab fire resistance; however, there is some ad hoc testing/guidance in development.
Further to this, there are no DIAP/EXAP rules for services passing through the timber slab. Again, usually, this doesn’t become a problem until the passive fire silo has entered RIBA 3, by which point the structure silo is in RIBA 5 (being constructed).
Likewise, with on-site design changes, where there may be a desire to increase ventilation and airflow in certain areas, more ducts are installed, which need to pass through structural elements such as steelwork. Holes are cut into the webs of the steel beams, turning them into cell beams.
This would not have been accounted for in the design stage and takes the steelwork outside of the intumescent coating that may have been applied.
In the two examples we have detailed, there have been huge costs incurred. In the first, new steel had to be installed to reinforce the already installed steelwork, and in the final example, a whole new passive fire system had to be installed on to the already protected steelwork.
Building Safety Act changes: What this means
We tend to find that construction follows a “Construction–Design–Approval” model with a lot of overlap.
The Building Safety Act gateways will fix this issue.
- Gateway 1 = RIBA 0: The planning application stage; tighter controls around the fire statement, competency of those preparing and scrutinising. This was implemented in Oct 2022.
- Gateway 2 = End RIBA 4: The initial building control stage before works commence. This gateway provides a “hard stop” where construction cannot begin until the Building Safety Regulator is satisfied that the dutyholder’s design meets safety requirements. This has been enforced since Oct 2023.
- Gateway 3 = End RIBA 5: The completion/final certificate phase pre-occupation.
All of this will give us the following: Design–Approval–Construction. Each of these will be a specific stage with no overlap.
It is illegal to start building before the design is approved and it is illegal to build anything other than the approved design.
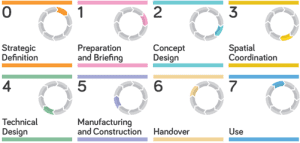
Who is responsible for the design of passive fire protection?
This is probably the toughest question to answer in this article. The challenge is that no one has all the answers.
Currently, the responsibility is usually passed down from the Principal Designer (PD) to the Principal Contractor (PC) and, in turn, it is passed down to the Specialist Contractor, who is then asked to change decisions made and constructed 12-18 months prior.
Ultimately the PDs have the legal responsibility of the design of passive fire protection. The issue is they take this responsibility with little experience in passive fire protection.
To help with this lack of understanding the ASFP is about to release Advisory Note 33, which will suggest ways to mitigate the risks surrounding all this.
We also advocate for early discussions and design meetings with the PD, PC and specialist subcontractor to avoid issues later on in the construction phase.