Wates Group’s construction of a £28m underground gallery and main entrance to London’s V&A Museum presented enormous challenges – but also brought huge rewards
This exciting project to build a vast new underground gallery and Exhibition Road main entrance to the landmark V&A Museum was much anticipated by the institution itself and by the public. In January 2014, Wates won the opportunity to take on the £28m gallery and courtyard construction challenge, which was to prove enormous in scale and complexity – but delivered huge reward and satisfaction.
The project spanned the next three years, completing in May 2017 and opening in June of that year. The overall project saw the Exhibition Road side of the V&A come into view, instead of being hidden behind a forbidding grey stone wall, with new gates to a porcelain-tiled courtyard and a bright glassed-in café area – all located above a huge new subterranean gallery.
Just one year after opening, it was credited with helping the V&A to buck the trend of declining museum visitor numbers, driving up its own figures by a phenomenal 26% and improving the visitor experience.
Neil Lock MCIOB led the initial Wates bid and was project manager for the V&A Museum initiative, using Elecosoft’s Powerproject for planning, progress management and to support reporting throughout.
He not only delivered a stunning reference achievement for Wates Construction, but was later personally rewarded by winning the overall title of Construction Manager of the Year from a strong field that included his own Gold Award in the Public & Infrastructure category.
Enormity of vision
The architect’s vision was compelling. The enormity of the technical challenge it created was clear from the outset, thanks to the large physical scale and difficulties of building what would become the largest column-free gallery in Europe. To do this beneath the site of the Grade I listed V&A Museum meant they would be building less than a metre beneath and within inches of five historic monument structures filled with irreplaceable artefacts. The new elements would bring a more modern look and feel yet would need to dovetail seamlessly with the historic structures internally and externally.
Lock developed a robust construction programme linked across the board from design to procurement, through manufacture and to build, approaching 1,100 lines of activity in all. He used Powerproject to manage this complex project start to finish, from clearing the old 1970s building in what was known as Boilerhouse Yard, through excavating down 16m, punching pilings up to 25m deep, creating the 1,100 sq m gallery, and finishing a breathtaking tiled and gated courtyard entrance featuring 9,500 hand-laid porcelain tiles plus a café roofed with 50 sq m of structural glass.
Powerproject is a very familiar programme planning platform, as Lock explained: “We use Powerproject in many ways. Wates has used Powerproject since I can remember, and I’ve used it for more than 20 years. Although we have planners, mostly planning on this project was by myself, the supply chain, and supported by a partner from our central document control team, who had worked with me at bid stage to draw up the original programme. During the build, I spent around a full day a week in the programme.”
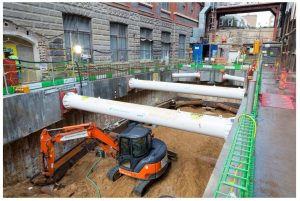
Every milestone mattered
Neil acted as the essential key link not only with the client but between all disciplines, overseeing 165 site staff and up to 35 subcontractors at its activity peak.
Perhaps unsurprisingly, the client was keen to stay in constant contact and understand progress to a fine degree. They saw each milestone met, however small, as a reason to celebrate. It made progress communication very important indeed.
“Our progress reporting was generated straight from Powerproject, with spend data from our forecast mapped against progress, so we could track actual versus forecast spending,” Lock said.
“For client progress meeting reporting we would do a standard dropline, then a dropline against the critical path. Using Powerproject, we generated an S-curve that maps spend against progress – it gives people a simplified view that is much easier to understand than looking at the main programme.”
Sharing information and plans between the large numbers of different players was important, as Lock explained: “Because of size of the site, everyone had to have sight of what everyone else was doing. We exchanged sub-programmes from suppliers constantly, and were also sharing our own programmes, so everyone could see the full scale of the interface with other works. I am an advocate of sharing programmes fully and believe it is a point of good supplier management not to restrict access to the overall programme.”
The logistics of sharing information were not difficult: “We could share our Powerproject project information with subcontractors and suppliers easily – some were using the same software so could take programme information directly, and we could export PDFs easily for others who were using spreadsheets or other project platforms. Without Powerproject programme how could we have explained what we were doing?”
The team made use of 3D modelling to help visualise, coordinate and detect clashes: “We use Synchro to run alongside the programme so when we play it we can see the timeline of where we will be. This wasn’t a challenge, since Powerproject integrates well with that system.”
City centre challenges
The site had just a single entrance on to Exhibition Road, one of the capital’s busiest thoroughfares, and one which was constantly crammed with traffic and pedestrian tourists in all seasons and all weathers. It meant that managing almost 6,000 lorry movements in and out to deliver materials and remove debris from the excavation was challenging – plus, until excavation was completed, there was very limited space for storage.
“Everything had to come in one way,” Lock said.
“That meant everything was restricted – and the more material there was, the less space. It meant that sharing information was vital. In a big open greenfield site that you can access from all sides everyone can have their own storage area. When there’s only one way in, one crane, one storage location, by not sharing a programme, you are making it difficult – everything has to be carefully coordinated.”
Room for manoeuvre was tight, since an asymmetrical excavation site meant working with buildings on five sides, including a 30m dogleg in between tightly located buildings. This restricted space meant hoisting plant in and out of extremely narrow spaces.
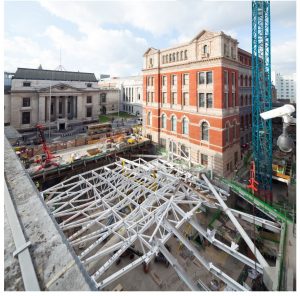
Planning the unplannable
Perhaps inevitably when working with historic structures, the team discovered that there were simply no straight lines or clear angles at all on this site.
There were also the usual surprises that come with excavations, which included numerous obstructions and asbestos, although luckily the archaeological watching brief turned up no delaying finds.
This constantly evolving need placed tight programme planning and management at the heart of the process, as Lock stated: “You simply couldn’t do a job like this it without a tool like Powerproject because it was so multi-disciplined, on so many different levels, with so many interfaces. You can’t keep track of it by writing it on a board. It must be stacked and linked logically. This must happen so this can happen. You need a form of ‘perfect plan’. No builder in the land should build without Powerproject or other professional-grade software.”
Precision planning was essential and constant physical monitoring was equally vital, since there were near-zero tolerances for movement and a constant concern about noise and vibration.
Constant critical changes
As a programme planning challenge, this project was particularly marked for its continual flow and sheer number of changes. Approaching 1,000 change requests were absorbed, coming both from the client as the design aspirations evolved and as realities and roadblocks emerged during the build.
“What stood out was the sheer vastness of the amount of change. I’ve been on many projects, but I’ve never seen change such as this,” Lock said.
The origin of the large number of changes often came from the realities of the site as its complexities were revealed, he added.
“The design when we took the project on was still somewhat conceptual in terms of architectural finishing and detailing. It was structurally very good, so there were very few changes there, but because there were no straight lines on the building, and it curved and interfaced on every junction, and levels and working to such tight restrictions, once we started to get into the detail about what were the systems and what actually had to be achieved to get warranties, it was clear that changes were needed.”
Lock outlined the impact that those many changes created for the timeline: “Whenever there are changes, we have to understand the real-time delays they will create. So as new drawings arrived or changes became necessary, we did a time delay analysis. We had to consider whether any change would require more design work, whether we needed to procure, if so, how long that would take and what else it would affect – then built all those time factors into the Powerproject programme. With 978 changes, those were significant.
“Using Powerproject, we would pull the timeline out of the programme, insert the extra work needed into it, drop it into the programme and reschedule the programme. Then we can see what it does to the critical path and the end date. Depending on where the links are, we’d see the effect it would have. It might be zero additional time if it is not on the critical path, but still require manpower and additional work.”
Changes to the originally planned timeline were carefully negotiated, and the original 141-week target became 176 weeks in all. This shifted the target completion from end of 2016 to May 2017, and the project was delivered bang on the agreed schedule.
Once in a lifetime
This kind of opportunity and challenge is rare – after all, as Lock observed, “it is an iconic structure that will never be built again”. Everyone involved in the build realised it was an opportunity that could only have come along once in a career despite, or perhaps because of, its difficulties.
In summing up the challenges of this landmark project, Lock said: “This was anything but mundane and straightforward. It gave us different things to think about, different problems to work on. Sometimes there’s just one way to do something. Here, you needed to think outside the box. Complex building like this is solution-driven: it tests your skills, stretches your brain, and you have to focus on how to overcome challenges.
“A job like this is a once-in-a-lifetime opportunity, and there will never be another one like it. It will leave a legacy behind that we can tell our grandkids about. When and how will I ever get a chance to build better than that?”
As a Wates project, it paid off not just in pride in an extraordinary job executed perfectly, but also in the acclaim of industry peers. Leaving a legacy for the nation and delivering demonstrable results and real value for the client.
Elecosoft
Tel: +44 (0)1844 261 700
Twitter: @Elecosoftpp