PBC Today sat down with Imerso CEO Frederico Valente to discuss the benefits of Imerso’s As-Built-to-BIM software, fire safety, and lean construction processes
Imerso has the fastest and simplest 3D scanning workflow on the market, letting your teams capture documentation at every stage with As-Built-to-BIM software at the press of a button and completely independently.
What inspired you to work with As-Built-to-BIM software and create Imerso?
The idea of working smarter, not harder, is very powerful. I’ve always had good friends and connections in the architecture and engineering space, in particular in smaller agencies where every employee is very dedicated and must do the work of 3 – 5 people.
At the time, I noticed a common complaint about the need for traveling often to the job site to get context, measurements, and other information.
My friends would comment on how difficult it was to ensure their models match the reality based on the few measurements and drawings they made in their visits, and how a missing data point would require bothering a customer and booking yet another visit.
Inaccurate models were becoming a massive and costly problem for the project later, and a reason for losing the confidence of a customer. This led me to investigate and learn about the challenges and importance of reliable As-built data.
I’ve challenged my co-founders to start experimenting with 3D reality capture solutions, which in my mind was a technology solving the problem brilliantly: fast, accurate measurements and imagery in every direction in a few minutes. The problem was the high cost of scanner devices, as well as the surveying expertise required to use them.
Our first product was a 3D scanning app for mobile devices that anyone could use as simply as taking a video, while getting a pretty decent Point Cloud scan for making models in the planning phase of a project.
This was a really neat solution that also helped architects win more projects because they could make a bigger number of bids that stand out from any others, with better data accuracy and engaging visuals. We were eventually challenged to give a demonstration at one of the largest construction sites in Norway at the time.
The project management was looking for better ways to track the work quality and progress beyond the traditional photos, report checklists, spot-checks and red-line diagrams. The team was very excited about the idea of getting a 3D site reconstruction with real-life measurements on a routine basis, without the need to call expensive third-parties that need long lead-times and work interruptions.
Someone pointed out the opportunity to compare this data against the building specifications in BIM for verifying compliance and find deviations automatically.
This was our AHA-moment and the Imerso concept has evolved ever since, in the direction of supporting fast feedback cycles in any construction setting and enhancing Lean practices.
What makes Imerso different from 360 Panoramas and similar solutions?
Imerso is very different from any other solution on the market. It surpasses alternatives relying on human judgment for verifying site conditions, and uncovers hidden issues that on-site experts miss.
Checklist apps with photos, and 360 Panorama solutions provide only a marginal benefit compared to regular photos. For every such image, customers require a pair of human eyes looking at them and making a decision, which is always subjective.
Unlike AI, which is quick, objective and unaffected by factors like diligence, tiredness or lunch breaks, and helps us, humans, identify severe errors that are impossible to see on images alone.
Another downside of such solutions is that photos lack measurements. We provide them because they are good to get a sense of status and progress, but not for actual quality inspection or compliance. So users can only conclude if an object is onsite or not, but never on whether the object is in tolerance.
For example, you wouldn’t expect a doctor to set a correct diagnosis for your internal organs based on a selfie. Instead, you’d make an appointment because doctors require measurement-based examinations, and jobsites too.
We’re getting many new customers that tried 360 photo or video solutions and with time ended up missing big issues, which quickly escalated and became costly. This is because Imerso provides both measurement-based jobsite data, AI analysis, comparison to BIM and updates of BIM to As-Built.
Imerso relies on millimeter-precise data from laser scanners, delivering a simple DIY scanning process without the need for expert involvement. This way, onsite users capture the reality easily and don’t need to make any judgment or consideration as the As-Built analysis and automated As-Built vs BIM comparison is delivered for them.
The process takes minutes, eliminates subjectivity, and provides both general and in-depth details, so that users see everything is on track or deviated, and share it with teams for quick issue resolution.
We also enable keeping BIM updated to the site changes, which again cannot be achieved with 360 images. And as a bonus, clients gain highly accurate documentation of the actual As-Built reality with very precise measurements at every step of the project, nothing that can be achieved with photos and diagrams.
Why not use 3D laser scanning solutions for surveyors from the big players?
Very fair! These solutions designed for expert surveyors in meeting some of the jobsite needs, yes. However, most of us don’t have advanced skills required to use such technology. Even in large companies there are only few users capable to use it, and much less in every jobsite.
On the other hand, crucial features like updating BIM to As-Built reality and their BIM to As-Built comparison is limited and complex to conduct. As there is no AI automatically delivering it – users do it manually object by object.
And this is the case both for analyzing the captured 3D data, as well as the onsite data capture process itself to begin with, and deal with complex procedures involving geo-referencing and setting coordinates.
As a result, such approaches need lots of lead-time in advance, the job site must be vacated and cleaned up (interrupting the fieldwork), and the results can take days or weeks to return to the project managers, who don’t know how to handle the data, which is already outdated by then.
Imerso is the only solution that requires no surveying expertise or training. Nearly all our users have never made a 3D Scan before in their lives, and are now routinely capturing the job site with survey-grade equipment on a daily or weekly basis. This democratization, together with the automation in data analysis, means that the job site can be tracked at high-frequency and customers immediately receive what they need most: Answers, not just data.
Fire Safety compliance is becoming a trendy topic. Do you have any examples of Imerso usage for this purpose?
Of course! We’ve seen customers leverage Imerso to control cases like the spacing of technical HVAC/MEP installations through the concrete superstructure, and ensure the regulatory necessary spacing for fireproofing is compliant.
Users have leveraged Imerso data into other leading software tools like Solibri, to apply custom rulesets based on the most current As-Built status.
This is super useful, as there are often hundreds to thousands of objects onsite needing such control, and are overlooked from traditional random sampling or visual inspections with 360 Panorama photo tools.
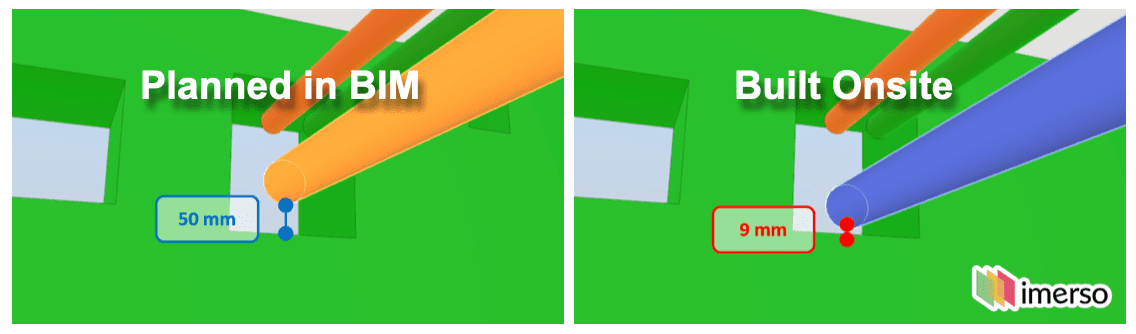
Another common case is the installation of interior partition walls that rely on vertical metal studs placed at specific intervals. What our customers often see is that the placement of these metal studs can coincide with the space planned for a technical HVAC/MEP element that crosses that partition wall.
The most frequent consequence is that later teams will cut the metal studs in order to install their components across the wall, thus violating the fire-proofing compliance of the partition installation. The whole thing is covered up with the wall panels, and the issue stays invisible until a compliance inspection reports the violation and demands a tear-down and rework of the entire structure. This can be extremely costly and delay the delivery of the building.
Imerso can analyze 100% of these metal studs, and predict future collisions of installations that are soon to be built. This way, our customers prevent the problem entirely before it happens.
What do you mean by “prevent the problem before it happens”?
I mean that having the ability to closely track the current As-Built conditions, with very accurate data taken routinely every week, allows two very powerful things: not only analyze the jobsite status today against what the plans say should be there today, but also by finding deviations and their consequences.
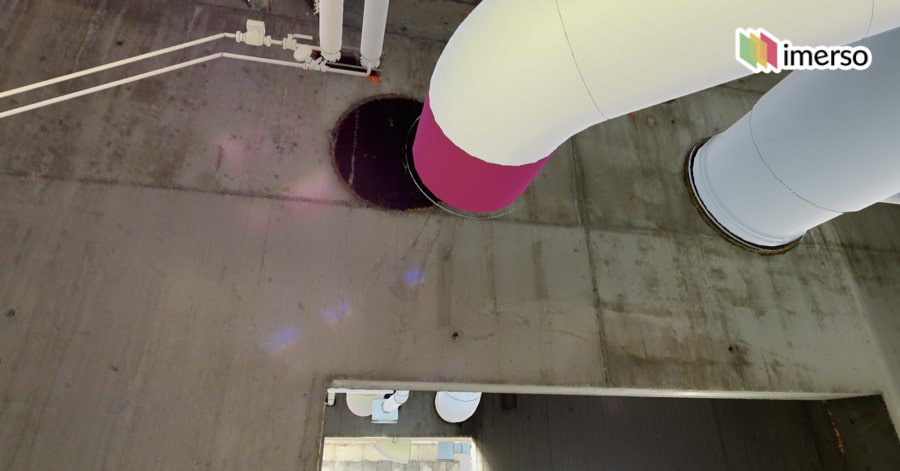
Not every deviation is necessarily a problem. But deviations that violate regulatory requirements, and especially deviations of previous work packages that create problems for upcoming teams, are high-ticket items that Imerso customers can find and fix very early (while its easy and the responsible team is still onsite), instead of overlooking the issue and letting the costs and delays escalate into the future when every solution will be sub-optimal.
What is your view on the future of Imerso and the construction industry?
The construction industry is steadily moving towards sustainable, lean-based processes that underline team productivity and a focus on work quality, while eliminating unnecessary costs and waste. We already see Imerso playing a pivotal role in this transformative journey.
One of our clients recently calculated Imerso’s impact on productivity worth 2% of the construction budget. In this project, our customer noted that a single Imerso user achieved in 60 days what would require an entire team over a year to complete.
We see that Imerso is offering a critical piece of the Lean Construction puzzle: the building plans are only as good as your ability to measure the performance of their execution.
Having an efficient way to routinely track progress and work quality and make frequent adjustments throughout the project is crucial for continuous improvement. That’s what our customers have realized: better projects require better feedback loops and information capturing.
This type of direct monitoring of the onsite reality also has direct impact on other trending topics in construction, such as better use of prefabrication, reduced waste and more sustainable projects.
In the near future, Imerso will become a standard in the industry, adopted by progressive construction managers and BIM leaders who are determined to stay ahead of the competition.