Precast detailing reinforced with BIM offers transformational advantages and an overall increase in project ROI, explains Bhushan Avsatthi, Hitech CADD Services
2D CAD has been used extensively by designers and engineers to plan, design, and construct buildings. The advent of advanced digital processes and tools like BIM have allowed stakeholders to look beyond design.
From a Precast detailing perspective, possibilities driven by BIM are enormous. 3D modelling of a virtual building in a 1:1 scale with comprehensive data on reinforcements and details can be leveraged to store data in the model. This can be used for precast production, scheduling, logistics, cost estimation, and field progress tracking.
BIM-based precast construction supports precasters and Precasting firms to compile data from various sources and tools without the need to backtrack toward 2D CAD. 3D BIM makes it simpler for multiple trades to communicate and collaborate information and drive model-based prefabrication.
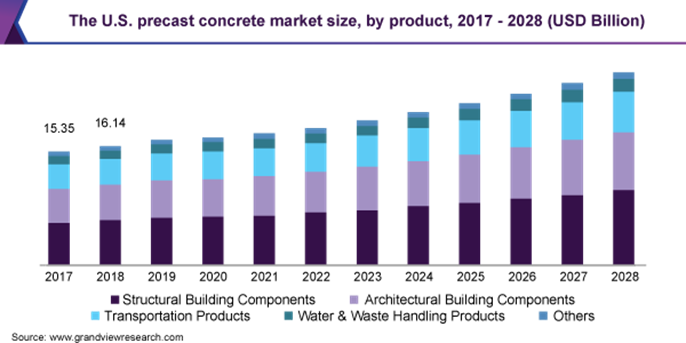
Traditional 2D CAD used for precast planning and layouts pose a series of challenges including, inaccurate dimensions, incomplete project documentation, structural integrity issues, onsite clashes, schedule overruns, and diminished productivity.
There is a myriad of unrealized advantages for precast such as simple and quick comparison of precast concepts during preconstruction, leading to higher constructability, and cost efficiency. After the detailing process is complete, project stakeholders can leverage fast precast production and onsite logistics.
Top five advantages of precast manufacturing with BIM
-
Error-free clash detection for interference-free precast installation
Precast detailing and manufacturing or rebar design can be complex. The use of 2D techniques are error-prone, Rebar detailing requires accurate and in-depth visualization to eliminate design errors.
Coherent visualization to design precast using clash-detection tools serves as a preemptive solution to diminish collisions in rebar design before actual fabrication or onsite work starts. Inter-disciplinary clash-detection through RFIs and design coordination reduces rework and promotes seamless onsite installation of precast members.
Precasters can use 3D BIM models and finalized drawings for manufacturing. These benefits drive better productivity, precise quantity takeoffs, and reduction in errors during fabrication and erection.
2. Improved process optimization in the design stage reduces time waste and erection delays
BIM offers a powerful set of tools like Revit and Navisworks for precast layout planning, manufacturing, progress tracking, etc. For example, fabrication, logistics, and erection sequences can be defined and traced from the 3D model.
The optimal use of logistics or casting component placement to optimize transportation can be achieved through smart scheduling to save money, time and reduce material wastage. When Precasting firms are reinforced with purpose-built tangible tools that are simple and effective, BIM possibilities would be realized efficiently.
3. Seamless data and report creation and sharing accelerates design and manufacturing
Generating reports through Revit can accelerate design and manufacturing for precast elements. Whether it includes extracting accurate precast quantities, generating bar lists, or generating bar bending schedules, customized reports ensure time-savings and collaboration with multiple stakeholders. Information available in real-time drives greater decision-making, agile communication, and preemptive monitoring.
Rigging plans and installation schedules can be created through an IFC model to diminish the need of storing precast elements onsite. They can be transported as per their erection sequence. Precast products or projects can be modelled and tracked to enhance internal workflows for higher productivity and reinforcing external workflows to benefit a myriad of stakeholders.
Precasters can store crucial information on each precast piece leading to time savings for planning and transport and achieving accurate concrete pours.
4. Quick model-based generated shop drawings enable precise fabrication and reduced rework
Shop drawings from a coordinated 3D structural model contain dimensions, specifications, location, material type, etc. of precast elements. Extracting rebar detail views from the model and superimposing it on the drawing layout reinforced with reports and additional information helps create a comprehensive document set.
Deploying software-driven precast design solutions through 3D models can help contractors drive rebar bending, concrete casting etc. The presence of accurate and complete shop drawings reduces errors and improves the overall deliverable quality.
If precast teams or firms are given early access in the planning and design phase, BIM models can cut down on project lifecycle time through a single source of truth. Project costs can be reduced as a reason of cancelled back and forth activities leading to reduction in RFIs.
5. Greater focus on building constructability through process automation for greater data reliability and progress tracking
BIM reinforced with tools like Revit, Navisworks, Dynamo, APIs, or Plugins improve precast design through the generation of 3D structural models from 2D drawings. 3D model coordination with Architectural and MEP trades at various LOD reinforced with bar bending schedules and Rebar delivers greater constructability.
Parametric 3D modelling with continuous updates reflected across every stage of the building lifecycle supports multi-trade involvement to access data on precast elements.
Integrating critical information directly into the 3D model drives quick information collaboration and seamless data flow. The use of a 3D structural model containing every element, component, or part data at required LOD enables multiple departments to assess project state through a digital file.
Structural elements, embeds, and piece connections can be estimated in final design with BIM. In early design, BIM supports the generation of preliminary drawings and layout for beams, columns, slabs, panels, etc. Automation drives the calculation of concrete volume, while project complexity can be assessed to calculate labour and material costs.
The future of precast detailing with BIM
There are several ways that Precasters can utilize BIM to achieve enormous time and cost savings. Laser scanned manufacturing is the first option wherein Precasters do not require manual measurements to generate component reinforcement, embeds, or run additional QC workflows.
The existence of laser scanned or assisted precast manufacturing saves time, reduces the carbon footprint, and mitigates errors. 40% -70% time savings could be achieved with 3D BIM.
BIM-based precast construction is two times faster than traditional construction systems. Where a traditional building construction may take 3-5 years, prefabrication allows buildings to be brought to a usable state in 1-1.5 years.
This not only saves 50% of the time as compared to the conventional methods of construction, but also enhances ROI. High-rise hotels and corporate houses can start business earlier (as soon as precast construction is complete) as compared to waiting for 3-5 years for the building to be constructed with traditional methods.
The adoption of BIM-based precast construction has been on the rise due to the host of advantages it offers to contractors and AEC stakeholders.
Bhushan Avsatthi
Twitter: @hitechcadd
LinkedIn: Hitech CADD Services
Instagram: @hitechcadd