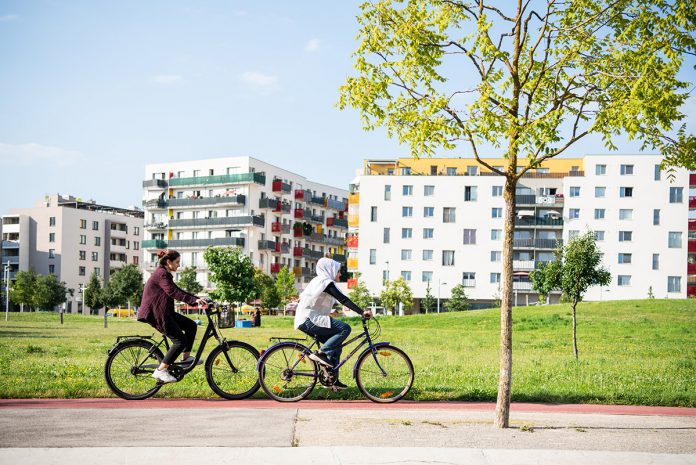
One of the largest urban development projects in Europe relies on precast construction for efficient and sustainable building – ALLPLAN software-enabled efficient precast detailing processes
Vienna is not only one of the most liveable cities in the world, but also one of the fastest growing on the continent. By 2027, its population is expected to pass two million.
In order to meet the growing demand for affordable housing, the city decided to tackle the challenge of developing a completely new quarter in the east of Vienna. Aspern die Seestadt Wien is – at 240ha – one of the biggest urban development projects in Europe and is being built on the site of a former airfield. Far from just accommodating citizens, Vienna has embraced the opportunity to develop a multifunctional district, creating more than 11,500 high-quality residential units and generous spaces for offices, manufacturing and service companies, science, research and education. New buildings with a planned gross floor area of more than 2.6m sq m will be built by 2030, comprising a total investment volume of around £4.28bn. A large portion of the buildings are being erected using prefabricated elements. This means that the elements are constructed offsite in a factory-style setting, before being transported to site and connected to other building components. For example, precast is a form of prefabrication as precast concrete elements such as slabs, walls, beams or stairs are cast in a factory and then transported to the construction site for installation.
Strengths of prefabrication
The main benefit of prefabrication is mass customisation, which enables a more efficient, manufacturing-style approach to the construction process. In turn, quality, reliability and safety are enhanced while productivity on site is considerably improved. Being able to work in a controlled environment ensures better finishes and can also help reduce waste through better planning and materials optimisation. Because of the higher precision and standardisation that can be achieved offsite, installation on site is easier, quicker and requires less manual labour, resulting in time and cost savings and better schedule certainty. Combined with the improved site management that arises from the ability to schedule just-in-time delivery of prefabricated components, overall site safety is increased significantly.
Ingrid Spörk, head of PR and communications at Wien 3420 aspern Development AG, underlines the importance of prefabrication to the development: “Our overall goal is to enable sustainable and highly comfortable living for all people that live and work here. Through prefabrication, we can forward the efficiency gains to the residents. The more prefab elements that are used, the less noise and dust pollution for the neighbours.”
Software solutions specifically tailored to the requirements of precast
Prefabrication is predicted to grow 70% faster than the rest of the construction industry and precast concrete represents a large proportion of this market. However, to benefit from this growth and keep up with demand requires adopting new digital tools that enable the productivity gains required. The digitalisation of products and processes through Building Information Modelling (BIM) is promoting a shift towards more data-driven decision-making and information sharing among project stakeholders. Combined with increasing industrialisation and new production technologies, new software solutions are needed to seamlessly connect design and detailing information to production and fabrication systems and relay this information to the construction site.
However, designing and producing precast concrete components is a much different process to placing in-situ concrete. Automating precast concrete production requires data that in-situ poured concrete does not. Precast elements need to be designed correctly the first time, with data that can be imported, shared, viewed and analysed by a multitude of project stakeholders, and in a format that can be read by production machines.
There are also additional matters that are not necessary with in-situ poured concrete, such as assembly and lifting considerations, transportation and logistics planning, and production and storage requirements. While reinforcement design and detailing are much the same as with in-situ concrete, the production of reinforcement bars and cages takes place earlier in the process, within the factory rather than on site.
Once on site, the construction team needs to understand how and where each precast element needs to be placed. These differences mean that a specialist software solution for precast concrete design, production and construction is a necessity rather than an option.
Dramatic growth of precast
STRABAG relies on precast construction for 80% of its residential projects in the greater Vienna area. Mischek, STRABAG’s precast manufacturer, is building about 25% of all buildings in the aspern Seestadt. For the design and implementation of the precast projects, Mischek relies on the software solutions from the Competence Centre Allplan Precast: “Planbar and Tim help us to generate a high level of data quality through their intuitive use. The Tim Quality Manager ensures that pure and correct data is transferred to production after approval by our customers.”
One of the first precast projects built by Mischek at the aspern Seestadt was the award-winning town house D10. The “Stadthaus” won an award for architecture and sustainability. The building has a low-energy standard and places a special focus on resource efficiency. The materials used have very good eco-efficiency and disposal properties. Locality also plays a major role: the mass-weighted distance between the construction site and the production site of the three most mass-intensive building materials is below 100km.
With the trend towards prefabrication – and therefore precast construction – growing, it is just a matter of time before the need for streamlined processes, improved productivity and standardised products becomes an expectation for precast companies. Those who choose to embrace these changes will get ahead of their competitors and place themselves in the best position to benefit from a better way of working and the coming surge in demand.
For more information, visit: www.allplan.com/precast
Christiane Ganster
Public Relations Manager
ALLPLAN Software Engineering GmbH
Tel: +43 6245 21001 403
Twitter: @allplan
LinkedIn: Allplan Precast
Please note: this is a commercial profile.