The new 3D printing technique is set to revolutionise the manufacturing industry and costs just £400
Scientists from the Institute of Sensors, Signals & Systems at Heriot-Watt University in Edinburgh modified a 3D printing process, known as stereolithography, to develop a new method of 3D printing that uses near-infrared (NIR) light to create complex structures containing multiple materials and colours.
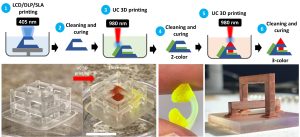
The project, Multimaterial Stereolithography by Crosslinking through Luminescence Excitation, received £280,000 of funding from the Engineering and Physical Sciences Research Council (EPSRC).
Dr Marques-Hueso explains: “The novelty of our new method, which has never been done before, is to use the NIR invisibility windows of materials to print at a depth of over 5 cm, whereas the conventional technology has a depth limit of around 0.1 mm.
“This means that you can print with one material and later add a second material, solidifying it at any position of the 3D space, and not only on top of the outer surfaces.
“For example, we can print a hollow cube that is mostly sealed on all sides. We can then come back later and print an object, made from an entirely different material, inside this box, because the NIR laser will penetrate through the previous material as if it were invisible, because in fact it is completely transparent at the NIR.
“In the same research project, we had previously developed a resin that can be selectively copper-plated.
“Combining both technologies, we can now 3D print with two different resins and selectively cover just one of them in copper by using a simple plating solution bath.
“This way, we can create integrated circuitry in 3D.”