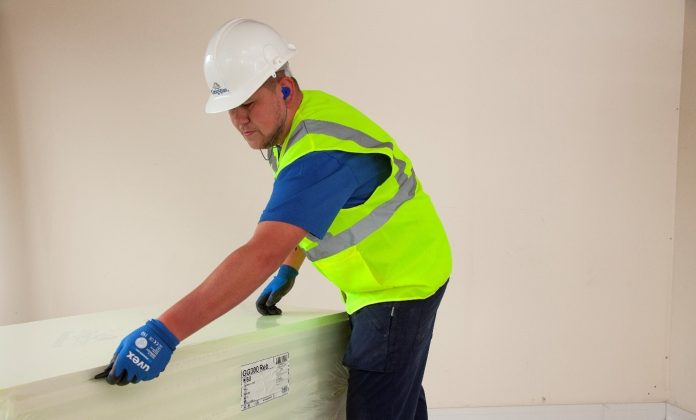
Ensuring the compressive strength of insulation keeps your building’s thermal performance at their optimum- lowering energy demand, emissions and bills
When specifying floors for applications such as rooftop car parks, industrial units and cold stores, understanding compressive strength and if the material is capable of handling heavy loads are fundamental considerations.
This is especially true when it comes to the choice of insulation.
Fitting the wrong product could cause the thermal performance of the construction to degrade over time, potentially notably increasing energy demand and carbon emissions.
Understanding compression with Behaviour and Creep tests
When fitting any insulation material, it is important to carefully check its compressive strength. When insulation materials are overly compressed, they can often become less effective at preventing heat loss, undermining the thermal performance of the building element.
All insulation products should be supported with clear information about their compressive strength. This is measured in kilopascals (kPa) and is the maximum load the material should be exposed to.
This is determined by a Compressive Behaviour test (BS EN 826:2013). The insulation is placed between two metal plates and put under a steadily increasing load until it either breaks or reaches 10% deflection.
The measure at the point this happens is its compressive strength.
In certain cases, structural engineers may also request further tests, known as a Compressive Creep test (BS EN 1606:2013). This assess the load an insulation product can be continually exposed to throughout its intended lifespan.
Specialist solutions can find the right compressive strengths for you
Modern insulation products come in a range of compressive strengths. For example, phenolic insulation boards typically have a compressive strength of around 120 kPa, which is suitable for most standard floor applications.
However, where floors are going to be exposed to especially heavy loads, such as heavy lifting machinery in a warehouse, specialist solutions are needed.
Extruded Polystyrene (XPS) boards are particularly well suited to these heavy duty applications – delivering compressive strengths of up to 700 kPa.
It’s important to be aware that these boards typically have fairly high thermal conductivities when compared with solutions such as phenolic insulation. This means that a greater thickness of insulation is needed to achieve the same U-value. This needs to be considered as part of planning for groundworks.
XPS boards come in a range of compressive strengths so it’s important to choose the right option.
A structural engineer should be able to carry out the loading calculations and advise what compressive strength of insulation is needed for your application.
Tips for insulation installation
XPS insulation can either be fitted below the floor slab or between the slab and the floor screed.
As XPS boards are highly resistant to moisture ingress, they can typically be fitted below the damp proof membrane (DPM) in below slab applications, although it is important to check the manufacturer guidance for the specific product to confirm this.
The DPM should be at least 300 micron and brought up to at least the level of the damp proof course (DPC).
The XPS boards can usually be cut with a fine-toothed saw. It’s important to measure and cut the boards carefully to ensure you get a continuous layer of insulation across the floor with no gaps. The boards should be loose-laid breakbonded with the joints lightly butted.
If you’re fitting more than one layer of insulation, then you should offset them horizontally so that the joints don’t align between the layers. To stop thermal bridging, a strip of rigid insulation (min 20 mm thick) should be fitted vertically around the room perimeter. The top of this strip should be level with the top of the floor screed.
If you’re fitting the XPS above the DPM or between the slab and the screed, then a polythene sheet (min 150 micron) needs to be laid over the insulation to stop concrete penetrating between the insulation joints. The sheets should have at least 150 mm overlaps with taped joints and be turned up 100 mm at the walls. The sand screed should also be at least 75 mm thick.
Delivering firm results
With the increases in energy costs in recent years, particularly for businesses, it’s more important than ever to ensure buildings are properly insulated.
By fitting specialist insulation, such as XPS, in high compression applications, you can ensure they continue to provide excellent thermal performance throughout the lifespan of the building.
You can learn more about Kingspan Insulation products and services here.