Martin Harvey, head of design and technical services at offsite manufacturing specialist McAvoy, shares the importance of understanding Design for Manufacture & Assembly (DfMA) principles to maximise the benefits of offsite modular design and avoid common pitfalls
According to the NBS Digital 2023 Construction Report, 57% of professionals stated they have been part of a project involving an element of offsite construction or manufacture – an increase from 50% in its 2021 survey.
This steady growth represents a changing construction industry, reflecting the momentum of utilising offsite manufacture for its minimal disruption on site, speed, quality and other advantages, as well reducing the reliance of on-site labour, which is in short supply.
As offsite manufacturing continues to grow due to its ability to alleviate pressures faced by traditional construction, the failure to fully grasp the offsite design skillset undermines its benefits.
A tendency to apply traditional construction design methods and timescales, especially to offsite modular design, is still prevalent, and often results in unnecessary costs and delays to projects.
Designing for offsite
A lack of exposure to, or understanding of, Design for Manufacture & Assembly (DfMA) design principles can impact the effectiveness of offsite modular design.
Working against five distinct principles, DfMA aims to reduce the number of components, ensure clarity, simplify fabrication and assembly as easy as possible, build tolerance into every component and structure, and reduce the need for adjustments.
All designers have the opportunity to use and embrace these principles to achieve the best outcomes. The DfMA principles guide the design through the lens of a standardised production approach, achieving the most streamlined, waste-free and efficient manufacturing, right through to the assembly process.
One of the first things to consider is the modular arrangement. Ensuring that the dimensions used in the design align with the range of lengths and widths of the manufactured modules is crucial.
Designing from the outset with the exact specifications in mind and using a grid format intended for offsite modular construction is what will guide the designer to the optimal layout.
It is always better to start with a design specifically prepared with offsite manufacturing in mind. While it is possible to adapt a traditional construction design, this may result in some degree of redesign and potentially a less efficient outcome. It may also not achieve the full benefits of an offsite manufactured solution.
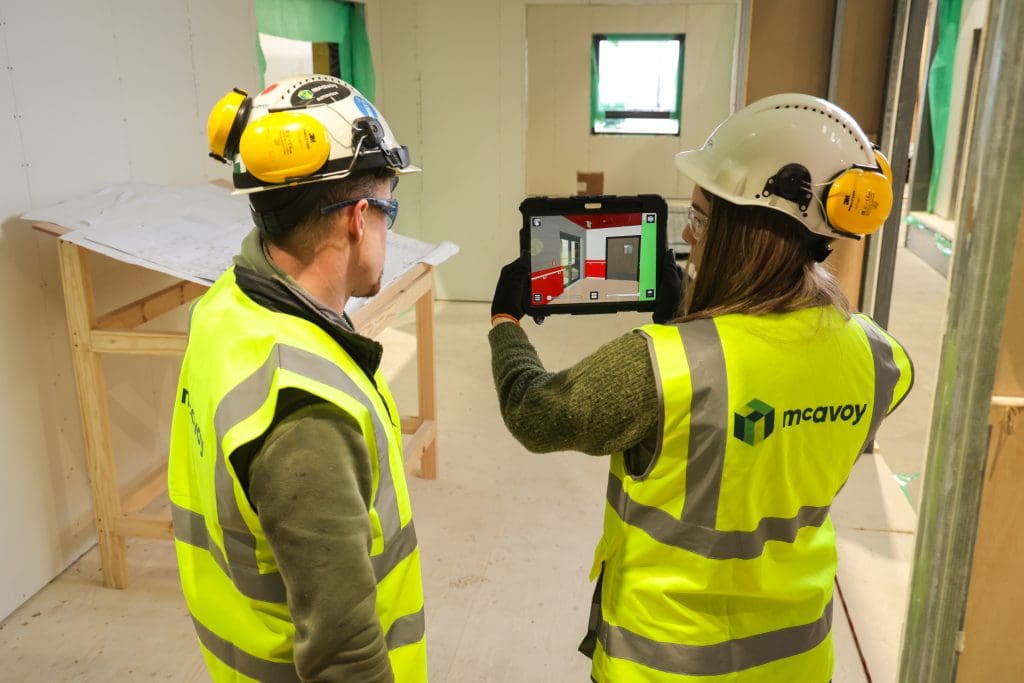
A standardised approach
When applying DfMA principles, the aim is to achieve the preferred layout, which is often bespoke, while using standardised components.
This should not impact the vision of the finished design, which is generally a concern from architects. Often, it is about working smarter and seeing where in the design the same outcome can be achieved but with fewer variations.
Standardising things like the wall build-ups, materials used and, where possible, the layouts of window and door locations brings significant benefits when manufacturing the subassemblies and delivering the modules to site.
It will also lead to a smoother and more efficient manufacturing process, with less room for error and waste, reducing the time required for the factory to produce and assemble.
The use of BIM and detailed digital models within the design process is another useful approach in offsite manufacturing. Not only for conceptualisation of the models but also to improve the detail and accuracy of the model information.
This is then used for creating precise manufacturing drawings, assisting with planning the manufacture, along with analysis of the module and subassembly weights and associated installations.
Also, with extremely accurate models, a greater level of planning can take place for installations. For example, in the ceiling voids of which the use of clash detection between M&E and structure is a major part.
Overcoming barriers
When designing for offsite, another consideration is transportation.
Highway rules and regulations, including bridge height and weight restrictions, mean that the module design must be created with these considerations front of mind.
While special road permits and alternative transportation can be sourced to ensure that larger sizing can be accommodated for while in transit, this all needs to be factored into the cost and timeframe of the project.
The good news is that with careful design, almost anything is possible and potential issues can be ruled out early, allowing for alternative approaches to be taken where necessary.
Through early collaboration with modular manufacturers, the design can be engineered to meet bespoke requirements. For instance, rather than supplying as one larger module, alternative designs formed of different module parts can still fulfil the brief.
Design freedom
Importantly, designing modular offsite applications to DfMA principles should not curtail the design process. The aim should always be to meet regulations and statutory body compliance while reaping the benefits that designing for modular has.
From healthcare, education and commercial buildings through to leisure, single living accommodation and more, offsite manufacturing is meeting the needs of various sectors.
As it continues to grow in prominence, ensuing that the specific requirements of modular design for offsite is not only understood, but embraced, will be key.