PBC Today explores whether light gauge steel framing is truly the most technically advanced material in the offsite technology portfolio, examines the challenges that are encountered when using these frames and discusses the properties and benefits when compared to other materials
Offsite technology has made significant advancements in recent years, with light gauge steel framing emerging as one of the leading materials. Light gauge steel framing offers a variety of advantages over traditional construction methods such as faster assembly times and increased design flexibility. It is quickly becoming an attractive option for builders looking for efficient building solutions within their project budgets.
This article will explore the properties and benefits associated with light gauge steel frames compared to other materials used for offsite technologies. It will also analyse how this type of frame can help reduce timeframes from concept to completion and examines some of the challenges that are encountered when using light gauge steel frames, including cost, transportability, and weight issues. Lastly, this article evaluates if there are any competing products or services that may be more beneficial than light gauge steel frames for offsite technologies.
What are the benefits of offsite technology?
Offsite technology is becoming increasingly popular in the construction industry due to its cost effectiveness, environmental impact and smart technologies. This form of prefabrication has revolutionised how buildings are designed and constructed, allowing for more efficient use of materials and labour. Offsite technology offers many advantages compared with traditional on-site building methods such as speedier production rates and less waste.
Smart technologies have also been incorporated into offsite technology systems to further enhance their efficiency and performance. These include automated processes that allow components to be produced quickly and accurately while eliminating potential errors from manual data entry or design alterations. Automated assembly processes reduce labour time associated with assembling parts on site, resulting in quicker completion times overall. Additionally, advanced software programs can track inventory levels throughout the entire construction process, enabling greater control over budgeting and resource allocation decisions.
Light gauge steel is durable, cost-effective and versatile
Light gauge steel is a type of steel construction that has become increasingly popular in recent years due to its increased durability, cost-effectiveness and versatility. It is often used for framing materials in offsite technology applications such as modular building systems or prefabricated components. Despite this popularity, the question remains whether light gauge steel is truly the most technically advanced material available within the portfolio of offsite technologies today.
To begin examining this issue one must first define light gauge steel and understand how it differs from other types of steel construction. Light gauge steel refers to thin sheets of galvanized or cold-rolled steel which are cut into pre-determined lengths using automated machinery. These pieces are then formed into specific shapes which can be joined together using bolts or rivets. This method creates strong but lightweight frames ideal for use in various structures including residential buildings, commercial complexes and industrial warehouses.
Compared to heavier forms of structural members made from rolled sections of hot rolled steels, light gauge steel offers significant advantages both economically and structurally. Not only are they lighter than their counterparts allowing for easier transportation on site, but their price point is also generally lower making them attractive choices for projects with tight budgets. Furthermore, since these frames do not require welding during installation, there is less risk associated with incorrect assembly or fire hazards caused by sparks generated through welding processes. This makes them especially well suited for high rise constructions where safety is a paramount concern.
In sum, while light gauge steel may not possess all the technical advances offered by some other alternative materials within the offsite technology portfolio, its combination of strength, affordability and ease-of-use make it an excellent choice for many different kinds of construction projects large and small alike.
What are the advantages of using light gauge steel framing?
Light gauge steel framing provides cost savings when compared to traditional stick-framing, as well as increased design flexibility and faster build times. Additionally, light gauge steel frames require less maintenance than other forms of construction, making them an attractive choice for many architects and builders.
The main advantage of using light gauge steel framing is its strength. The metal components are designed to be extremely tough and stable, meaning they can withstand high loads with minimal deformation over time. Furthermore, because the frame assembles quickly and easily on site, it reduces labour costs significantly. As a result, light gauge steel frames offer greater economic benefits than conventional building materials such as timber or concrete blockwork.
In addition to being strong and economical, light gauge steel frames also provide excellent thermal insulation properties due to their airtight nature. This means that heat transfer from outside sources is kept at a minimum while internal temperatures remain constant throughout different seasons. Moreover, the frames have exceptional acoustic performance which makes them suitable for use in areas where noise pollution needs to be reduced or eliminated altogether.
Types of steel used in construction
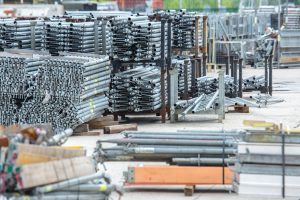
There are several types of steel used in the industry:
1. Cold-rolled steel
2. Galvanized Steel
3. Stainless Steel
4. Alloy Steel
5. Corten Steel
Cold-rolled steel is one of the most common varieties available and it is often galvanized to protect against corrosion. It has excellent formability properties and can be bent or formed into complex shapes with ease. Stainless steel is another type of steel commonly found in offsite construction projects, as it offers superior durability and strength compared to other steels. Alloy steels offer increased mechanical properties, making them suitable for applications that require higher levels of performance. Lastly, corten steel provides an aesthetic appeal due to its unique patina finish when exposed to weather conditions over time.
Offsite technology relies on these different types of steel depending on their desired qualities; cold-rolled steel offers good formability, stainless steel fulfils high durability needs, alloy steels provide enhanced performance capabilities, and cortensteel adds a unique decorative touch due to its changing appearance over time from exposure to various elements such as moisture and sunlight. Other types of steel also play significant roles in providing specific features needed for successful building projects.
Comparing steel against other building materials
When compared with other building materials such as wood construction, concrete framing, prefabricated panels, structural insulated panels and masonry construction, light gauge steel has some advantages but also certain disadvantages.
A recent survey found that 22% of builders prefer using light gauge steel for their projects due to its strength and durability. Light gauge steel frames are also ideal for smaller structures because they can be produced quickly and cost-effectively. Additionally, architects appreciate the design flexibility of this type of frame which allows them to create unique shapes with minimal effort. Furthermore, it’s possible to use lightweight materials like plastic or aluminium sheathing on these frames which reduces their overall weight and increases energy efficiency.
On the downside, however, light gauge steel may require more maintenance than traditional construction methods and is prone to corrosion if exposed to moisture over time. Moreover, there have been reports of premature deterioration in some cases due to incorrect installation or poor quality materials being used. Finally, while light gauge steel provides good insulation properties against sound and heat transfer, it cannot match the performance capabilities provided by alternative options such as masonry construction or structural insulated panels.
Technical specifications and requirements for light gauge steel framing
Light gauge steel framing has specific technical specifications and requirements that must be met to ensure its safe and effective use. The most important of these are related to the grade of steel used, as well as the components used for framing and installation.
Steel grades commonly used include cold-rolled structural steels with yield strengths ranging between 250MPa up to 550 MPa. The range of framing components available includes light-gauge metal sections such as studs, joists, trusses, purlins, rafters and braces along with their associated fittings such as nuts, bolts and screws. Installation requirements depend on the type of building being constructed but typically require a minimum foundation depth depending on soil conditions, wall spacing measurements according to Australian Standards (AS 1684), fire ratings for walls and ceilings according to AS 1530 Part 4:2014, fastening schedules outlined by AS 3566:2015 as well as insulation values determined using AS/NZS 4859 series standards where appropriate.
Quality assurance methods for light gauge steel framing
“A stitch in time saves nine.” This adage is an apt reminder of the importance of quality assurance when it comes to light gauge steel framing. Quality assurance (QA) methods are essential for ensuring that construction methods and techniques used to create a frame with structural integrity meet the required safety standards. Thus, QA measures should be performed on each component of a light gauge steel frame before assembly begins.
The most common QA measure employed during construction with light gauge steel framing is checking measurements against design drawings or blueprints. It is also crucial to make sure all components have been cut accurately according to specifications as even small variations can affect how the frame fits together. In addition, visual inspections should be conducted throughout the process to ensure that welds, fasteners, and other connections are properly installed and not damaged by environmental conditions such as rusting. Furthermore, tests can be carried out at various stages of production to verify strength levels and check for any potential weaknesses in the structure.
Finally, proper maintenance practices can help extend the life of a light gauge steel frame and guarantee its durability over time. Regularly inspecting frames for signs of corrosion or wear-and-tear damage allows contractors to address any issues quickly before they worsen and become costly repairs down the line. These preventative steps are vital for upholding long-term performance and overall value provided by light gauge steel framing systems.
Environmental impact of light gauge steel framing
As the construction industry continues to prioritise green building solutions, light gauge steel framing has become increasingly attractive as an environmentally friendly material option. This type of steel framing offers several environmental benefits that make it well suited for numerous applications in both residential and commercial buildings.
One of the primary advantages of light gauge steel is its high levels of recyclability. Steel production requires large amounts of energy, but when steel is reused or recycled, this reduces the overall amount of energy needed for manufacturing new materials. Additionally, since lightweight steel frames are made from thin sheets cut into specific sizes and shapes before being welded together, there is much less waste generated during installation than with traditional wood-framing methods.
The use of light gauge steel also allows for more efficient insulation systems compared to other materials used in offsite technology portfolios such as concrete or masonry blocks. Lightweight metal studs create air pockets that can be filled with insulating foam which helps reduce heat loss through walls or roofs and increases thermal efficiency within a structure’s envelope. Furthermore, since these structures require fewer resources to build and maintain while providing greater durability over time they often have longer lifespans resulting in lower long-term costs associated with upkeep and repairs.
Overall, light gauge steel provides many environmental benefits. Its low weight facilitates easy transport and quick assembly on site while its ability to support multiple types of finishes makes it suitable for a variety of design options allowing architects greater scope in their designs without compromising sustainability goals. In addition, its excellent thermal properties offer significant potential savings in terms of heating and cooling costs throughout the lifespan of any building constructed using this material.
Design considerations when using light gauge steel framing
The use of light gauge steel framing in offsite technology can be likened to a finely-tuned instrument, providing the perfect blend of design flexibility and structural integrity. When considering this material for construction projects, there are several key design considerations that must be taken into account:
- Building Regulations: Light gauge steel frames meet all building regulations standards across regions and countries, ensuring safety and security for occupants.
- Design Flexibility: Due to its strength-to-weight ratio and ease of installation, light gauge steel frames offer greater versatility than other materials when it comes to designing complex structures.
- Load-Bearing Capacity: Light gauge steel is one of the strongest materials available for load bearing capacity, making it an ideal choice for large scale projects such as commercial buildings or multi-storey complexes.
While there may be different factors at play depending on the specific project site, these three design considerations – building regulations compliance, flexibility in design, and load-bearing capacity – are fundamental when selecting a material like light gauge steel framing.
Challenges in producing and installing light gauge steel framing
Production of light gauge steel is a complex process that requires specialised machinery and expertise. It involves cutting, bending, forming, welding, and other processes to create the building components. The production of light gauge steel must be done in accordance with industry standards and regulations to ensure safety and compliance. Additionally, production can be expensive as it requires specialised labour and materials.
Installation of light gauge steel also poses some challenges due to its weight and size. Specialised equipment may be needed for lifting and maneuvering the large pieces into place on site. Furthermore, installation errors can cause serious structural issues if not addressed properly. Thus, proper training for installers is essential for successful execution of an offsite technology project using light gauge steel framing materials.
How cost-effective is light gauge steel framing?
The cost-effectiveness of light gauge steel framing as an offsite technology is difficult to measure and compare with conventional construction costs due to its relative newness. However, the potential savings associated with utilising such a material are significant. Light gauge steel frames use precision manufacturing processes that cut down on labour and time, which can reduce overall construction costs. Additionally, the frames can be designed for quick assembly in comparison to traditional structures, further reducing labour costs.
Light gauge steel also offers greater durability than other materials used in offsite technologies. The accuracy of the fabrication process eliminates errors during installation and creates a sturdier building structure that will stand up to wear over time better than other materials. This longevity allows builders to save money by avoiding costly repairs or replacements in the future.
What are the safety requirements for light gauge steel framing?
According to the Civil Engineering Portal, over 65% of all building codes adopted by U.S states require that light gauge steel meets specific fire protection needs. As such, it is important for builders to understand the safety requirements surrounding this type of technology before beginning any project.
The most common safety requirement pertaining to light gauge steel structures relates to fire resistance ratings (FRR). If an FRR rating is not achieved through correct design or installation methods, then additional measures may need to be taken in order to meet code regulations – including installing additional insulation or sprinkler systems inside walls and ceilings. Additionally, structural elements such as columns and beams should always adhere to applicable loading specifications in order for buildings to remain stable during extreme weather conditions like high winds or earthquakes.
Builders should also keep in mind that certain local governments may have their own set of rules when it comes to approving projects using light gauge steel frames. It is important for these professionals to do thorough research into their area’s regulations prior to designing and constructing a structure with this type of technology so they can make sure they are compliant with all necessary requirements. Furthermore, having a third-party inspector evaluate the work done on site will help guarantee compliance with all applicable standards and provide peace of mind that the job was done correctly.
How does light gauge steel framing compare to wood framing in terms of durability?
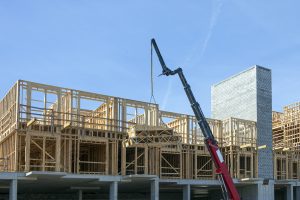
Light gauge steel has far greater strength than wood framing when it comes to resisting movement due to wind loads or seismic activity. This makes it ideal for areas prone to extreme weather conditions or earthquakes, as it will not warp or crack like wooden frames might do over time. The steel also doesn’t have issues such as termite damage that could potentially weaken the structure of a building if left unchecked. In addition, light gauge steel is non-combustible and can stand up better against fire than many other types of construction materials. These qualities make it an excellent choice for projects where safety and performance are top priorities.
When comparing the two materials on a more basic level, we find that light gauge steel offers several advantages over wood framing:
- Steel does not shrink or expand due to changes in humidity and temperature levels;
- Steel frames require less maintenance since they don’t need painting or staining like wood frames do;
- Steel frames offer superior soundproofing capabilities since metal absorbs sound waves much better than wood; and
- Steel is lighter in weight than wood but still provides adequate structural support for larger buildings.
From these points alone, one can see why light gauge steel would be preferred over traditional wooden structures in certain applications.
Are there any special tools or skills required to install light gauge steel framing?
When it comes to installing light gauge steel framing, certain special tools are typically required in order to complete the process. These include:
- An angle finder – used to measure angles accurately for cutting pieces of frame
- A jigsaw or reciprocating saw – used to cut holes into metal studs if those are needed
- A drill – used to make pilot holes in wood or other materials before screwing them together
- Specialised bits – used with the drill when working with different types of metals such as aluminium or stainless steel
In addition to these specialised tools, specific skills are also necessary when performing light gauge steel framing projects. Knowledge of basic carpentry techniques such as measuring, marking, drilling, cutting and assembling components is important in order ensure accurate alignment and proper fitment of parts.
It is essential that anyone attempting an installation project involving light gauge steel framing has access to these special tools and requisite knowledge about their use prior to undertaking any work on such structures; this ensures optimal results from these complex constructions without compromising structural integrity or code compliance regulations specified by government entities within each municipality where construction occurs. Additionally, obtaining assistance from experienced professionals who have extensive experience in this area can provide invaluable guidance during any stage of a build project using this type of material which could prove beneficial both financially and structurally over the life cycle cost analysis associated with each job site’s situation depending on the complexity involved.
What is the typical turnaround time for light gauge steel framing projects?
The average turnaround time for light gauge steel framing projects depends on several factors, including the size and complexity of the project, availability of materials, and any other specific requirements that may need to be met.
The size and complexity of a light gauge steel framing project will affect its overall timeline significantly. Smaller projects tend to have shorter turnarounds due to fewer material needs and less labour required. Conversely, larger or more complex projects require additional input from multiple departments or contractors which consequently leads to an extended completion date. Furthermore, when it comes to sourcing materials for these types of projects, delays can occur if stock is not readily available at the supplier’s warehouse. In cases like this where special orders must be placed there is often longer waiting periods before delivery is made and construction can proceed accordingly.
In addition to the elaborate processes already mentioned above, certain specifications regarding fire safety or acoustic performance may also have been specified by building regulations making them compulsory components within the design process. Thus ensuring all relevant tests have been completed adds further complexity into the equation thereby increasing total lead times even further.
It becomes evident then that accurately predicting how long a particular steel framing project will take requires detailed analysis across numerous interconnected variables in order for an accurate estimate to be formulated. As such, depending on individual circumstances each situation should be assessed carefully before committing to final timelines so that realistic expectations can be established right from the outset with minimal disruptions throughout its entire duration period.
What is the expected lifespan of light gauge steel framing?
The lifetime of light gauge steel frames depends on many factors, such as the environment in which they are installed, their maintenance regime and level of exposure to extreme weather conditions. Steel has excellent corrosion resistance properties, meaning that with proper care and protection from environmental elements, steel frames can have a life expectancy of up to 50 years or more. That said, if exposed to harsh weather conditions or poor maintenance regimes, then the frame may need replacing sooner than anticipated.
With careful consideration paid to protecting against corrosion and maintaining regular upkeep according to manufacturer guidelines; light gauge steel can offer significant lifespans without sacrificing any structural integrity or aesthetic character throughout its useful lifetime.
Future trends and opportunities for light gauge steel framing
The continued growth of light gauge steel framing is expected to open up new avenues for collaboration among industry professionals. As more companies begin to recognise the advantages of using lower cost yet highly durable steel frames, they are likely to form partnerships with firms specialising in related fields such as structural engineering or prefabrication services. Furthermore, advancements in digital technologies could enable more efficient design processes, thereby further expanding the scope of possibilities available through offsite technology.
These developments present an immense opportunity for those involved in building construction projects utilising light gauge steel framings. With access to newer methods for improving efficiency and accuracy during fabrication and installation, contractors can rest assured knowing their clients’ needs will be met without compromising on quality or safety standards. Moreover, lighter weight structures offer increased flexibility when designing large-scale projects – allowing architects greater freedom in creating unique designs while still meeting all necessary regulations.