Pre-Manufactured Value (PMV) is becoming a driving force in the specification of volumetric technology in public sector projects – particularly in healthcare and education. But Richard Hipkiss, development director for the Modular & Portable Building Association (MPBA), questions the value of purely financial calculations
Without doubt, Pre-Manufactured Value is a step in the right direction as the government drives to boost the uptake of Modern Methods of Construction (MMC) through the broader Offsite Construction Solutions framework, which encompasses volumetric and panelised building solutions.
As the name suggests, PMV is the financial proportion of a project’s gross construction cost derived through pre-manufacturing. It is a core metric for measuring the level of MMC in a project and is central to the UK government’s procurement programme.
Contractors are required to show that pre-manufacturing will account for at least 70% of all construction costs. This essentially plays to the strengths of a volumetric modular approach – so you might ask why I am questioning this?
Pre-manufactured value does not even have a standard definition
It is widely acknowledged that we do not have an industry-wide definition of PMV that stands up.
It has yet to be comprehensively defined and applied. As constructors move to respond, the accuracy of PMV calculations, particularly for the purposes of tendering, is something that has to be addressed.
Not only does it have to be precisely and consistently calculated but also has to be monitored to ensure fairness in the public sector procurement process.
PMV as it stands is a starting point but a barrier to progress is the need to rethink the scope and calculation of pre-manufactured value used in project procurement.
Currently metrics fail to account for the complexity and range of jobs that fall within the 70% PMV remit.
MMC has its origins in small scale residential housing, but is now used on major projects, from hospitals to infrastructure. The scale, diversity and complexity of projects also adds to the uncertainty about PMV’s accuracy and confusion opens doors for misinterpretation.
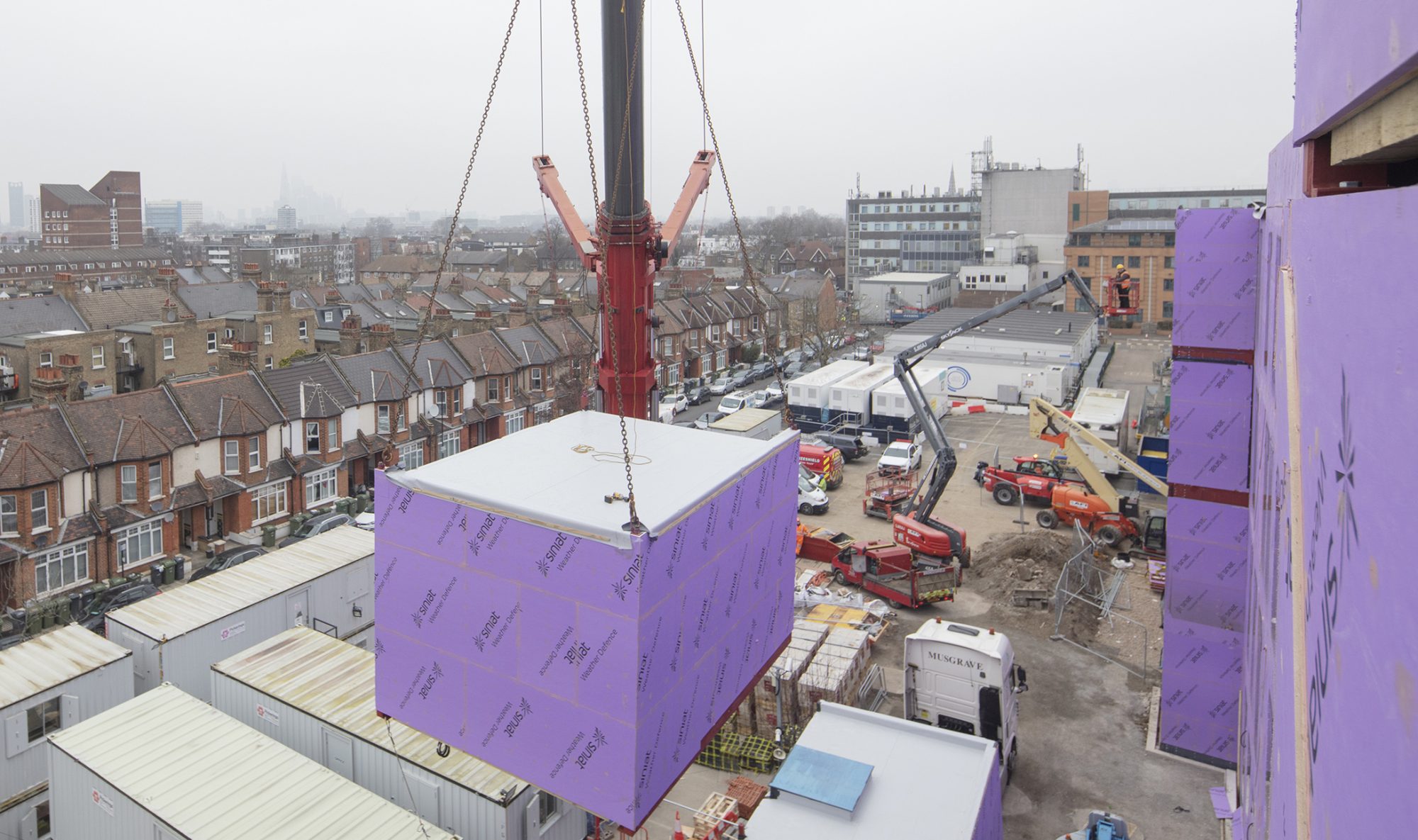
It would be good to see a standard calculation tool that can be regulated and legislated. We need greater education and clarity around PMV across the wider construction industry and standardisation of how it is calculated.
When you read the Construction Leadership Council’s definition of PMV, it appears to have been written by a quantity surveyor.
It is a commercial metric and rightly so as the government has to demonstrate best value, but PMV could be much more than this. One of the major benefits of pre-manufacturing and volumetric construction is reducing embodied carbon – which leads me to my second point.
Aligning construction costs with net zero
I accept this is very much in its infancy and there is more work to be done but the government has an opportunity here to align construction costs with net zero targets to demonstrate economic and environmental best value.
The government has set stretching net zero targets by 2050, so why is PMV’s calculated ‘value’ just in monetary terms.
Of course, demonstrating value for tax payers is critically important, particularly in these times of financial hardship, but as we all strive to reduce carbon in construction, is there not an opportunity here to include economic and environmental benefits within the PMV procurement scope?
As an industry association, it is one of our objectives to demonstrate how the route to 2050 could follow many different paths. It is now established that volumetric modular approaches reduce build times by an impressive 50-60% while increasing quality, productivity and safety.
But what is not so widely understood is that compared with traditionally built projects, it is easier to control energy use in factory settings than in an open construction site.
Carbon calculation provides a strong foundation for PMV metrics
On average, 67% less energy is required to produce a volumetric manufactured building and up to 50% less time is spent onsite, resulting in up to 90% fewer vehicle movements, which is less disruptive and reduces carbon emissions.
Not only is the actual construction of the building ‘greener’ but volumetric manufactured buildings are more energy efficient – reducing primary energy requirements and in-use operational emissions during the lifetime of the building.
Carbon calculators are now widely used throughout the offsite construction sector, and these could potentially form the basis for a PMV calculation tool.
I accept we have to get the fiscal calculations right first but by aligning financial and sustainability goals, public sector projects could expand the “value” criteria.
Richard Hipkiss
Development director
Modular & Portable Building Association
Tel: +44 (0)2475 90 1938