As the construction industry scratches its head wondering how to make the dream of volumetric MMC a reality, could a novel hybrid housing concept be the catalyst that finally drives it mainstream?
Construction technology start-up and serial innovator Sano thinks so and is putting its money where its mouth is with its intriguing new M-Dock product for single-family dwellings.
The idea of factory-built houses sold as products to solve humanity’s housing needs is a long-cherished dream.
People have been pushing for workable solutions, from the earliest mail-order kit homes in North America to the snazzy buildings of the high-tech era. The idea remained niche, though.
Even today, in the wake of the UK government’s Transforming Construction grand challenge, and despite unparalleled computer processing power and advanced manufacturing technology, it seems that the industry is struggling to deliver on the promise of MMC.
The long-cherished theory
That promise – of safer, quicker, more sustainable, higher-quality homes than is possible through traditional construction techniques – still looks good in theory.
Just as a car built in a factory has a much better chance of delivering long-term value than one cobbled together on someone’s suburban drive, a factory-built home should yield better outcomes than those built on-site.
Processes are optimised, waste is minimised, workers are protected, economies of scale are possible, on-site assembly is fast, and output quality is assured. You get efficient and effective pre-manufactured value (PMV): it’s a shoo-in.
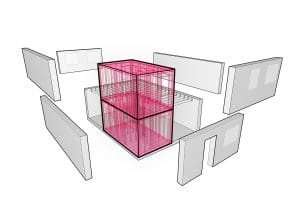
The frustrating reality
Unfortunately, the differences between housebuilding and car manufacturing are currently proving to be too great a barrier to driving MMC into the mainstream.
Over the past few years, high-profile ConTech innovators (including Katerra in the US and House by Urban Splash and Ilke Homes in the UK) have gone bust.
Commentators have diagnosed many possible factors for this failure: inconstancy of orders, planning constraints and logistical problems, disconnect between designers, manufacturers and assemblers, consumer preferences, etc.
The truth is that all of these probably apply to a greater or lesser extent, made worse by an industry stuck in its ways.
This inertia, combined with a lack of skills and factory capability, suggests that the changes attempted to date are too deep, fast and inflexible.
Is hybrid housing the solution?
Attempting to build a whole house in a factory, ship it in volumetric modules, and then assemble it onsite is a dramatic change to business as usual.
However, giving up on volumetric MMC entirely means leaving its potential benefits on the table, which is particularly difficult to envisage given the UK government’s commitment to MMC in its playbook.
Given this impasse, how should the industry respond? Sano believes the answer is to implement a hybrid housing approach – with only certain specific, difficult-to-get-right, high-value parts of a house standardised and built offsite, with everything else built traditionally.
Factory quality and design flexibility: The best of both worlds
In their thinking, this gives you the best of both worlds. On the one hand, you have the flexibility to tailor the building to the needs of the site, the local planning conditions, the developer’s business case and the end-user. On the other hand, you can control the quality of the more technical parts of the house by building them in a factory.
Sano’s M-Dock product does precisely this. The “M” bit stands for Module or Mod. The “Dock” bit refers to the onsite part of the build that the Mod plugs – or docks – into.
Sano’s solution cleverly concentrates all the MEP controls and most plumbing (common points of failure) into the Mod for quality control.
Designed as one repeatable, standardised template with several slight variations, the system comprises a first-floor Mod that stacks on top of its ground-floor twin to form a front door, entrance hallway, stairs, toilets and bathroom.
The Mods sit inside the building’s thermal and structural envelope and have a proprietary system for anchoring back to ‘dock’ living spaces. This way, designers have total freedom about how they design and finish the rest of the house. Note that Sano has worked out several generic whole-house designs using the M-Dock system that takes the headache out of designing them afresh.
The M-Dock advantage
The advantages of this patent-protected system are evident, overcoming the barriers presented by manufacturing whole houses. By building the low-failure point majority of the house on-site, factories building Mods don’t have to be so large or so highly geared. You also avoid the costs, carbon footprint and logistical barriers of transporting lots of modules to potentially awkward sites.
Depending on the developer’s appetite for innovation and as the industry matures, the on-site parts of the system are amenable to being built using offsite panels or even 3D printing techniques, increasing the development’s overall PMV. Even without it, the M-Dock system achieves a PMV score of 70+.
Solving the housing crisis
In short, Sano’s M-dock system solves many of the difficulties modular housebuilders face. It allows them to evolve away from on-site practices at a manageable pace that keeps up with their skills mix and ways of doing business without losing out on the benefits of offsite.
The UK’s ongoing housing crisis makes it imperative that we find new and better ways to build. This will become especially urgent if, as polls suggest, the Labour Party wins the next election and follows through with its commitment to build 1.5m new homes. Deployed in bulk, Sano’s M-Dock system and hybrid housing will likely be part of the solution.
Sano is finishing its first test house as a proof-of-concept in partnership with SIPco. They urge developers, registered providers, architects, contractors and anyone else to contact the test house and discuss technological innovation, smart manufacturing and how M-Dock could be part of your build programme.
David Jones
Co-Founder
Sano
Tel: 07949 829594
*Please note: This is a commercial profile.