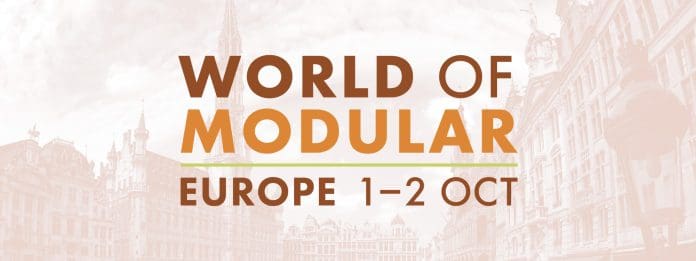
John McMullen, PCM and marketing director of the Modular Building Institute, looks at the exciting offerings at World of Modular Europe
Modular and offsite construction are nothing new to European building stakeholders. Still, with the rate of industry innovation and evolution around the world, continuous education, networking, and knowledge sharing is key. To that end, the Modular Building Institute (MBI), the world’s largest international trade association for the commercial modular construction industry, is bringing its premier event to the heart of Europe in October, 2024.
World of Modular Europe, to be held in Brussels on 1-2 October, will be an event like none other. Featuring speakers, exhibitors, and attendees from across Europe and around the globe, World of Modular Europe will be a world-class forum, offering key insights, best practices, and the opportunity to meet leaders and stakeholders from every corner of industry.
Examining the state of modular construction in the UK and Europe
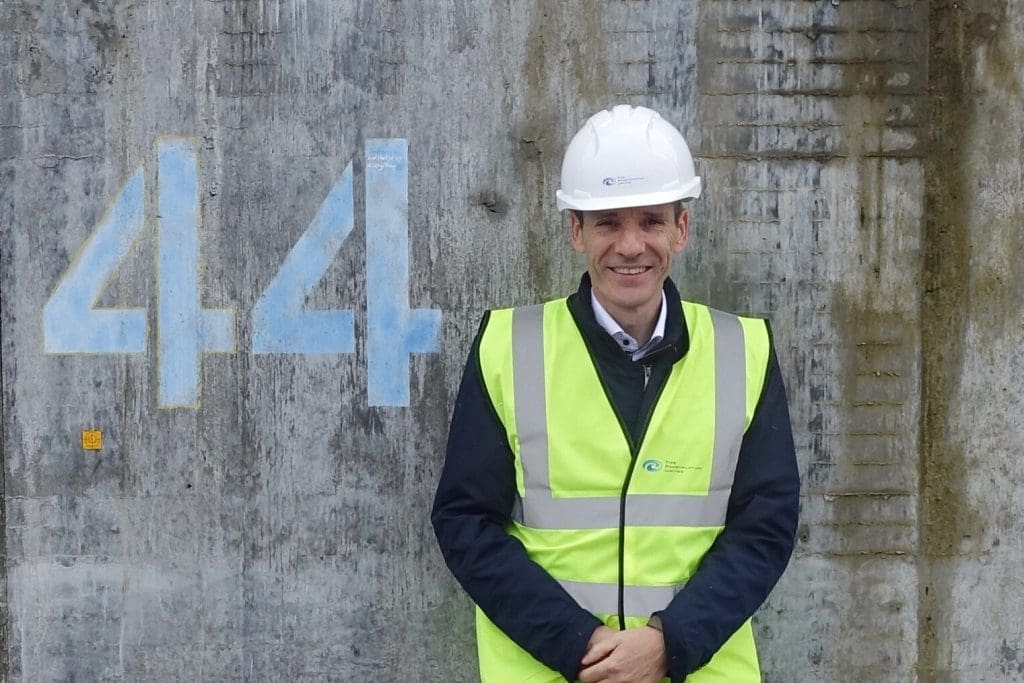
Speakers from around the UK and Europe will be presenting at World of Modular Europe, including Michael Hough, principal at Ireland’s MJH Structural Engineers, and Franco Vietti, associate at Holland-based Green Prefab. Both Hough and Vietti will be sharing—among other things—their insights on the industry based on their 20-plus year careers.
“Recently,” says Hough, “the UK government conducted an enquiry into the barriers to modern methods of construction (MMC) to see how government may assist with improving the output of housing. In broader terms, there appears to be a move towards some level of standardization within the industry, through platforms and repetition. While there is a place for standardized platforms in the industry, I believe that this is just one piece of the puzzle in the goal to redefine the construction industry and improve productivity in line with the developments in technology in society.”
Outside the UK, adds Vietti, “Europe is steadily increasing the premanufactured value of each building project by moving towards the adoption of not just one particular offsite system, but a combination of systems depending on each application. From my perspective, hybridization—combining different prefabrication methods—is the best approach to industrializing the sector in Europe, especially from the developer’s standpoint, in order to mitigate the risks of a yet-to-develop broad supply chain.”
Ultimately, says Hough, “in order to move the needle towards general acceptance of modular construction we need to see the promotion of innovation, flexibility and the adoption of more modular solutions to construct more and more statement buildings.”
Exploring the barriers to MMC adoption—and the opportunities that lie ahead
“Europe is a complex landscape shaped by stringent regulatory frameworks,” says Vietti, “which can vary significantly from one country to another, and even between regions within the same country. In some cases, there is strong support from governments, but this doesn’t always yield efficient and quick results. Like everywhere, governmental initiatives to quickly solve long-term structural problems, such as housing shortages and emergencies, are often less effective in boosting the industry than addressing inefficiencies and bureaucracy, allowing the private sector to take the lead.”
That said, “modular construction is still very much in its infancy,” adds Hough, “with no clearly defined system operating across all markets. There are pockets of Europe where modular is very prolific, such as Sweden, and plenty of countries where it has not taken off at all yet. The flexibility in codes in Europe…allows innovation but also requires that the construction system is proven to do so, as well.”
“Modular volumetric construction is showing strong performance as a delivery system for commercial buildings, including healthcare, education, student accommodation, and build-to-rent developments,” says Vietti. “There is also increasing interest in data centers and other mission-critical buildings. It is important to note that these markets are also targeted by real estate developers during economic downturns, and modular volumetric construction stands as a perfect solution for them. Within these groups, companies with diversified business models and a more service-oriented approach are outperforming the design-build ones, especially those targeting affordable housing.”
As for Hough, he says “medium-rise modular construction is probably where the most benefits are being realised around Europe right now. The split between site and factory is good and the parallel constructions have a large effect on program and the overall bottom line for a project. For some modular manufacturers, once adequate repetition is achieved vertically to allow viability of a project, then additional flexibility in horizontal changes to module layouts may be accommodated. These effects are increased in high rise construction, and we would like to see the high rise modular construction market increase in size with other companies entering the market building increasingly taller modular buildings and providing much needed homes in urban centers.”
Setting the stage for World of Modular Europe
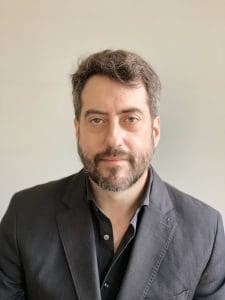
“At the World of Modular Europe,” says Vietti, “I will focus on the opportunities for modular construction to truly enter the service economy. The service economy, comprising nearly 80% of developed countries’ economies, has been boosted by the sharing economy and new generations’ behaviors emphasizing ‘using versus owning’ assets, favoring an asset-light strategy. This trend presents a significant opportunity for the modular industry, as modular building allows one to own and service flexible building solutions for clients. In other words, there will be a transition from fixed real estate building assets to dynamic relocatable building asset solutions, creating outstanding opportunities for development.
“We call it Modular Building as a Service (MBaaS). This will revolutionize the commercial real estate industry by transitioning from traditional ‘product and space’ offerings to dynamic ‘system and service’ solutions, boosted by advanced automation and AI. In my presentation, I will explore this new concept and how it can be a disruptor for the industry.
“Additionally, I will examine the performance of different business models, including design-build, operating lease, and MBaaS in the modular industry. I will discuss how diversifying business models is a winning strategy for manufacturing companies looking to mitigate risk and increase profitability, investment opportunities, and return on equity for investors, developers, and asset managers.”
And in his presentation, Hough will track the evolution of modular construction in UK—with a focus on his recently completed work for the 50-story College Road Croydon project—to see what further advantages lay ahead.
“If anything has been learned in the last few years,” says Hough, “it is that a revolution in construction is difficult for many reasons. We will outline the progress in modular from the early 2000’s up to the current levels of construction and show what has been happening. We will showcase projects and the progression of modular construction over the years.
“Our latest completed project, College Road Croydon,” concludes Hough, “provided homes at a rate of more than one per day for the duration of the construction program in a building with seven levels of amenities. This is achieved only by the parallel processes of site and factory in tandem, the nature of the occupancy and using offsite to minimize the program. We would aim for the main takeaways to be the potential and successes of modular as it moves into more mainstream construction.”
Join the Industry in Brussels, 1-2 October
“Taking part in World of Modular Europe excites me because it provides a unique platform to connect with industry leaders, innovators, and visionaries from around the globe,” says Vietti.
“I would not have worked all over the world and be collaborating with Green Prefab if not for an MBI event. These events foster knowledge sharing, collaboration, and the exchange of ideas that drive the industry forward. I am particularly eager to learn from my peers, discover new trends and technologies, and contribute to the ongoing dialogue about the future of modular construction. And maybe come back home with some new projects.”
See all speakers and presentations for World of Modular Europe and register today.