Co-location developments are an emerging trend. Could this be an answer to helping solve the housing crisis, with high demand for both industrial and residential developments? Why not integrate the two uses? Peter Watkins, director of HDR|Bradbrook explores
A co-location scheme is a mixed development model, where new homes lie in close proximity to other uses, such as light industrial, retail, offices and other classes of use.
This article explores the design and engineering challenges around the integration of industrial and residential developments with a focus on the city of London.
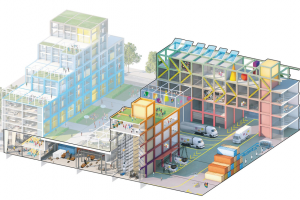
The demand for housing and industrial space
With limited land availability in London and the emergence of e-commerce over the last 5 years, industrial developers are competing with residential developers for land. As the need for housing and industrial space in cities grows, we’re starting to see the two sectors merge to explore opportunities on how industrial and residential can co-exist and operate harmoniously.
Consolidation, intensification and co-location of uses, to grow and retain industrial space is supported by the new London Plan. Landowners in London are therefore considering the consolidation of assets to maximize land value, exploring the viability of co-location developments with multiple uses, looking to either refurbish to free up lettable area, demolish in part or whole to accommodate other uses.
The population in London has grown 7.5% in the last 5 years to an estimated 9.3m and it was predicted to grow by a further 5% in the next 5 years. A recent report for the British Property Federation by Turley estimated that on average in the UK, 69ft2 of additional storage space is required for every new home built. With the government targeting to build circa 65,000 new homes in London this equates to approximately 4.5 million sqft of new warehouse space needed, an area approximately the size of 330 Olympic swimming pools.
These population predictions were made pre-Covid 19. The impact on how and where we work in the future is likely to change radically as we negotiate our way through this pandemic. This could potentially lead to London’s population contracting in the next few years as more people are able to work remotely from outside of Central London. However, there will undoubtedly still be a requirement for additional storage space to augment new housing.
Consumer behaviour is evolving and there is an increasing demand for last-mile logistics as retail trade is increasingly being driven by e-commerce. The Office for National Statistics survey findings show that 20% of all retail sales are currently online and this is predicted to continue to grow over the coming years.
The impact of Covid-19
In addition, the Covid-19 pandemic has accelerated the growth of e-commerce. With shops temporarily closed and the public on lockdown, shoppers have been forced to turn to on-line shopping. This trend is likely to continue in the future as peoples buying habits change.
Many of the elder generation are having to use technology-enabled services for the first time, such as online food shopping and communication tools like, Microsoft Teams and Zoom. As this generation becomes more comfortable with technology their behaviours are likely to change permanently and many of them will continue to use these services when the pandemic passes. This will further accentuate the growth in urban logistics hubs.
Before the global crisis of Covid-19, CBRE predicted that e-commerce will represent over a third of all retail sales by 2040. This additional growth predicted above will require more and bigger warehouses in cities.
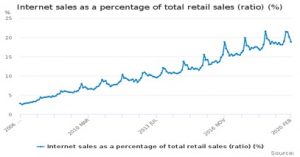
Co-location engineering challenges
In collaboration with the design team the structural engineer has a fundamental part to play in the resolution of all these key technical factors. The primary role of the engineer is to design the most efficient structure that maximizes flexibility and minimizes complexity, whilst meeting the client’s objectives.
The structural engineer must determine what the most economical framing system is? How the structure will resist lateral forces, such as wind and how it will safely transmit the high building loads to the foundations, whilst ensuring that all the site constraints are taken into consideration.
Most Industrial type buildings are typically constructed with a steel frame due to the need for clear internal spaces, resulting in long-span structural elements. The lateral stability is usually provided by a combination of cross-braced bays and portal frames. However, in contrast to industrial buildings, multi-storey residential buildings are typically constructed with a reinforced concrete frame, with flat slabs and blade columns.
The spans between columns are relatively modest and columns can be hidden within party walls. Lateral stability for this type of development is usually provided by reinforced concrete lift/stair core walls. A concrete frame solution offers benefits over other materials in terms of its inherent thermal mass, fire protection, robustness and acoustic performance.
Thus, when these uses are combined, the most efficient structure is not that obvious and the result in theory might be a hybrid steel and concrete framed structure. However, combining materials introduces additional complexity in the design and in particular how the materials connect.
The interface between two materials is likely to occur at a transfer structure over the industrial space. Transfer structural elements supporting multi-storey residential apartments over long span industrial spaces can be significant in terms of size and cost. It is important when assessing the possible solutions to consider all viable forms of construction. Not just the materials cost, but also buildability, material weight, programme and the distribution of services.
Close collaboration with Architects is essential to co-ordinate the interfaces between the uses to minimize the extent of any transfer structures. The recommendation to avoid unnecessary complexity and cost is to align the structural cores resisting lateral forces up through every floor.
The extent of columns within the industrial floor space must be carefully coordinated with the architects and will be limited to maximize flexibility of use of the floor area, and to allow for HGV circulation and storage.
The magnitude of loading on the vertical elements is also significant, (mega newtons rather than kilo newtons). Consideration should be given to use of high strength materials and lightweight materials, lightweight facades, polystyrene void formers in landscaped areas and lightweight floor build-ups.
Façade structure interaction is another technical factor, it’s important to minimize the weight of the façade system, this will assist in reducing deflections on the slab edge, and more importantly it reduces the column loads. This in turn limits the effects of compound deflection on transfer beams supporting these columns.
Vibration impacts on co-location developments
Other technical challenges include structure-borne vibration, generated by the industrial operations. This is a potential risk to the residential occupants and may require mitigation measures. Structure-borne vibration results from an impact on, or a vibration against, a part of a building structure resulting in sound being radiated from an adjacent vibrating surface through the frame.
The main sources of structure-borne vibration associated with industrial operations are likely to be:
- Vehicular movements (Vans/HGV’s/Forklifts) tracking on the slab.
- Vibration of mechanical plant systems attached to the structure.
- Vehicular/accidental load impacts on structural columns & walls.
- Accidental impacts from dropped objects (pallets/containers) on the structure.
- Gantry Crane movements.
To determine the magnitude of these potential vibration sources a detailed vibration modelling assessment is required during the detailed design phase of the project.
Mitigation measures if deemed necessary would likely entail some form of vibration isolation. The illustration below indicates two typical solutions on how this could be achieved. The relative merits of these options and other potential solutions would clearly depend on the individual constraints of the project.
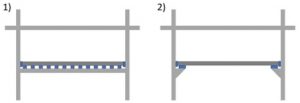
Co-location engineering impact on sustainability
Industrial/residential co-location developments by their nature of having complex and heavy structural elements will result in increased levels of embodied energy and carbon, if not efficiently designed.
Structural engineers can influence the design to improve the efficiency of a building. The use of light weight forms of construction such as timber or light gauge steel where viable, will minimize the building weight to reduce the extent of concrete foundations or transfer elements. Optimizing structural column grids to achieve thinner slabs, the use of post-tensioned slabs, specifying high-strength materials and recycled aggregates will all result in less concrete being used and a greener, leaner structure.
The future of co-location
These are certainly unprecedented times, our industry is currently facing three of the biggest challenges in tackling a global pandemic, driving climate change and BREXIT.
The uncertainty surrounding these unprecedented times has slowed the construction industry. I’m optimistic that as a resilient nation the wheels will keep turning, the future for the mixed development model is bright and this will continue to be driven over the next few years by the demand for housing and the growth of e-commerce.
As technology and e-commerce continue to grow the next big challenge for the Engineer could be multi-storey beds over multi-storey sheds.
Peter Watkins BEng CEng MICE FIStructE
Director