The Building Cost Information Service (BCIS) Has released their latest forecast, detailing rises in both costs and tender
Read our Building Materials and Components: December 2024 Commentary breakdown here:
1. Overview of building material prices
- General price trends:
Building material prices for all work rose by 3.5% year-on-year in December 2024. While this represents a decline in the rate of growth compared to earlier in the year, materials remain historically expensive. Prices increased by 0.7% compared to November 2024.
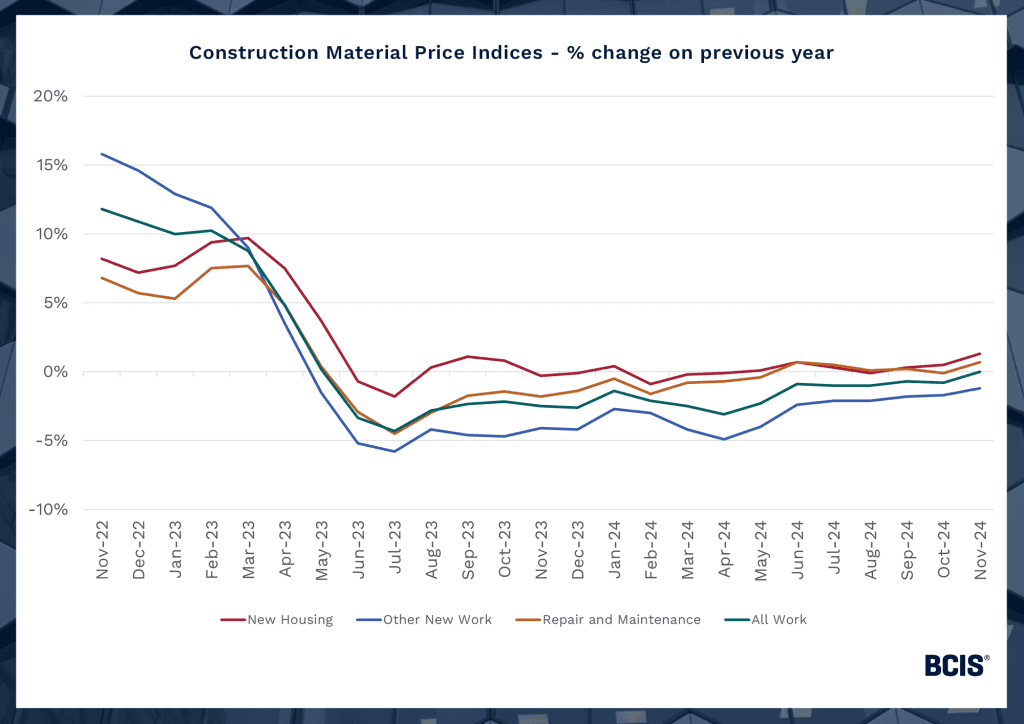
- Key materials:
-
- Timber: Prices for sawn and planed wood stabilised after a sharp rise in 2023, reflecting improved global supply chains. However, demand remains high for structural timber, sustaining higher price levels.
- Steel: Reinforcing steel prices rose by 5.2% year-on-year, driven by energy cost increases and global demand in infrastructure projects.
- Cement and concrete: Cement prices rose modestly by 2.1%, with ready-mixed concrete showing a similar trend. Supply constraints have eased compared to 2023.
- Bricks: Prices rose 4.8% year-on-year, with demand from residential projects pushing up costs. Manufacturers report increased capacity to meet demand.
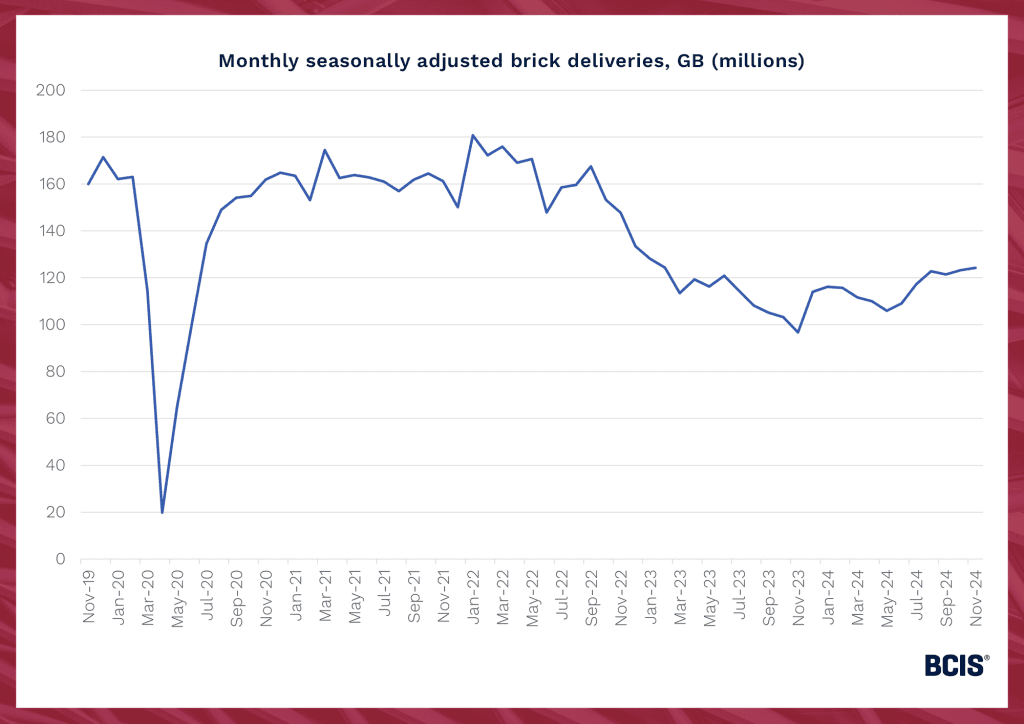
2. Supply chain dynamics
- Import and export trends:
-
- Imports of construction materials declined by 1.5% year-on-year, reflecting the stabilisation of domestic production.
- Exports of UK-produced materials increased by 2.3%, led by insulation and architectural metal products.
- Key import markets for the UK remain EU countries, China, and the USA. Disruptions in global logistics have reduced compared to 2023.
- Domestic production:
Domestic production of key materials such as aggregates, bricks, and concrete improved in 2024, reducing reliance on imports. This has been facilitated by investments in production capacity and modernisation of manufacturing plants.
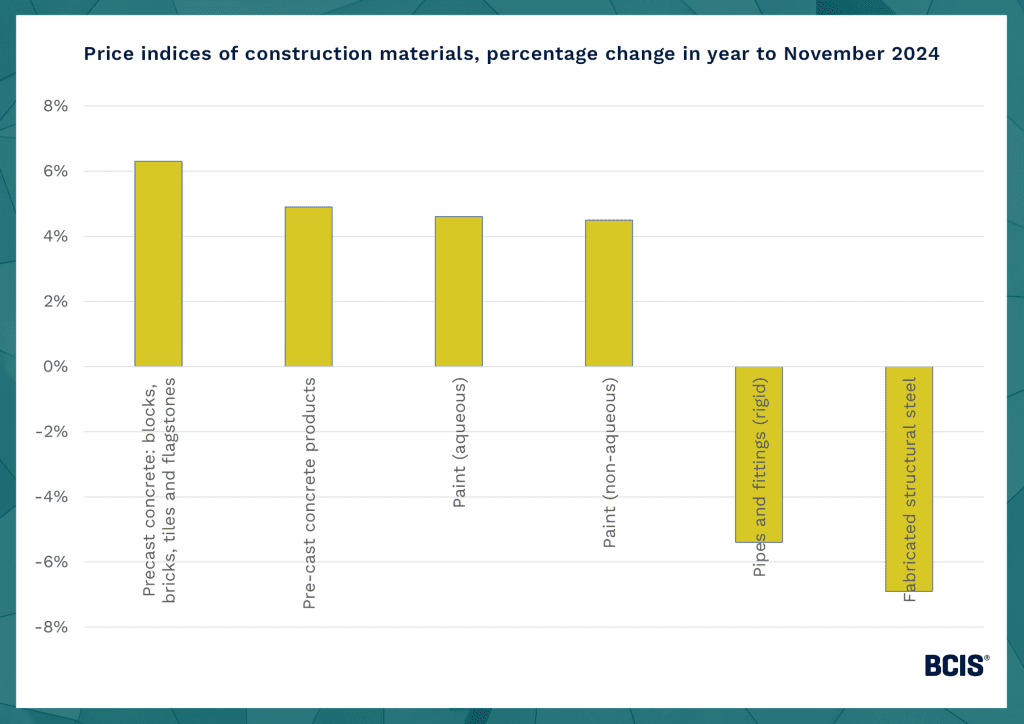
3. Sector-specific insights
- Residential construction:
High demand in residential building continues to drive the market for bricks, cement, and timber.
Material costs, especially for insulation and roofing materials, remain significant factors influencing project budgets. - Infrastructure and civil engineering:
Increased government spending on infrastructure projects, such as HS2 and renewable energy initiatives, has driven demand for steel, aggregates, and concrete.
Supply chains have adapted to meet specific project requirements, with targeted imports of high-grade materials. - Renovation and repair:
The repair and maintenance sector saw steady growth, boosting demand for materials like plaster, paints, and lightweight construction components. Supply chain improvements have eased delivery times for these items.
4. Energy and transportation costs
- Energy costs remain a major contributor to material price inflation. The continued volatility in energy markets has particularly impacted materials like steel and cement, which are energy-intensive to produce.
- Transportation costs stabilised in late 2024 due to improved global fuel prices and logistics efficiency, though they remain higher than pre-2020 levels. This has benefited the timely delivery of construction materials across the UK.
5. Sustainability and innovation
- Recycled materials: The use of recycled aggregates and eco-friendly building materials has grown as contractors seek to meet sustainability targets.
- Low-carbon cement: Adoption of low-carbon cement products increased significantly in large-scale projects. Manufacturers are investing in reducing the carbon footprint of production processes.
- Offsite construction: Prefabricated materials and modular components saw increased uptake, improving construction timelines and reducing waste on site.
6. Regional differences
- Material price increases and supply challenges varied by region:
-
- London and the South East: Higher costs due to demand in commercial and residential construction.
- Northern England: Moderating price pressures as demand stabilised after significant infrastructure investment.
- Scotland and Wales: Higher logistics costs affected materials like timber and steel.
7. Challenges and opportunities for 2025
- Challenges:
-
- Continued energy price volatility may influence the cost of production for key materials.
- Labour shortages in construction manufacturing sectors could hinder the expansion of domestic production capacities.
- Fluctuating global demand, particularly in markets like China and the US, may impact UK material prices.
- Opportunities:
-
- Expanding the adoption of sustainable materials could help reduce costs and environmental impact.
- Investments in domestic manufacturing could shield the UK from future global supply disruptions.
- Advances in material technology, such as graphene-based composites, may create new efficiencies in construction projects.
Costs for civil engineering are forecast to rise by 17% over the next five years to Quarter 3 2029, and civil engineering tender prices are forecast to rise by 19% in the same period.
New work infrastructure output is also expected to have seen a 8.9% decline in 2024.
Growth is also expected in the BCIS infrastructure forecast
Despite a decline last year, new work infrastructure output is also expected to recover quickly and grow by 18% in the next five years, specifically due to growth in the electricity sub-sector.
The BCIS infrastructure forecast is produced covering projected input costs, tender prices, and output, and is calculated through the lens of construction market trends, and is intended to inform the market on what to expect for the year.
The All-in Tender Price Index measured the trend of contractors’ pricing levels in accepted tenders, recording a growth of 2.3% in Q4 2024.
In terms of input costs the main driver is labour, with an annual growth in the cost index predicting a slowing to 5.3% in Q4 2024.
National Insurance contributions increased, and the National Living Wage is predicted to impact labour costs, with an increase of 2.5% predicted in April-March, and an overall increase to the BCIS Labour Cost Index of 19% predicted up to Q42029.
Materials cost inflation has been gradually slowing ever since its peak in 2022, with an annual growth in the Materials Cost Index in the negatives from Q3 2023 to Q2 2024. Therefore, the index is expected to grow by 15% to Q3 2029.
Overall output figures have remained low, with the recorded data to Q3 2024 decreasing by 4.1% compared to Q3 2023.
“We do expect to see housing output increase”
Dr David Crosthwaite, chief economist at BCIS, said: “Industry sentiment data continues to present positive readings, although since the Autumn Budget these are now less optimistic than at the time of our previous forecast in September, when the headline S&P Global UK Construction Purchasing Managers’ Index reached a 29-month high.
“We’re predicting that prices will grow more slowly than input costs in 2025 and that this trend will reverse from 2026.
“Given the continuing tightening of the supply side, the long-term loss of employment in the construction labour force, prevailing shortages of skilled labour and an expected uptick in demand this year, the risks to this forecast remain on the upside.
“We’re expecting new work to have contracted by 4.7% overall in 2024 as a result of declines in most sectors. We’re forecasting a return to growth from 2025, with recovery fuelled by housing and infrastructure spending.
“Although the government’s ambitious targets for housebuilding may remain simply an ambition at the volumes they’re aiming for – to achieve 370,000 homes annually, annual construction output for housing would need to see a 68% increase on 2023 levels – we do expect to see housing output increase.
“However, the state of the public finances puts much public spending at risk and the sluggish economy will likely dampen growth in both industrial and commercial sectors.
“It’s unfortunate that the second phase of the government’s Spending Review has been put back to June as many funding and viability decisions are reliant on a transparent pipeline of work and long-term commitment to a growth strategy.”